Open Access
ARTICLE
Fabrication and Comparative Properties of Sustainable Epoxy Methacrylate of Bisphenol-C-Jute/Treated JuteNatural Fibers Sandwich Composites: Part-1
Department of Chemistry, Saurashtra University, Rajkot-360 005, Gujarat, India.
* Corresponding Authors: e-mail: and
Journal of Polymer Materials 2022, 39(3-4), 205-221. https://doi.org/10.32381/JPM.2022.39.3-4.3
Abstract
Epoxy methacrylate of bisphenol-C-jute/treated jute and their sandwich composites of white coir, brown coir, wild almond, bamboo, betel nut, and palmyra were prepared by a compression molding technique under 5MPa pressure and at room temperature for three h. The neat sample showed almost double tensile strength than its jute composite, while it is comparable for treated jute. The composites revealed substantially improved flexural strength compared to neat. The neat, jute/treated jute and their sandwich composites indicated good impact strength, pretty good Barcol hardness, and fairly good electric strength. The neat sample showed excellent volume resistivity, while jute/treated jute and their sandwich composites revealed reasonably good volume resistivity. The composites showed high water ingress tendency, excellent hydrolytic stability, and different diffusivity in different environments at 30oC. Water ingress trend was observed the same for all the composites in different environments, and it is H2 SO4 > HCl >NaOH >H2 O>NaCl. The sandwich composites may find their applications as low-cost housing and insulating materials and also for marine vessels.Keywords
Humankind uses natural fibers to make household materials such as ropes, clothes, bedsheets, packaging materials, etc. The demand for natural fibers is increasing globally day by day due to their easy and bountiful availability, biodegradability, economically cheaper than synthetic fibers[1-3]. Material scientists are looking for sustainable and nonbiodegradable fiber-reinforced composites that are accustomed to using building construction, agriculture, packaging, automobile, engineering, and aerospace fields to avoid environmental problems. Attractive features of natural fiber-reinforced composites are their low cost, lightweight, nonhazardous, moderate mechanical strength, and easy handling. Natural fibers can be extracted from various parts of the plants such as stems, fruits, leaves, seeds, husks, kernels, etc. [4-8] Commonly used natural fibers are jute, bamboo, coconut, ramie, kenaf, sugar cane, sisal, pineapple, abaca, nettles, rice, flax, grass, etc. The chemical compositions and water absorption tendencies of different fibers are different. [4-6] The main drawbacks of natural fibers are their high flammability [9-11] and their highly hygroscopic nature, which restrict their applications. The primary chemical constituent of natural fibers is cellulose containing a large number of hydrophilic hydroxyl groups, showing poor wettability with hydrophobic resins and poor interfacial bonding. Such drawbacks can be improved by chemical or physical modification of the fibers. [4]
The most commonly used matrices for synthetic and natural fiber-reinforced composites are epoxy, phenol-formaldehyde, and polyester resins because of their very good to excellent physicochemical properties, relatively cheaper, and readily available. The sustainability of the composites relies on many factors, namely nature and constituent fibers and matrices, pollution, temperature, environmental humidity, light, and magnetic radiations, etc.[3, 12-14] Fiber-reinforced composites are used in the automotive, shipping, gas, and oil tube industries.[1, 15, 16]
Several researchers have carried out their researches on low-cost and sustainable natural fiber-reinforced composites for specific industrial applications. Most of them have used readily available commercial epoxy resin or unsaturated polyester resin based on bisphenol-A as a matrix material and achieved good to excellent physicochemical properties.
Previously we have synthesized semisolid epoxy methacrylate of bisphenol-C and prepared its jute, glass as well as biomass-filled sandwich composites[17,18] and achieved good physical properties. The semisolid resin was found difficult to handle so we have synthesized liquid epoxy methacrylate of bisphenol-C[19] and achieved comparable physical properties with commercial resin Aeropol 7105. A 40% styrene was used as a reactive diluent. Neat and 5% MMT-filled samples were prepared at room temperature by using 1% MEKP as an initiator, 1.5% dimethylaniline as a promoter, and 1% cobalt octoate as an accelerator. Mechanical and electrical properties as well as water absorption behavior of MMT filled and unfilled samples were investigated and compared. MMT filled and unfilled samples showed better studied mechanical and electrical properties and very low water ingress.
In our recent work, we have prepared 5% montmorillonite filled and unfilled epoxy methacrylate of bisphenol-C-jute, treated jute, glass, and their hybrid composites; and investigated their physicochemical properties.[20] Filled and unfilled composites revealed good to excellent mechanical and electrical properties, and excellent chemical resistance against water acids, alkali, and salt solutions. Hybrid composites showed intermediate properties of their parent composites. MMT filled treated jute (46), and unfilled glass (48), and MMT filled glass (48) composites revealed Barcol hardness between the suggested range of 45-65 for scratch and wear resistance proof materials. We had observed the effect of the nature of the reinforcements, matrix, filler, fiber treatment, and environmental conditions on studied mechanoelectrical properties and chemical resistance.
Using twelve different chopped (1-2 mm) bio-fibers, glass-bio-fibers-epoxy methacrylate of bisphenol-C sandwich composites were fabricated[21]. The sandwich composites revealed good mechanical and good to excellent electrical properties and excellent chemical resistance against water, acid, and alkali solutions. Compared to neat and glass composite the sandwich composites displayed the lowering of some of the mechanical and electrical properties because of the random orientation of the bio-fibers and poor adhesion.
We intended to protect the environment partially and support producers financially. So we have fabricated sustainable and low-cost sandwich composites of liquid epoxy methacrylate of bisphenol-C[19] and evaluated their mechanoelectrical properties and water ingress in different environmental conditions. Such sandwich composites may replace plywood for specific applications, especially during natural calamities like floods, earthquakes, cyclones, etc. For this purpose, we had collected several natural fibers from different natural resources. Studied properties of the sandwich composites are collated with neat and glass composite.
Laboratory grade solvents and chemicals used in this work were purified before their use [22] or used as received. The liquid epoxy methacrylate of bisphenol-C (EMABC) [19] was synthesized according to the following Scheme-I:
Scheme-I:: The synthesis of epoxy methacrylate of bisphenol-C
A 40% styrene solution of EMABC was prepared at room temperature, and 0.2% hydroquinone was added as an inhibitor. This solution was designated as EMABCS, which had 1.12 g cm-3 density, 300 cP viscosity, 20 min gel time, and 135oC peak exotherm temperature[19]. Methylethylketone peroxide (MEKP), 6% cobalt octoate, and mylar film were supplied by EPP Composites, Rajkot, as free samples and were used as received. Jute fabric (J) (350 GSM) was purchased from a local market (Rajkot). Jute was treated with 4% alkali solution at room temperature for 12 h [23] and designated as TJ.
Various bio-fibers (BFs) such as white coir (WC) (Cocus Nucifera), brown coir (BC) (Cocus Nucifera), were obtained from a local market (Rajkot). Wild almond fruits were procured from Junagadh and fibers (WA) (Sterculia foetida) were extracted manually[7]. Bamboo (BM) fibers (Phyllostachys aurea) were acquired from Kolkata. Betel nut (BN) (Areca catechu) and palmyra (PM) (Borassus flabellifer) fibers were bought from Calicut. Collected natural fibers were cleaned, washed several times with distilled water, and dried in an oven at 50°C for 48 h. Dry and cleaned bio-fibers were chopped into 1-2 mm size and stored in airtight containers. Chemical compositions and physical properties of some of the natural fibers are found variable[4-6] (31-83% cellulose, 18-33% hemicellulose except coir, 14-30% lignin, and 8.5-17% water absorption tendency).
Preparation of Controls and the Composites
EMABCS control was prepared according to our recently published work[19]. The required quantities (Table 1) of EMABCS, 1% initiator (MEKP), 1% cobalt octoate (accelerator), and 1.5% dimethylaniline (promoter) of resin were transferred into a 500 mL beaker at room temperature and mixed well with a glass rod to prevent air bubble formation. Jute fabric of 20 cm x 20 cm sizes (5 plies) was impregnated by a smooth brush and kept at room temperature for 15-20 min. The chopped natural fibers were divided into four equal portions (about one-third of jute fabric) and spread uniformly on five impregnated sheets, stacked one over the other between two mylar films, and pressed between two mold platen under 5 MPa pressure at room temperature for three h and post cured in an oven at 150°C for 30 min; cooled to room temperature, peeled off mylar films, and machined the edges. For tensile and flexural testing, the samples were prepared as per standard test methods. For tensile strength measurements, the sample widths and thicknesses were 9.04-11.42 mm and 4.25-6.17 mm, respectively, and they were 12.03-12.49 mm and 4.25-6.27 mm, respectively for flexural strength measurements. For the water ingress study, 2cm x 2cm samples were cut from the respective sheets and sealed using corresponding resin solutions and cured at room temperature, and post-cured in an oven.
Tensile strength (ASTM-D-638-01) and flexural strength (ASTM-D-790-03) measurements were carried out at a speed of 10 mm min-1 on a W & T Avery Ltd. Type 1010 Model No E-46234 (Birmingham, England). Izod impact strength (ASTM-D-256-06) tests were carried out on an Izod Impact Tester Model No.E-46204 Type A-1300 (Birmingham, England). Electric strength (IEC-60243-Pt-1-1998) quantifications were carried out in the air using 25/75 mm brass electrodes on a high voltage tester (Automatic Electric-Mumbai). Volume resistivity (ASTM-D-257-2007) tests were carried out in the air at 25°C after 60 s charging at 500 V DC applied voltage on a Hewlett Packard high resistance meter. Replicate tests were managed 3-5 times, and average values were considered. Water ingress (ASTM-D-570-98) testing was performed at 30±2°C by the change in mass method. The samples were weighed and dipped in water, 10% aq. NaCl, 10% aq. NaOH, 10% aq. HCl and 10% aq. H2SO4 solutions at 30±2°C. The samples were withdrawn at the interval of 24 h; the sample's surfaces were cleaned with tissue papers, reweighed, and immediately dipped in the respective solutions. The experiments were continued until the saturation/equilibrium was established.
Comparative mechanical properties namely tensile strength, flexural strength, flexural modulus, Izod impact strength, and Barcol hardness of EMABCS (neat), EMABCS-J/TJ, and EMABCS-J/TJ-BF are shown respectively in Figures1-5. The tensile strength of the neat sample is almost double that of EMABCS-J and is comparable with EMABCS-TJ. The enhanced tensile strength of the alkali-treated composites is due to surface modification of jute fibers and improved interface adhesion. EMABCS-TJ-BF resulted in enhanced tensile strength than EMABCS-J-BF due to the above-mentioned reasons. EMABCS-J-WC/BC/BN/WA/BM showed good to excellent better tensile strength (23.1-92.3%). EMABCS-J-PM showed comparable tensile strength. Similarly, EMABCS-TJ-WC/BC/BN/WA ensured 12.1-34.5% good tensile strength. Thus, both types of the sandwich composites showed improved tensile strength relative to EMABCS-J and EMABCS-TJ except EMABCS-J-PM, EMABCS-TJ-PM, EMABCS-M, and EMABCS-TJ-BM. Thus, different constitutional compositions and physical properties of the reinforcements[4-6], surface modification of the jute fibers, the nature of the matrix, and interface adhesion affected the tensile strength of the composites.
Figure 1. Comparative tensile strength of EMABCS-J/TJ and EMABCS-J/TJ-BF.
Figure 2. Comparative flexural strength of EMABCS-J/TJ and EMABCS-J/TJ-BF.
Figure 3. Comparative flexural modulus of EMABCS-J/TJ and EMABCS-J/TJ-BF.
Figure 4. Comparative impact strength of EMABCS-J/TJ and EMABCS-J/TJ-BF.
Figure 5. Comparative Barcol hardness of EMABCS-J/TJ and EMABCS-J/TJ-BF.
From Figures 1 and 2, it is clear that the flexural strength of the neat sample is somewhat smaller than the tensile strength indicating the rigid nature of the neat sample. The flexural strength of the treated and untreated jute composites is enhanced substantially over EMABCS because of the stiff nature of the jute fibers. EMABCS-TJ showed almost doubled flexural strength than EMABCS-J and EMABCS (2.6 times). The enhancement of flexural property is mainly due to surface modification and improved interface bonding. Interface adhesion can be better judged by SEM analysis but due to personal limitations, such analysis was not done. We had judged the enhancement or deterioration of the properties based on observed results. The stated sandwich composites revealed a significantly improved flexural strength in light of the neat sample. EMABCS-J-WC/BN/PM/WA/BM displayed 15-40% more flexural strength except for EMABCS-J-BC due to the inherent characteristic properties of the bio-fibers. EMABCS-TJ-WC demonstrated slightly better flexural strength (8%) than EMABCS-TJ, and EMABCS-TJ/BC/BN/PM/WA/BM indicated slightly lower flexural strength (2-6%). The lowering of the tensile and flexural properties of EMABCS-TJ-BF sandwich composites is probably due to the increased polarity of treated jute fibers, which increased like interactions of hydroxyl groups of jute and bio-fibers with matrix and thereby lowering interface adhesion. The mechanical properties of the bio-fiber reinforced composites are governed by the selection of the bio-fibers, and the matrix, the chemical compositions, microfibril angles, fiber surface treatment, fabrication technique, fiber orientation, fiber strength, and stiffness, fiber loading, etc.[24-26]. In the present work, we had used bioriented jute fabric and randomly oriented bio-fibers in making composites. Untreated bio-fibers have noncellulosic compounds and smooth surfaces, which lead to inferior mechanical interlocking and incompatibility between bio-fibers and polar matrix material. Fiber modification can improve mechanical properties because of improved compatibility, hydrophobicity, interfacial bonding, and surface roughness of bio-fibers.
Figure 3 revealed excellent flexural modulus of EMABCS-J/TJ, and EMABCS-J/TJ-BF due to improved stiffness of the composites. The observed fact is due to reinforcement of the bioriented jute fibers, randomly oriented bio-fibers, and fiber treatment. The flexural moduli of EMABCS-J and EMABCS-J-BF are much smaller than EMABCS-J and EMABCS-TJ-BF. EMABCS-TJ has indicated 1.4 times more stiffness than EMABCS-J. EMABCS-J/TJ is 1.2-1.3 and 1.1-1.7 times more rigid than EMABCS-J/TJ-BF. Somewhat decrease in stiffness of the sandwich composites is mainly due to the random orientation of bio-fibers and their characteristic properties. In sandwich composites, stress transfer is discontinuous, which causes a lowering in the mechanical properties of the composites. In bioriented jute/treated jute fibers, stress transfer is continuous, and as a result, mechanical strengths are improved. The overall result of the use of oriented and randomly oriented fibers is the deterioration of the properties of the composite materials.
EMABCS, EMABCS-J/TJ, and EMABCS-J/TJ-BF showed good impact strength (Figure 4). EMABCS-J (17%) and EMABCS-TJ (43.5%) showed better impact strength than EMABCS due to improved interfacial bonding between jute and matrix material. Similarly, EMABCS-J (18-59 %) and EMABCS-TJ (21-42 %) displayed better impact strength than EMABCS-J/TJ-BF. The random orientation of the bio-fibers in the sandwich composites is mainly responsible for the decreasing impact strength.
It is noticed from Figure 5 that the mentioned composites showed enhanced Barcol hardness. EMABCS and EMABCS-J have equivalent Barcol hardness and it is slightly better for EMABCS-TJ due to alkali treatment. EMABCS-J-BF (19-36%) and EMABCS-TJ-BF (5-30%) showed reduced Barcol harness than EMABCS-J and EMABCS-TJ. The decrease in Barcol hardness of the sandwich composites is mainly due to the random orientation and variable chemical and physical properties of the bio-fibers. The fiber modification followed almost identical Barcol hardness of EMABCS-TJ-WC/BC/BN/BM and EMABCS. None of the samples can be used as scratch and wear resistance materials because of the lack of the required Barcol hardness of 45-65[27]. The acquired mechanical properties of the studied composites suggested their utility as low load-bearing housing applications.
The electric strength and volume resistivity of neat, untreated jute, treated jute, and sandwich composites are represented in Figures 6 and 7, respectively. The electric strength of the neat and EMABCS-TJ is comparable and almost double that of EMABCS-J (Figure 6). Both types of the sandwich composites revealed good electric strength except EMABCS-TJ-WC/BC/WA. EMABCS-J-WC/BC/BN/PM/WA (16-63%) showed better electric strength than EMABCS-J and EMABCS-J-BM displayed equivalent strength. The electric strength of EMABCS-TJ-BN/PM/BM is declined 7-29% over EMABCS-TJ. In the case of EMABCS-TJ/WC/BC/WA, the decline in the electric strength is substantially very high (47-76%). The declining electric strength of the treated jute sandwich composites might be due to the increased surface polarity of treated jute fibers.
Figure 6. Comparative electric strength of EMABCS-J/TJ and EMABCS-J/TJ-BF.
Figure 7. Comparative volume resistivity of EMABCS-J/TJ and EMABCS-J/TJ-BF.
The neat sample revealed excellent volume resistivity, while jute, treated jute, and sandwich composites showed fairly good to good volume resistivity (Figure 7) due to the polar nature of reinforcing fibers and their different chemical compositions. Surface modification of jute fibers leads to increased volume resistivity of EMABCS-TJ over EMABCS-J (two times). EMABCS-TJ-WC and EMABCS-J-BC exhibited comparable volume resistivity with EMABCS-J.
Polymeric materials are dielectric materials and show electrical conductivity (inverse of resistivity) of the order of 10-12 to 10-15 ohm-cm due to the presence of free charge carriers [28, 29]. The observed electrical properties of the composites are mainly due to the polar nature of reinforcements and matrix. The pretty good electric strength and volume resistivity of the composites indicated their usefulness as electrically insulating materials.
Under environmental conditions, polymeric fiber-reinforced composites undergo different interactions such as a chemical reaction, absorption, solvation, stress cracking, plasticization, etc. Consequently, their physicochemical properties change with time. Overall chemical resistance is determined based on some characteristic properties like bond strength, polarity, degree of branching, % crystallinity, temperature, etc. In a humid atmosphere, the moisture ingress in polymeric composites relies on the nature of the constituent components. It is a well-known fact that the natural fibers possess variable chemical compositions, physical properties, and water uptake (9-16%) tendencies.[4] Bio-fibers are hygroscopic because of the presence of many hydrophilic hydroxyl groups, which leads to poor wettability with hydrophobic matrix [4, 5, 23, 30, 31].
Water ingress in EMABCS-J/TJ and EMABCS-J/TJ-BF composites was studied by assuming unidimensional Fickian type diffusivity[31]. Following the kinetics of the mass change method at room temperature (30±2°C) and the interval of 24h was followed in different electrolytic solutions such as water, 10% aq. NaCl, 10% aq. NaOH, 10% aq. HCl and 10% aq. H2SO4. The percent water ingress in the composites was calculated according to Eqn.1:
Where M = % water ingress, Wm = weight of the moist sample, and Wd = weight of the dry piece.
Typical % Weight gain against Time curves for EMABCS-J/TJ-PM and EMABCS-J/TJ-WA are shown in Figures 8 and 9, respectively. Experimentally it was observed that the % weight gain was found to increase over time and then remained practically constant, i.e., equilibrium or saturation point. The saturation time and saturation water content in different environments for all the composites are reported in Table 2. The observed water ingres s trend in the composites is the same in different environments. Obtained water ingress trend is H2SO4 >HCl >NaOH >H2O >NaCl. Water ingress tendency in treated jute composites is reasonably lower than jute composites. The observed fact is due to surface modification. In different media (Table 2), untreated jute (20.5-17.8%) and jute-biofiber (20.5-14.1%) composites showed higher saturation water content than treated jute (16.9-14.4%) and treated jute-biofiber (17.7-14.1%). The high water ingress tendency of the composites is due to the hydrophilic nature of the jute and bio-fibers. The variable chemical compositions of the bio-fibers affected water ingress in the composites. The stated composites showed a relatively longer saturation time (384-456h) and excellent hydrolytic stability in harsh environmental conditions.
Figure 8. Comparative water ingress curves of EMABCS-J/TJ-PM sandwich composites at 30°C in different conditions.
Figure 9. Comparative water ingress curves of EMABCS-J/TJ-WA sandwich composites.
Hemicellulose leads to higher water ingress in the composites. In contrast, lignin-rich fiber composites show better resistance to weathering [32] due to a lower affinity towards moisture and act as a protective barrier for cellulose microfibrils from water ingress. The nature of electrolytes with the same concentration and different chemical compositions of bio-fibers affected saturation time and equilibrium water absorption behavior.
The diffusivity in EMABCS-J/TJ and EMABCS-J/TJ-BF in a given environment was evaluated from the initial slopes of M against √t curves according to Eqns. 2 and 3:
Where Dx = diffusivity, t = time (second), h = sample thickness (m) and Mm = equilibrium water ingress. Evaluated diffusivities in the composites in different environments are presented in Table 3. The environments, type, and nature of the constituents of the composites and strong electrolytes affected the diffusivity in the composites. The different electrolytes affect water structure differently, and as a result, different diffusivity is observed in different environments due to different solvated ionic sizes [17-19, 23].
Water diffusion in the composites occurred through the capillary mechanism and resulted in swelling, and blistering. The diffusion in the composites was continued with time till saturation point and then free water was occupied in the voids if any. Due to personal limitations, the void content in the composites was not carried out. Free water may interact with constituent components of the composite and thereby may cause delamination, degradation, or void formation[33]. Absorbed moisture causes swelling and plasticization of resin, weakening of interface increases delamination rate and thereby deterioration of the mechanical properties of the composite.[13, 33-39] Cracking and blistering lead to high water absorption, while the leaching of small molecules results in a decrease in weight [40]. In the present case, no leaching from the composites was observed. Excellent hydrolytic stability and longer equilibrium time of the sandwich composites in different media indicated their usefulness in harsh and humid environments.
Epoxy methacrylate of bisphenol-C-jute/treated and their biofiber sandwich composites was prepared and determined their mechanical and electrical properties; and water ingress in different media at 30°C. The composites showed good mechanical and electrical properties, and excellent hydrolytic stability, and a high water ingress tendency in various media. Treated jute and its sandwich composites revealed improved studied properties. The nature of the matrix, reinforcements, electrolytes, fiber orientation, surface modification, chemical compositions of fibers, and their physical properties affected the investigated physical properties of the composites.
Acknowledgement: The authors are thankful to FIST-DST and SAP-UGC for their generous financial support for instrumentation support to the Department of Chemistry and Director TIPCO industries Ltd., Valsad-Gujarat, India, to test the composites.
References
1. M. P. M. Dicker, P. F. Duckworth, A. B. Baker, G. Francois, M. K. Hazzard, and P. M. Weaver. Green composites: A review of material attributes and complementary applications. Composites Part A: Appl. Sci. and Manuf. 56 (2014): 280-289. [Google Scholar]
2. O. Akampumuza, P. M. Wambua, A. Ahmed, W. Li, and X-H. Qin. Review of the applications of biocomposites in the automotive industry. Polym. Compos. 38(2017): 2553-2569. [Google Scholar]
3. S. C. Furtado, A. L. Araújo, A. Silva, C. Alves, and A. M. R. A. Ribeiro. Natural fibre-reinforced composite parts for automotive applications. Int. J. Automot. Compos. 1(2014): 18-38. [Google Scholar]
4. J. P. Patel, and P. H. Parsania. Biodegradable and biocompatible polymer composites, properties and applications characterization, testing and reinforcing materials of biodegradable composites, Woodhead Publishing, Elsevier, Duxford, United Kingdom, (2018): 55-79. [Google Scholar]
5. Andrzej K. Bledzki, and Abdullah A. Mamun, and Jürgen Volk. Physical, chemical, and surface properties of wheat husk, rye husk, and softwood and their polypropylene composites. Composites: Part A. 41 (2010480-488. [Google Scholar]
6. Sridach Waranyou. Pulping and paper properties of Palmyra palm fruit fibers. Songklanakarin J. Sci. Technol. 32 (2010): 201-205. [Google Scholar]
7. Pooja P. Adroja, S. B. Koradiya, and P. H. Parsania. Fabrication, the mechanical and electrical study of sandwich biocomposites of epoxy resin of 1,1'-bis(3-methyl-4-hydroxyphenyl) cyclohexane. Ind. J. Eng. Mater. Sci. 20 (2013): 568-572. [Google Scholar]
8. O. Faruk, A. K. Bledzki, H. P. Fink, and M. Sain. Biocomposites reinforced with natural fibers: 2000-2010. Prog. Polym. Sci. 37 (20121552-1596. [Google Scholar]
9. S. Fatima, and A. R. Mohanty. Acoustical and fire-retardant properties of jute composite materials. Appl. Acoust. 72 (2011): 108-114. [Google Scholar]
10. S. Chapple, and R. Anandjiwala. Flammability of natural fiber-reinforced composites and strategies for fire retardancy: A review. J. Thermoplastic Compos. Mater. 23 (2010): 871-893. [Google Scholar]
11. T. Umemura, Y. Arao, S. Nakamura, Y. Tomita, and T. Tanaka. Synergy effects of wood flour and fire retardants inflammability of wood-plastic composites. Energy Procedia. 56 (2014): 48-56. [Google Scholar]
12. A. N. Fraga, E. Frullloni, O. De La Osa, and J. M. Kenny, A. Va´Zquez. Relationship between water absorption and dielectric behavior of glass fiber reinforced unsaturated polyester resin. J. Compos. Mater. 41 (2007): 393-402. [Google Scholar]
13. A. Alhuthali, I. M. Low. Water absorption, mechanical, and thermal properties of halloysite nanotube-reinforced vinyl-ester nanocomposites. J. Mater. Sci. 48 (2013): 4260-4273. [Google Scholar]
14. J. Holbery, and D. Houston. Natural-fiber-reinforced polymer composites in automotive applications, overview low-cost composites in vehicle manufacture. J. Org. Mater. 58 (2006): 80-86. [Google Scholar]
15. G. Phiri, M. C. Khoathane, and E. R. Sadiku. Effect of fiber loading on mechanical and thermal properties of sisal and kenaf fiber-reinforced injection-molded composites. J. Reinf. Plas. Compos. 33 (2014): 283-293. [Google Scholar]
16. A. V. Ratna Prasad and Mohana Rao K. Mechanical properties of natural fiber reinforced polyester composites: Jowar, sisal, and bamboo. Mater. Design. 32 (211): 4658-4663. [Google Scholar]
17. J. V. Patel, R. D. Bhatt, and P. H. Parsania. Synthesis and characterization of methacrylate epoxy resin of 1,1 ‘-bis(4-hydroxyphenyl) cyclohexane and its composites. J. Polym. Mater. 31 (2014): 409-20. [Google Scholar]
18. J. V. Patel, J. P. Patel, R. D. Bhatt, and P. H. Parsania. Mechanical and electrical properties of jute-biomass-styrenated methacrylate epoxy resin sandwich composites. J. Sci. Indus. Res. 74 (2015): 577-581. [Google Scholar]
19. P. H. Parsania, R. D. Bhatt, and J. P. Patel. Synthesis and evaluation of some physical properties of epoxy methacrylate of bisphenol-C. A comparative study with commercial resin Aeropol-7105. Polym. Bull. 78 (2021): 7355-7367. [Google Scholar]
20. Ritesh D. Bhatt, Jignesh P. Patel, and Parsotam H. Parsania. Potential comparison of montmorillonite filled and unfilled epoxy methacrylate of bisphenol-C-glass/jute/treated jute and hybrid composites. World Scientific News. 158 (2021227-246. [Google Scholar]
21. Ritesh D. Bhatt, Jignesh P. Patel, and P. H. Parsania, Glass/Biofibers/Epoxy Methacrylate of Bisphenol-C sandwich composites: Comparative mechanical and electrical properties and chemical resistance. J. Polym. Mater. 38 (2021): 81-97. [Google Scholar]
22. A. I. Vogel, A. R. Tatchell, B. S. Furnis, A. J. Hannaford, and P. W. G. Smith (1998). Vogel's Textbook of Practical Organic Chemistry, 5th ed.; Addison Wesley Longman: Harlow, Essex, UK (1998): 395. [Google Scholar]
23. J. P. Patel, and P. H. Parsania. Fabrication and comparative mechanical, electrical, and water absorption characteristic properties of multifunctional epoxy resin of bisphenol-C and commercial epoxy-treated and untreated jute fiber-reinforced composites. Polym. Bull. 74 (2017): 485-504. [Google Scholar]
24. Latif Rashid, Wakeel Saif, Noor Zaman Khan, Arshad Noor Siddiquee, Shyam Lal Verma, and Zahid Akhtar Khan. Surface treatments of plant fibers and their effects on mechanical properties of fiber-reinforced composites: A review. J. Reinf. Plas. Compos. 38 (2019): 15-30. [Google Scholar]
25. K. G. Satyanarayana, G. G. C. Arizaga, and F. Wypych. Biodegradable composites based on lignocellulosic fibers-An overview. Prog. Polym. Sci. 34 (2009): 982-1021. [Google Scholar]
26. S. Kalia. B. Kaith, and I. Kaur. Pretreatments of natural fibers and their application as reinforcing material in polymer composites-A review. Polym. Eng. Sci. 49 (2009): 1253-1272. [Google Scholar]
27. International Cast Polymer Alliance, Solid surface properties and applications. Arlington, ICPA (2003): 8. [Google Scholar]
28. T. H. Wu, A. Foyet, A. Kodentsov, L. G. J. van der Ven, R. A. T. M. van Benthem, G. de With. Curing and percolation for carbon black-epoxy-amine nanocomposites. Compos Sci Technol. 181 (2019) DOI: https://doi.org/10.1016/j.compscitech.2019.05.029. [Google Scholar] [CrossRef]
29. G. C. Psarras. Conductivity and dielectric characterization of polymer nanocomposites. In Physical properties and applications of polymer nanocomposites. Eds. Tjong SC, Mai Y-W. Woodhead, Cambridge (2010): 31-69. [Google Scholar]
30. J. Gassan, and A. K. Bledzky. The influence of fiber-surface treatment on the mechanical properties of jute-polypropylene composites. Composites. 28 (1997): 1001-1005. [Google Scholar]
31. T. Collings. Handbook of polymer fiber composites. Longman Scientific and Technical, UK (1994366. [Google Scholar]
32. D. N. Saheb, and J. P. Jog. Natural fiber polymer composites: A review. Adv Polym Technol. 18 (1999): 351-363. [Google Scholar]
33. C. S. Tyberg, K. M. Bergeron, M. Sankarapandian, P. Singh, A. C. Loss, D. A. Dillard, J. E. McGrath, and J. S. Riffle. Structure-property relationships of void-free phenolic–epoxy matrix materials. Polymer. 41(2000): 5053-5062. [Google Scholar]
34. S. L. Gibson, V. Baranauskas, J. S. Riffle, and U. Sorathia. Cresol-novolac epoxy networks: Properties and processability. Polymer. 43 (2002): 7389-7398. [Google Scholar]
35. V. Alvarez, A. Vazquez, O. De La Osa. Cyclic water absorption behavior of glass-vinyl ester and glass-epoxy composites. J. Compos. Mater. 41 (2007): 1275-1289. [Google Scholar]
36. S. Marais, M. Metayer, T. Q. Nguyen, M. Labbe, and J. M. Saiter. Diffusion and permeation of water through unsaturated polyester resins-influence of resin curing. Eur Polym. J. 36 (2000453-462. [Google Scholar]
37. A. M. Visco, N. Campo, and P. Cianciafara. Comparison of seawater absorption properties of thermoset resins-based composites. Composites Part A Appl. Sci. Manuf. 42 (2011): 123-130. [Google Scholar]
38. F. A. Ramirez, L. A. Carlsson, and B. A. Acha. Evaluation of water degradation of vinyl ester and epoxy matrix composites by single fiber and composite tests. J. Mater. Sci. 43 (2008): 5230-5242. [Google Scholar]
39. A. N. Fraga, V. A. Alvarez, A. Vazquez, and O. De La Osa. Relationship between dynamic mechanical properties and water absorption of unsaturated polyester and vinyl ester glass fiber composites. J. Compos. Mater. 37 (2003): 1553-1574. [Google Scholar]
40. L. R. Bao, and A. F. Yee. Effect of temperature on moisture absorption in a bismaleimide resin and its carbon fiber composites. Polymer. 43 (2002): 3987-3997. [Google Scholar]
Cite This Article
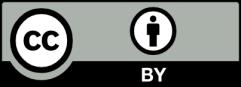
This work is licensed under a Creative Commons Attribution 4.0 International License , which permits unrestricted use, distribution, and reproduction in any medium, provided the original work is properly cited.