Open Access
ARTICLE
Fabrication and Comparative Properties of Sustainable Epoxy Methacrylate of Bisphenol-C-Jute/Treated JuteNatural Fibers Sandwich Composites: Part-2
Department of Chemistry, Saurashtra University, Rajkot-360 005, Gujarat, India.
* Corresponding Authors: e-mail: and
Journal of Polymer Materials 2022, 39(3-4), 223-239. https://doi.org/10.32381/JPM.2022.39.3-4.4
Abstract
Compression-molded epoxy methacrylate of bisphenol-C-jute/treated jute-banana/groundnut/ cane sugar/pineapple leaf/rice husk/wheat husk sandwich composites were fabricated under 5 MPa pressure at room temperature for 3 h. Alkali treated jute-natural fiber sandwich composites displayed considerably improved mechanical properties over untreated jute-natural fiber sandwich composites due to surface modification of the jute fibers. Both types of sandwich composites showed high water uptake tendency, excellent hydrolytic stability against acids, alkali, and salt solutions, and also a longer equilibrium time at 30o C. Alkali treated sandwich composites revealed a considerably lower water uptake tendency than untreated sandwich composites. Observed water uptake trend is H2 SO4 > HCl >NaOH >H2 O>NaCl.Keywords
The majority of polymers are well known as barriers to water uptake. Most widely they are used in packaging, food, pharmaceutical, and rubber industries to reduce undesirable moisture uptake. Agricultural resources like plants, crops, and pods are renewable biomaterials that support the ecosystem and socio-economic development of the green society. The demand for greener and biodegradable natural fiber-reinforced composites are increasing rapidly due to their easy accessibility and abundance, renewability and biodegradability, low-cost, eco-friendly production, low density, reduced wear, high specific strength, good physical, mechanical, and decomposition properties[1–4]. These attractive features of biomaterials are value-added in making bio-composites for various applications.
Natural fibers can be extracted from bast, leaf, seed, stalk, grass, and wood and are used to manufacture composites for aerospace, transportation, railway coaches, automobile, packaging, sports, home appliances, consumer products, acoustic insulators, building, and construction applications[5, 6]. Cellulose, hemicellulose, lignin, wax, and pectin are the chemical constituents of the natural fibers[7]. Chemical compositions of natural fibers govern the physical and mechanical properties of natural fibers and hence ultimately affect the characteristic properties of the composites[8, 9]. The main drawback of natural fibers is their hydrophilic nature, incompatibility with hydrophobic matrices, thermally unstable, and inferior interfacial bond strength. These problems can be improved to a greater extent by fiber surface treatments and for that various chemical treatment methods are available in the literature[7, 10-12] to improve compatibility, hydrophobicity, interfacial bonding, and surface roughness of the natural fibers which lead to better tensile strength, flexural strength, impact strength, and interfacial shear strength of the composites.
Most of the researchers have utilized bisphenol-A-based epoxy resin or unsaturated polyester resin in making economic and sustainable natural fiber-reinforced composites and exploited their possible industrial applications. To the best of our knowledge, no other researchers have utilized epoxy methacrylate of bisphenol-C matrix material for the development of fiber-reinforced composites. We had developed epoxy resin of bisphenol-C-based fiber-reinforced composites and characterized them for their plausible applications[13-19]. We have also developed semisolid and liquid epoxy methacrylate of bisphenol-C in our laboratory. Semisolid epoxy methacrylate was found difficult to handle so we had prepared liquid epoxy resin and its methacrylate for easy handling. Prepared resin was used in making value-added glass/ untreated jute/treated jute/jute-natural fiber/ treated jute-natural fiber-reinforced composites[13-19]. In our recently published work[18, 19], we had used various natural fibers namely white coir, brown coir, wild almond, bamboo, betel nut, palmyra, banana, groundnut, cane sugar, pineapple leaf fibers, rice husk, and wheat husk in combination with glass/untreated jute/treated jute fabrics. The composites revealed promising mechanical and electrical properties; and excellent chemical resistance against acids, alkali, and salt solutions[13-19]. The present work deals with the utilization of liquid epoxy methacrylate of bisphenol-C[16] in fabricating sandwich composites. For that, we have used jute/treated jute in combination with banana fibers, groundnut fibers, cane sugar fibers, pineapple leaf fibers, rice husk, and wheat husk. Our motto was to prepare economic and sustainable epoxy methacrylate of bisphenol-C-jute/treated jute-natural fiber-reinforced sandwich composites and search their industrial utility. Mechanical and electrical properties and chemical resistance of the sandwich composites are evaluated and compared with neat and untreated jute/treated jute composites.
Laboratory grade solvents and chemicals used in this work were purified by appropriate methods[20] or used as received. The liquid epoxy methacrylate of bisphenol-C (EMABC)[16] was synthesized according to the following Scheme-I: A 40% styrene solution of EMABC (EMABCS) was used for the preparation of the sandwich composites. Methylethylketone peroxide (MEKP), 6% cobalt octoate and mylar film were supplied by EPP Composites, Rajkot, as free samples and were used as received. Jute fabric (J) (350 GSM) was purchased from a local market (Rajkot). Surface modification of jute fabric was done using 4% sodium hydroxide solution at room temperature for 12 h[21] and designated as TJ.
Scheme-I:: The synthesis of epoxy methacrylate of bisphenol-C
Various natural fibers (NFs) such as banana fibers (B) (Musa acuminate), groundnut fibers (GN) (Arachis hypogaea), cane sugar fibers (CS) (Blue agave), pineapple leaf fibers (PA) (Pina), rice husk (RH) (Oryza sativa L) and wheat husk (WH) (Triticum) were collected from the local resources. Collected fibers were cleaned, washed several times with distilled water, and dried in an oven at 50°C for 48 h. Dry and cleaned fibers were cut manually into 1-2 mm size and stored in airtight containers. Natural fibers possess different physical properties and different chemical compositions[7] (31-83% cellulose, 12-33% hemicellulose, and 5-30% lignin) and 8.5-17% water uptake tendency.
Preparation of Controls and Sandwich Composites
The control samples namely EMABCS[16], epoxy methacrylate of bisphenol-C-jute (EMABCS-J), and epoxy methacrylate of bisphenol-C-treated jute (EMABCS-TJ)[17], and compression-molded sandwich composites[19] were prepared according to our recently published work. The details of sandwich composites are described in Table 1. The sandwich composites are designated as EMABCS-J/TJ-B/GN/CS/PA/RH/WH. For tensile and flexural testing, the samples were prepared as per standard test methods. For tensile strength measurements, widths and thicknesses of the composite samples were 8.34-10.49 mm and 4.25-7.37 mm, respectively, and that for flexural strength measurements, they were 12.05-12.52 mm and 4.25-7.16 mm, respectively. For the water uptake study, 2cmx2cm samples were cut from the respective sheets and sealed using corresponding resin solutions and cured at room temperature, and post-cured in an oven.
Tensile strength (ASTM-D-638-01) and flexural strength (ASTM-D-790-03) measurements were carried out at a speed of 10 mm min-1 on a W & T Avery Ltd. Type 1010 Model No E-46234 (Birmingham, England). Izod impact strength (ASTM-D-256-06) tests were carried out on an Izod Impact Tester Model No.E-46204 Type A-1300 (Birmingham, England). Electric strength (IEC-60243-Pt-1-1998) quantifications were performed in the air using 25/75 mm brass electrodes on a high voltage tester (Automatic Electric-Mumbai). Volume resistivity (ASTM-D-257-2007) tests were done in the air at 25°C after 60 s charging at 500 V DC applied voltage on a Hewlett Packard high resistance meter. Replicate tests were managed 3-5 times, and average values were considered. Following the procedure of our recent work[19], water uptake (ASTM-D-570-98) testing was performed in distilled water, 10% aq. NaCl, 10% aq. NaOH, 10% aq. HCl and 10% aq. H2SO4 solutions at 30±2°C by the change in mass method at the interval of 24h till equilibrium attained.
Mechanical and Electrical Properties
The tensile strength, flexural strength, flexural modulus, Izod impact strength, Barcol hardness, electric strength, and volume resistivity of EMABCS (neat), and EMABCS-J/TJ are described in our recently published work[16,17] and are compared with EMABCS-J/TJ-B/GN/CS/PA/RH/WH in Figures 1-7. The tensile strength of the EMABCS is almost double that of EMABCS-J and is comparable with EMABCS-TJ. EMABCS-TJ-B/GN/CS/PA/RH/WH showed increased tensile strength than EMABCS-J-B/GN/CS/PA/RH/WH (Figure 1). EMABCS-J-GN/CS/PA/RH/WH showed 7.7-76.9% improved tensile strength except for EMABCS-J-B, which showed a 7.7% reduced tensile strength. Similarly, EMABCS-TJ-PA/RH/WH ensured 13.8-17.2% improved tensile strength, and EMABCS-TJ-B/GN/CS, respectively showed 53.4, 3.4, and 32.8% reduction in tensile strength. Compared to EMABCS-J/TJ, the improvement or deterioration of tensile strength of EMABCS-J/TJ-B/GN/CS/PA/RH/WH is due to different characteristic chemical compositions and physical properties of the natural fibers[7] and poor wettability of NFs with EMABCS. Sandwich composites showed almost comparable tensile strength with those of sandwich composites based on other natural fibers[19].
Figure 1. Comparative tensile strength of EMABCS-J/TJ and EMABCS-J/TJ-B/GN/CS/PA/RH/WH composites.
A slightly smaller flexural strength (Figure 2) of EMABCS than its tensile strength (Figure 1) revealed its somewhat rigid nature. Reinforcement of J/TJ and or NFs in EMABCS resulted in a considerably improved flexural strength of the composites. Compared to EMABCS-J, EMABCS-J-B/CS/PA/RH/WH showed 28.4-46.3% improved flexural strength except for EMABCS-J-GN, which showed 19.4% reduced flexural strength. EMABCS-TJ-B/PA displayed a little improvement in flexural strength (2.3-4.6%) and the rest of the alkali-treated sandwich composites (EMABCS-TJ-GN/CS/RH/WH) resulted in decreased flexural strength (13-17.5%). This is probably due to an overall decrease in the stiffness of the composites. The nature of the natural fibers, their microfibril angles, fiber orientation, fiber strength and stiffness, chemical compositions, and surface modification affect the overall stiffness of the composites[1, 2, 10]. Fabrication technique and fiber loading also affect the mechanical properties of the composites. In sandwich composites, jute fibers are bioriented and natural fibers are randomly oriented. The stress transfer from fiber to the matrix is continuous for oriented fiber and it is discontinuous for randomly oriented fibers. Untreated jute and natural fibers have noncellulosic compounds and smooth surfaces, which lead to inferior mechanical interlocking and incompatibility between natural fibers and polar matrix material. Alkali treatment to jute and natural fibers remove noncellulosic materials and thereby improved mechanical properties can be achieved due to improved compatibility, hydrophobicity, interfacial bonding, and surface roughness of natural fibers.
Figure 2. Comparative flexural strength of EMABCS-J/TJ and EMABCS-J/TJ-B/GN/CS/PA/RH/WH composites.
EMABCS-J/TJ and EMABCS-J/TJ-B/CS/PA/RH/WH revealed good to excellent flexural modulus (Figure 3) except EMABCS-TJ-GN because of the good stiffness of the composites. EMABCS-TJ-CS showed comparable flexural modulus. EMABCS-TJ-PA displayed 5.4% improved flexural modulus due to the overall improved stiffness of the sandwich composite. Compared to EMABCS-J/TJ, EMABCS-J-B/GN/CS/PA/RH/WH and EMABCS-TJ-B/CS/PA/RH/WH sandwich composites showed respectively 31.8-39.4% and 7.4-15% reduction of flexural modulus, while EMABCS-TJ-GN revealed 79.8% reduction. The observed fact is due to the characteristic chemical compositions and physical properties of the natural fibers, and interfacial strength. Alkali-treated sandwich composites showed better stiffness over untreated sandwich composites due to improved wettability and interface adhesion. Mainly random orientation and characteristic chemical and physical properties of the natural fibers in the sandwich composites are responsible for the reduction of the flexural modulus.
Figure 3. Comparative flexural modulus of EMABCS-J/TJ and EMABCS-J/TJ-B/GN/CS/PA/RH/WH composites.
It is noticed from Figure 4 that the impact strength of both types of sandwich composites is decreased compared to neat, and EMABCS-J/TJ. Compared to neat, EMABCS-J (17.4%) and EMABCS-TJ (43.5%) revealed better impact strength due to untreated and treated jute reinforcement. EMABCS-J-B (70.4%), EMABCS-J-CS (66.7%), EMABCS-J-GN/PA (33.9%), and EMABCS-J-RH/WH (51.9%) showed a considerable lowering of impact strength. Similarly, EMABCS-TJ-B (48.5%), EMABCS-TJ-GN (21.2%), EMABCS-TJ-CS (57.6%), EMABCS-TJ-PA (15.2%), EMABCS-TJ-RH (42.4%), and EMABCS-TJ-WH (45.5%), also resulted in lowering of the impact strength. The lowering of impact strength of both types of sandwich composites is due to random orientation, poor adhesion, and characteristic chemical and physical properties of the natural fibers. We had also observed similar behavior with other natural fibers-based composites[19].
Figure 4. Comparative impact strength of EMABCS-J/TJ and EMABCS-J/TJ-B/GN/CS/PA/RH/WH composites.
From Figure 5, it is clear that EMABCS-J/TJ-B/GN/CS/PA/RH/WH sandwich composites showed decreased Barcol hardness compared to EMABCS, and EMABCS-J/TJ. Alkali treated jute-B/GN/CS/PA/RH/WH sandwich composites showed better Barcol hardness over untreated jute-B/GN/CS/PA/RH/WH sandwich composites. Compared to EMABCS-J, EMABCS-J-B/GN/CS/PA/RH/WH resulted in a 22.2-36.1% reduction in Barcol hardness. Similarly, EMABCS-TJ-B/GN/CS/PA/RH/WH sandwich composites showed a 5-32.5% reduction in Barcol hardness compared to their counterpart EMABCS-TJ. The observed facts in both types of sandwich composites are due to random orientation and characteristic chemical and physical properties of the natural fibers[7]. In the present case, the suggested Barcol hardness (45-65)[22] was not achieved for scratch and wear resistance application.
Figure 5. Comparative Barcol hardness of EMABCS-J/TJ and EMABCS-J/TJ-B/GN/CS/PA/RH/WH composites.
Performance of the natural fiber-reinforced composites are influenced by cellulose content, microfibrillar angles, defects, structure, physical properties, chemical composition, cell dimensions, mechanical properties, and the interaction of a fiber with the polymer matrix. The selection of plant fibers, matrix materials, dispersion of the fibers, surface adhesion, surface treatments, fabrication techniques, etc is very important for improved mechanical properties of the natural fiber-reinforced composites[23]. Achieved mechanical properties of both types of sandwich composites signified their importance as low load-bearing materials for housing applications.
From Figure 6, it is noticed that EMABCS and EMABCS-TJ have comparable electric strength, and almost double that of EMABCS-J. Compared to EMABCS-J, EMABCS-J-GN/PA/RH/ WH showed 31.6-52.6% improved electric strength, while it has deteriorated in the case of EMABCS-J-B (22.8%) and EMABCS-J-CS (64.9%). Similarly, EMABCS-TJ-B/PA/RH/WH showed 5-39% deterioration in electric strength over EMABCS-TJ and it is much more for EMABCS-TJ-GN (54%) and EMABCS-TJ-CS (77%) due to fiber treatment and inherent characteristic properties of the fibers.
Figure 6. Comparative electric strength of EMABCS-J/TJ and EMABCS-J/TJ-B/GN/CS/PA/RH/WH composites.
EMABCS showed excellent volume resistivity, while it is good for EMABCS-J/TJ and EMABCS-J/TJ/-B/GN/CS/PA/RH/WH (Figure 7). EMABCS-TJ showed improved volume resistivity over EMABCS-J. The decrease in volume resistivity of EMABCS-J/TJ and EMABCS-J/TJ-B/GN/CS/PA/RH/WH is due to polar reinforcements and their different chemical compositions. EMABCS-J-GN/PA/RH displayed 192.3-384.3 times improved volume resistivity over their counterpart EMABCS-J and it is 57.7 times for EMABCS-J-WH. EMABCS-J-B (0.5 times) and EMABCS-J-CS (0.96 times) showed almost comparable volume resistivity with EMABCS-J. Alkali treated jute-natural fiber sandwich composites showed substantially lower volume resistivity than untreated–natural fiber sandwich composites except for EMABCS-TJ-PA, which has shown 2600 times improvement. EMABCS-TJ-B/GN/ RH/WH showed 9-50 times improvement in volume resistivity compared to EMABCS-TJ and it is comparable for EMABCS-TJ-CS. Polymeric materials are regarded as insulating materials having a volume resistivity of the order of 1010-1015 ohm-cm. Extremely low conductivities of such materials are due to the presence of free charge carriers[24, 25]. The fairly good electrical properties of the studied composites are mainly due to the polar nature of reinforcements as well as epoxy methacrylate resin indicated their usefulness as insulating materials.
Figure 7. Comparative volume resistivity of EMABCS-J/TJ and EMABCS-J/TJ-B/GN/CS/PA/RH/WH composites.
During service, polymeric materials come across various environmental conditions and mechanical forces and therefore it is highly essential to assess their water uptake tendency in different environmental conditions affecting ultimate properties. In the present study, we had selected different environments namely water, 10% aq. NaCl, 10% aq. NaOH, 10% aq. HCl and 10% aq. H2SO4 for water uptake kinetics at room temperature (30±2°C). The amount of moisture uptake or absorbed by the samples was determined according to the following Eqn. 1:
M=Wm−WdWd×100 (1)
Where M = % water uptake at time t, Wm = weight of the moist sample, and Wd = weight of the dry sample. Typical water uptake curves for EMABCS-J/TJ-B and EMABCS-J/TJ-PA are presented in Figures 8 and 9, respectively.
Figure 8. Comparative water uptake curves of EMABCS-J/TJ and EMABCS-J/TJ-B composites at 30°C.
Figure 9. Comparative water uptake curves of EMABCS-J/TJ and EMABCS-J/TJ-PA composites at 30°C.
The percentage of water uptake in the composites were found to increase with time, reached maximum, and then remained practically unchanged with time i.e., equilibrium point or saturation point. The equilibrium water content in different environmental conditions and equilibrium time for all the composites are given in Table 2. The observed water uptake trend in the composites is the same in different environments. Obtained water uptake trend is H2SO4 >HCl >NaOH >H2O >NaCl except EMABCS-TJ-CS (H2SO4>HCl>H2O>NaOH). Water uptake tendency in treated jute sandwich composites are considerably lower than jute sandwich composites. The observed fact is due to surface modification. In different environments (Table 2), untreated jute (20.5-17.8%) and jute-natural fiber (20.9-18.6%) sandwich composites showed higher equilibrium water uptake than treated jute (16.9-14.4%) and treated jute-natural fiber (18-15.1%) sandwich composites. The high water uptake tendency of the composites is due to the hydrophilic nature of the jute and natural fibers. The variable chemical compositions of the natural fibers affected water uptake in the composites. All the composites showed a relatively longer saturation time (384-432h) and excellent hydrolytic stability in harsh environmental conditions.
Hemicellulose present in the natural fibers results in thermal and biodegradation and higher water uptake in the composites. In contrast, lignin-rich fiber composites show better resistance to weathering[25] due to a lower affinity towards moisture and act as a protective barrier for cellulose microfibrils for water uptake. Lignin is thermally stable but it is greatly responsible for UV degradation[23]. Water uptake in polymeric materials depend upon the type of the materials, chemical compositions, fabrication conditions, electrolytic environments, temperature, etc.[17-19, 26]. The nature of electrolytes with the same concentration and different chemical compositions of natural fibers affected saturation time and equilibrium water content. Water uptake leads to swelling, plasticization, lowering in the elastic modulus, and glass transition temperature of the polymer[26-33].
The coefficient of water diffusion or water diffusivity in the composites in different environments was calculated according to Eqns. 2 and 3:
M=4Mmh√tπ√Dx (2)
Dx=π(h4Mm)2 (slope)2 (3)
Where Dx = diffusivity, t = time (second), h = sample thickness (m) and Mm = equilibrium water uptake. For the calculation of the values of Dx, the initial slopes of M against √t curves (Eqn. 3) were determined and are reported in Table 3. From Table 3, it is clear that the environmental conditions, nature of the electrolytes, matrix, and the constituents of the composites played an important role in the diffusivity in the composites. Different strong electrolytes break water structure differently and form new water structures and consequently, affect water diffusion in the composites. Observed different diffusivity in different environments are due to different solvated ionic sizes [17-19]. Water uptake proceeds through the matrix by the Fickian diffusion of solvated water molecules driven by a concentration gradient. The diffusion of water in the composites depends on the temperature and concentration of water molecules. The diffusion of solvated water molecules in the composites was continued with time until equilibrium was established and then free water was occupied in the voids if any. Due to personal limitations, the void content in the composites was not carried out. Free water present in the voids may lead to delamination, degradation, or void formation [28]. Cracking and blistering lead to high water uptake and the leaching of small molecules results in a decrease in the mass[26]. No leaching of small molecules from the composites was observed. Excellent hydrolytic stability and longer equilibrium time of the sandwich composites indicated their applications in humid and harsh environmental conditions.
Epoxy methacrylate of bisphenol-C-jute/treated jute–natural fibers reinforced sandwich composites were prepared and characterized for their mechanical and electrical properties; and water uptake in acidic, alkaline and saline environments at 30°C. The sandwich composites revealed fairly good to good mechanical and electrical properties. Both types of sandwich composites showed excellent hydrolytic stability against water, acids, alkali, and salt solutions, a high water uptake tendency, and a longer equilibrium time. Treated jute-based sandwich composites displayed a considerable water uptake tendency due to surface modification. The nature of the reinforcement, their orientation, surface modification, physical and chemical properties of the fibers affected the studied properties.
Acknowledgement: The authors are thankful to FIST-DST and SAP-UGC for their generous financial support for instrumentation support to the Department of Chemistry and Director TIPCO industries Ltd., Valsad-Gujarat, India, to test the composites.
References
1. K.G. Satyanarayana, G.G.C. Arizaga, and F. Wypych. Biodegradable composites based on lignocellulosic fibers-An overview. Prog. Polym. Sci. 34(2009):982-1021. [Google Scholar]
2. Rashid Latif, Saif Wakeel, Noor Zaman Khan, Arshad Noor Siddiquee, Shyam Lal Verma, and Zahid Akhtar Khan. Surface treatments of plant fibers and their effects on mechanical properties of fiber-reinforced composites: A review. J. Reinf. Plast. Compos. 38 (2019): 15-30. [Google Scholar]
3. M. R. Sanjay, P. Madhu, M. Jawaid, et al. Characterization and properties of natural fiber polymer composites: a comprehensive review. J. Clean Prod. 172 (2018): 566-581. [Google Scholar]
4. S. R. D. Petroudy. Physical and mechanical properties of natural fibers. In: Fan M and Fu F (eds). Advanced High Strength Natural Fiber Composites in Construction. Wood Publishing, (2017): 59-83. [Google Scholar]
5. S. K. Ramamoorthy, M. Skirfvars, and A. Persson. A review of natural fibers used in biocomposites: plant, animal, and regenerated cellulose fibers. Polym. Rev. 55 (2015): 107-162. [Google Scholar]
6. H. M. C. De Azeredo. Nanocomposites for food packaging applications. Food Res. Int. 42 (2009): 1240-1253. [Google Scholar]
7. J. P. Patel, and P. H. Parsania. Biodegradable and biocompatible polymer composites, properties and applications characterization, testing and reinforcing materials of biodegradable composites, Woodhead Publishing, Elsevier, Duxford, United Kingdom, (2018): 55-79. [Google Scholar]
8. S. Park, J. O. Baker, M. E. Himmel, P. A. Parilla, and D. K. Johnson. Cellulose crystallinity index: measurement techniques and their impact on interpreting cellulase performance. Biotechnol Biofuels (2010). DOI: https://doi.org/10.1186/1754-6834-3-10 [Google Scholar] [CrossRef]
9. Y. Zhou, M. Fan, and L. Chen. Interface and bonding mechanisms of plant fiber composites: an overview. Compos Part B Eng. 101 (2016): 31-45. [Google Scholar]
10. S. Kalia, B. Kaith, and I. Kaur. Pretreatments of natural fibers and their application as reinforcing material in polymer composites-A review. Polym. Eng. Sci. 49 (2009): 1253-1272. [Google Scholar]
11. Z. N. Azwa, B. F. Yousif, A. C. Manalo, and W. Karunasena. A review on the degradability of polymeric composites based on natural fibers. Mater. Des. 47 (2013): 424-442. [Google Scholar]
12. A. Shalwan, and B. F. Yousif. Investigation on interfacial adhesion of date palm/epoxy using fragmentation technique. Mater. Des. 53 (2014): 928-937. [Google Scholar]
13. Jignesh V. Patel, Ritesh D. Bhatt, and Parsotam H. Parsania. Synthesis and characterization of methacrylate epoxy resin of 1,1-bis(4-hydroxy phenyl) cyclohexane and its composites. J. Polym. Mater. 31 (2014): 409-420. [Google Scholar]
14. J. V. Patel, J. P. Patel, R. D. Bhatt, and P. H. Parsania. Mechanical and electrical properties of jute-biomass-styrenated methacrylate epoxy resin sandwich composites. J. Sci. Indus. Res. 74 (2015): 577-581. [Google Scholar]
15. J. V. Patel, J. P. Patel, R. D. Bhatt, and P. H. Parsania. Filled and unfilled glass/jute-epoxy methacrylate of 1,1'-bis(4-hydroxy phenyl) cyclohexane composites: Mechanical and electrical properties, Indian J. Chem. Technol. 23 (2016): 153-157. [Google Scholar]
16. P. H. Parsania, Ritesh D. Bhatt, and Jignesh P. Patel. Synthesis and evaluation of some physical properties of epoxy methacrylate of bisphenol-C: A comparative study with commercial resin Aeropol-7105. Polym. Bull. 78 (2021): 7355-7367. [Google Scholar]
17. Ritesh D. Bhatt, Jignesh P. Patel, and Parsotam H. Parsania. Potential comparison of montmorillonite filled and unfilled epoxy methacrylate of bisphenol-C-glass/jute/treated jute and hybrid composites. World Scientific News. 158 (2021): 227-246. [Google Scholar]
18. Ritesh D. Bhatt, Jignesh P. Patel, and P. H. Parsania. Glass/Biofibers/Epoxy methacrylate of bisphenol-C sandwich composites: Comparative mechanical and electrical properties and chemical resistance. J. Polym. Mater. 38 (2021): 81-97. [Google Scholar]
19. Ritesh D. Bhatt, Jignesh P. Patel, and Parsotam H. Parsania. Fabrication and comparative properties of sustainable epoxy methacrylate of bisphenol-C-jute/treated jute-natural fibers sandwich composites: Part-I. J. Plym. Mater. 39(2022): 205-221. [Google Scholar]
20. A. I. Vogel, A. R. Tatchell, B. S. Furnis, A. J. Hannaford, and P. W. G. Smith. Vogel's Textbook of Practical Organic Chemistry, 5th ed.; Addison Wesley Longman: Harlow, Essex, UK, 1998, 395. [Google Scholar]
21. J. P. Patel, and P. H. Parsania. Fabrication and comparative mechanical, electrical, and water absorption characteristic properties of multifunctional epoxy resin of bisphenol-C and commercial epoxy-treated and untreated jute fiber-reinforced composites. Polym. Bull. 74 (2017): 485-504. [Google Scholar]
22. International Cast Polymer Alliance, Solid surface properties and applications. Arlington, ICPA 2003: 8. [Google Scholar]
23. D. N. Saheb, and J. P. Jog. Natural fiber polymer composites: A review. Adv. Polym. Technol. 18 (1999): 351–363. [Google Scholar]
24. T. H. Wu, A. Foyet, A. Kodentsov L. G. J. van der Ven, R. A. T. M. van Benthem, G. de With. Curing and percolation for carbon black-epoxy-amine nanocomposites. Compos. Sci. Technol. 181 (2019). DOI: https://doi.org/10.1016/j.compscitech.2019.05.029. [Google Scholar] [CrossRef]
25. G. C. Psarras. Conductivity and dielectric characterization of polymer nanocomposites. In Physical properties and applications of polymer nanocomposites. Eds. Tjong S. C., Mai Y-W. Woodhead, Cambridge, (2010): 31-69. [Google Scholar]
26. A. N. Fraga, V. A. Alvarez, O. De La Osa, and A. Vazquez, Relationship between dynamical mechanical properties and water absorption of unsaturated polyester and vinyl ester glass fiber composites, J. Compos. Mater. 37 (2003): 1553-1574. [Google Scholar]
27. C. S. Tyberg, K. M. Bergeron, M. Sankarapandian, P. Singh, A. C. Loss, D. A. Dillard, J. E. McGrath, and J. S. Riffle. Structure-property relationships of void-free phenolic-epoxy matrix materials. Polymer. 41(2000): 5053-5062. [Google Scholar]
28. S. L. Gibson, V. Baranauskas, J. S. Riffle, and U. Sorathia. Cresol-novolac epoxy networks: Properties and processability. Polymer. 43 (2002): 7389-7398. [Google Scholar]
29. V. Alvarez, A. Vazquez, O. De La Osa (2007). Cyclic water absorption behavior of glass-vinyl ester and glass-epoxy composites. J. Compos. Mater. 41 (2007): 1275-1289. [Google Scholar]
30. S. Marais, M. Metayer, T. Q. Nguyen, M. Labbe, and J. M. Saiter. Diffusion and permeation of water through unsaturated polyester resins-influence of resin curing. Eur. Polym. J. 36 (2000): 453-462. [Google Scholar]
31. A. M. Visco, N. Campo, and P. Cianciafara. Comparison of seawater absorption properties of thermoset resins-based composites. Composites Part A. Appl. Sci. Manuf. 42 (2011):123-130. [Google Scholar]
32. F. A. Ramirez, L. A. Carlsson, and B. A. Acha (2008). Evaluation of water degradation of vinyl ester and epoxy matrix composites by single fiber and composite tests. J. Mater. Sci. 43 (20085230-5242. [Google Scholar]
33. L R. Bao, and A. F. Yee. Effect of temperature on moisture absorption in a bismaleimide resin and its carbon fiber composites. Polymer. 43 (2002):3987-3997. [Google Scholar]
Cite This Article
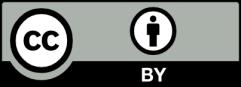
This work is licensed under a Creative Commons Attribution 4.0 International License , which permits unrestricted use, distribution, and reproduction in any medium, provided the original work is properly cited.