Open Access
ARTICLE
Study of the Effect of UV-exposure on HDPE/Carbon Black Composite Floating Structure
a
Central Institute of Petrochemicals Engineering & Technology, Raipur, C.G., India.
b
Department of Mechanical Engineering, Maulana Azad National Institute of Technology,
Bhopal, M.P., India.
* Corresponding Author: e-mail:
Journal of Polymer Materials 2022, 39(3-4), 183-193. https://doi.org/10.32381/JPM.2022.39.3-4.1
Abstract
HDPE material is found to be best suited material for the manufacturing of floating bed structure for the solar photovoltaic (PV) system due to its light weight and excellent mechanical & chemical resistant properties. However, the major restriction in this regard is the limited engineering design and also the effect of UV radiations present in the natural environment that leads to the degradation of the plastic materials. Hence, in order to improve its UV stability carbon black is incorporated into it as UV resistant additive and hollow cubical floats of such HDPE/carbon black composite material has been manufactured by rotational molding process and studied. Similarly, hollow cubical floats of virgin HDPE material was also manufactured and studied for comparison.The mechanical behavior of HDPE and HDPE /carbon black (CB) composite floats have been evaluated under artificial weathering condition (UV-exposure) at different intervals of time till 1152 hours, to perceive the lifespan of floating bed. It was observed that virgin material degrades more rapidly as compared to HDPE/Carbon Black (CB) composite floats. HDPE/CB floats do not show any major degradation of properties even after UV exposure. For virgin HDPE, the tensile strength & elongation at break were reduced to 42.13% & 52.9% respectively due to chemical cross linking along with the chain scission which causes photo degradation of the polymer whereas for HDPE/CB the value limits to 4.2% and 10.38% which confirms uniform dispersion of carbon black and good interfacial adhesion with HDPE matrix. The impact resistance did not show any significant change due to UV exposure in both the cases. However, hardness was increased more (upto 8.19%) in non-filled material due to deterioration of low molecular weight polymer but it was maintained in HDPE/CB due to the molecules of the filler and polymers are closely packed at macroscopic level so the intermolecular packing of material can be attributed to modifications in the amorphous regions. It is concluded that HDPE material with 2% CB depicts better mechanical properties for floating bed than virgin HDPE floats after accelerated UV exposure and is safe to bear the load of solar panels.
Keywords
Huge energy demand and continuous depletion of the fossil fuels focus on the sustainable energy sources which are unlimited and are also eco-friendly for the environment.[1, 2] Even though solar electricity has several advantages over other forms of energy generation, the major problem of it is the cost and requirement of vast land which is scarcely available in the world.[3] An innovative way of using solar power, i.e. floating solar power plants address this issue. The floating solar plant can be installed in any water bodies which will not only escalate the amount of power generation because of the cooling effect of water but conjointly decrease the need of costly land.
The desirable characteristics of the floating structures are: nontoxic, resistant to salt water and alkalis acids, UV resistant, recyclable, and be able to withstand temperatures from -60°C to 80°C for a long time underwater without retrograde in their mechanical properties.[4] Main materials which can be used as structures are plastic float elements and stainless-steel elements. Since, the metals are highly expensive also they are less resistive, various chemicals present in water bodies, which build interest for manufacturing of plastics float due to their low cost, good mechanical properties, light weight, resistive properties, durability and versatility than other materials.[5] Among the polymer family, High Density Poly Ethylene (HDPE) has governed a dominating position for the use of pontoons or floating blocks for the support structures of solar panel array.[6] Also, the mechanical properties of HDPE are found to be good and are not deteriorated with their use in natural weathering condition for a prolonged time make them ideal for making floating solar panel structure[7].
Polymer components normally fail either by bad engineering design or bad materials design or a combination of both[8]. Therefore, the design of floating bed or composition of polymeric materials is important for determining its durability. One of the possibilities of polymer degradation could be exposed to ultraviolet (UV) light. The morphological and mechanical properties of the polymer changes when subjected to UV radiations from the sun, which cause the photodegradation of the polymer because of the chain scission or chemical cross-linking. Therefore, it is important to find out a solution that can overcome this problem. Carbon black has been found to be the most effective stabilizer for polyethylene plastic with respect to degradation due to light and weathering.[7] The stability is very important when the material is subjected to exposure to sunlight and weathering over long periods of time.[9] Carbon black acts as a light stabilizer in polyethylene which absorbs light from the entire range of the solar spectrum and protects the interior of the plastic from the penetration of high energy photons. The resistance to degradation of plastic floats depends upon the particle size of carbon black used and its type, furthermore the scattering of the carbon black in the base matrix and its concentration also plays a vital role in resisting against the UV radiation[10]. Many researchers have reported the evaluation of mechanical and electrical properties of carbon filled polymeric materials[11].
L.C. Mendes has studied mechanical, thermal and microstructure evaluation of HDPE after weathering and concluded that non stabilized HDPE material is mechanically dead after 2500 hours of UV exposure [12].
The variations and changes in structure and mechanical properties of compression molded samples of commercial HDPE were reported by Carrasco et Al [13] when subjected to natural aging during a Canadian winter. They considered that there is a drastic decrease in impact energy of HDPE due to the loss in crystallinity and thermal fatigue. Gonzalezet al [14] has reported the effect of mineral fillers on photo-oxidation of HDPE in a UV-weathering chamber. They observed that the degradation follows a free radical chain mechanism and CaCO3 slows the carbonyl and hydroperoxide functional group formation acting as a protective barrier for UV light penetration.
The objective of this research work to study the effect of accelerated UV radiations on HDPE floats (conditioned in UV weatherometer at the intervals of 168, 360, 504, &1152 hours) before and after incorporation of carbon black, by evaluating the mechanical properties like tensile strength, elongation, load bearing capacity, impact strength, hardness and Young’s modulus at different time interval. Also the load bearing capacity of the material has been observed to sustain in the given loading condition.
2.1 Manufacturing of HDPE/CB Composite Floats by Rotational Molding Process
HDPE 010DP45U [15] grade virgin material from Indian Oil Corporation Limited (IOCL) has been chosen for the manufacturing of the floats. Similarly, a cubical float having size as 342 mm x 342 mm x 342 mm made of virgin HDPE (Fig. 1a) and HDPE with 2% carbon black (Fig. 1b) has been manufactured by rotational moulding process. Rotational moulding is four step processes, which are: stocking of the mould with resin along with heating as well as rotating of the mold and further cooling of the mold and lastly product removal. In a cold mold, the weight which is predetermined comprising polyethylene powder has been loaded when it was closed. Later that mold is heated as well as rotated after transferring it to the oven. The most commonly used temperature is up to 250°C.[16] The Float processing technique, rotational molded floats are stress free with strong outside corner (no weld lines, no gate marks).
Figure 1. (a) Virgin HDPE floats, (b) HDPE/CB Composite Floats made by Rotational Moulding process
2.2 Preparation of Virgin HDPE and HDPE/CB Composite Samples
The filler carbon black (CB) amalgamated with HDPE material using a high-speed blender for at least 5 min in a concentration 2% by weight. Then the mixture so formed is processed in a twin-screw extruder to produce granulated composites. The test specimens of virgin HDPE and HDPE/CB composite have been prepared by Injection moulding machine (JIT make, the Philippines, 80T capacities) for measuring different mechanical properties as per international standards (ASTM) [17].
2.3 Conditioning of Samples by UV Weathering
Moulded HDPE and HDPE/CB samples have been conditioned in UV Weathering Chamber (Q Lab, USA make, model no. QUV/SE/240). The specimens have been exposed (Fig.2) to the action of weathering (Accelerated UV exposure) in agreement with ASTM G 154.[18] This instrument has eight UVA-340 lamp of 40W each, providing 8 hours cycle for irradiance of 0.73 W/m2 at 340 nm wave length with an incident radiation beam at an angle of 24o and the black panel temperature of 60 (±3) °C. After irradiance cycle, 4 hours condensation cycle at 50 (±3) °C-black panel temperatures is maintained.
Figure 2. Specimens placed for ageing in QUV weatherometer
2.4 Evaluation of Mechanical Properties
The mechanical properties have been evaluated by taking 5 specimens from each sample and the average values were reported.
2.4.1 Tensile Strength, Maximum Load, Young’s Modulus & Elongation at break
The tensile strength and elongation at break (%) of weathered HDPE and HDPE/CB samples have been determined using Universal Testing Machine (Instron, USA make, Model: 3382K6825, 100 KN capacity). The test was conducted according to ASTM D 638[19] at a speed of 100 mm/min, gauge length of 115 mm at a temperature of 23± 2oC and relative humidity of 50 ± 5%.
The Izod impact test (notched) has been conducted in an Impact testing machine (Tinius Oslen, USA make, Model-IT 504). The test has been conducted according to ASTM D 256[20] using hammer energy of 24.838 J at a temperature of 23± 2oC and relative humidity of 50 ± 5%.
The hardness of samples before and after ageing has been determined by Shore D-Durometer (MICROTEST make, Model: 1993). The test has been conducted according to ASTM D 2240 [21] at a temperature of 23± 2oC and relative humidity of 50 ± 5%.
3.1 Analysis of Mechanical Properties
The initial properties i.e., properties before UV Exposure and properties after UV exposures with or without carbon black (CB) have been measured & compared in different interval of time.
Tensile strength is an important property for analysis of product in terms of its mechanical strength. The variation in tensile strength before the weathering conditions (at 0 hour) and after accelerated weathering (UV radiation) with or without carbon black in different intervals of time have been reported and shown in Fig.3. The tensile strength decreases gradually in early stages after the UV exposure and then the deterioration is more & finally value of 14.64 MPa is recorded after 1152 hrs of accelerated UV condition in case of virgin HDPE material. However, due to incorporation of carbon black in HDPE the UV-degradation is hindered as carbon black act as a perfect light stabilizer at all wavelength. The TS values are not affected by exposure to UV environment and are well maintained within the range of 23 to 21 MPa under same weathering condition.
Figure 3. The variation of tensile strength of HDPE and HDPE/CB composite w.r.t duration of UV-exposure (in hours) (with and without carbon black)
3.1.2 Maximum Load Bearing Capacity
The maximum load bearing capacity of the samples were also studied (Fig 4). This is one of the most important properties to be analyzed as the HDPE material used in cubical blocks are being used for supporting structure of the different shape and size solar panels in water bodies. From the figure it was observed that the maximum load bearing capacity of the sample with carbon black after UV-exposure is nearly constant and well maintained while it decreases gradually for the sample without carbon black as the exposure time increases. After 1000h of exposure to accelerated weathering, the HDPE/CB composite material has the tendency to hold a constant load of 991.78N without rupture, compared to virgin HDPE sample (637.81N). The material may fragile but do not break in this region.
Figure 4. The variation of Load bearing capacity w.r.t exposure time in hours after UV exposure with and without carbon black
The variation in Young’s modulus is shown in Fig. 5. The Young’s modulus of UV stabilized HDPE with carbon black is nearly unchangeable and increased after incorporation of carbon black because of the strong coalition among the filler particles and polymer chains and/or between particles and particles of the filler and polymer. The value varies in the range of 924-995 MPa which showed a good sign of material stability. The reduction in modulus of virgin HDPE material was attributed to changes in molecular mobility of the sample when exposed to UV radiation. For stabilized HDPE, the values of tensile stress and modulus of elasticity are practically constant. Also the stiffness of the composites increased because of the presence of rigid inorganic carbon black particles as the macromolecular chain segments become immobile.
Figure 5. Young’s Modulus vs UV-exposure time with and without carbon black
3.1.4 Elongation at Break Analysis
Several authors have shown that elongation at break value can be a good measure to monitor the ageing of polymers.[22, 23] During the initial stage of exposure, the value of elongation at break for virgin material drops up to 47% of the initial value and then a continuous drop in this value is noted until it reaches to a minimum value or constant. This type of behavior can be explained because of the obvious reason that the parental chain of HDPE separates or there is a division in the main chain that causes a decrease in the molecular weight of the material. Due to long exposure brittleness occurs and the sample loses this property. The variations of the elongation at break percentage values for the HDPE specimens before & after weathering are presented in Fig. 6.
Figure 6. The variation in the elongation at break value as a function of UV-exposure
Primarily, the chain was long and the molecules were entangled with weak van der waal forces to each other and the movement of entire molecules is associated with viscous flow. This is obviously depending upon the number of entanglements but at the time of steep drop in elongation at break these entanglements of the molecules get reduced or break down occurs because of the chemical changes like formation of carbonyl groups that reduces the entanglements.[24] On the other hand after mixing with carbon black, since the chain mobility of the polymer decreased due to the presence of filler which results in lower deformability of the composites because of the polymer-filler interaction resulting in diminution of the break point.[25] The inflexibility of the composites rest on the uniformity of the distribution of filler particle in the base material and the interfacial adhesion between the filler particle and the base material.[26] Compared with the non-filled material, the value decreased from 65.4% to 54.18 % but later on maintained up to 39.28% of elongation.
3.1.5 Impact Strength Analysis
The impact Strength of the samples before and after UV exposure of the HDPE sample with or without carbon black at different intervals is shown in Fig.7. The decrease of impact strength in starting of HDPE samples is mainly due to deterioration of low molecular weight polymer present in PE due to UV exposure for virgin material. The impact strength of HDPE/carbon black composite decreases with increase time of exposure. This is because of the filler particle blocks the roving of macromolecule chain segments, which limit the ability of composite to accommodate the contortion and to the speedy crack distribution along the interface of the filler-matrix.[27] The main reason for the reduction of impact strength is the generation of cracks on the weaker interfacial regions due to the filler content that increase the interfacial regions as the crack propagation do not resisted by interfacial regions more effectively as the polymer matrix can.[28] The exposure to UV light does not show any major effect on the impact strength in case of carbon filled HDPE. It can also be stated in this way that UV exposure is neither creating a tough or hard material as well as nor forming any kind of cracks in the weaker regions of the interfacial areas of the composite.
Figure 7. Variation of impact strength of HDPE with and without carbon black after UV exposure
The results of hardness analysis are shown by Fig. 8. The aged samples had higher values of hardness than found for the untreated sample. The percentage of carbon shows a negligible effect on the hardness before and after UV with carbon black. A slight variation occurs due to the molecules of the filler and polymers are closely packed at macroscopic level or the cross-linking reaction that heads towards the hard and dense formation of the structure.[29] Later on, it was investigated here that after 1152 hours of aging the hardness remains constant. The intermolecular packing of material can be attributed to modifications in the amorphous regions.
Figure 8. Hardness of HDPE with and without carbon black after UV exposure
In this study, the effect of UV-exposure on the various mechanical properties of virgin HDPE and HDPE/carbon black composites has been assessed. The following conclusions have been drawn from this research work:
1. The tensile strength is reduced from 25.3 MPa to 14.64 MPa after accelerated UV exposure in case of virgin HDPE material while the strength is well maintained (from 23.22 to 21.19MPa) for the HDPE/CB composite even after exposed to UV radiation. It was observed that after 1000h of exposure to accelerated weathering the carbon filled material had a tendency to hold a constant load of 991 N without rupture, compared to non-filled sample (637.81N). The loss of tensile strength of weathered samples for HDPE/CB composite is very less than non-filled sample and not affected much by the accelerated UV weathering condition.
2. The value of elongation at break is decreased from 65.4% to 54.18 % when carbon black is added to HDPE material but maintained upto 39.28% when exposed to UV radiation. The elongation at break is reduced to 12.48% in case of virgin HDPE material. The gradual and progressive deterioration of the elongation at break could be mainly due to the presence of low molecular weight species in HDPE after 1152 hrs of accelerated UV exposure.
3. The impact resistance did not show a significant change in both the cases during this period, the value varies in the range of 13.54 –10.06 KJ/m2. However, the hardness is increased more in virgin sample from 61 to 66 (Shore D). Increase in hardness after weathering of samples indicates increase in crystallinity of the material as well as cross linking of polymer which is not found in HDPE/CB composite material.
4. HDPE filled with carbon black technology delivers a substantial improvement in mechanical properties, which includes increased environmental stress crack resistance (ESCR), increased top load resistance for higher stacking requirements and ability to lightweight containers while maintaining drop impact resistance.
It is concluded that the mechanical properties of HDPE/CB composite material after accelerated UV exposure was not much affected as compared to virgin HDPE sample. Therefore, it is good to manufacture HDPE/CB floating bed of solar PV system that can bear the load of solar panels and other accessories mounted over it on the surface of water bodies. Further studies can be done using FRP material in place of steel structure. Also the effect of water mounted solar PV system on aquatic life and effect of air Impact on design can be considered for future studies.
References
1. A. K. Akella, R. P. Saini and M. P. Sharma, Renew. Energ. (2009): 34, 390–396. [Google Scholar]
2. J. P. Painuly, Renew. Energ. (2001): 24, 73–89. [Google Scholar]
3. A.K. Sahu, N. Yadav and K. Sudhakar, Renew. Sustain. Energy Rev. (2016): 66,815–824. [Google Scholar]
4. C. G. Granqvist, Adv. Matter. (2003): 66, 1789–1803. [Google Scholar]
5. A. Ammala, S. Bateman, K. Dean, E. Petinakis, P. Sangwan, S. Wong, Q. Yuan, Yu. Long, C. Patrick, and K.H. Leong, Prog. Polym. Sci. (2011): 36: 1015–1049. [Google Scholar]
6. N. Krishnaveni, P. Anbarasu, and D. A. Vigneshkumar, IJCRME (2016): special issue 2455-5428. [Google Scholar]
7. F. Carmona and J. Ravier, Carbon (2002) 40: 151–156. [Google Scholar]
8. G. Scott, Polymers and the environment, University Birmingham, Letchworth UK, Royal Society of chemistry, 1999: ISBN 0-85404-578-3. [Google Scholar]
9. M. Maryudi, A. Hisyam, R. M. Yunus, and M. D. H. Bag, IJERA. (2013) 3: 1156–1165. [Google Scholar]
10. W.T. Wallder, W. J. Clarke, J.B. Decoste and J. B. Howard, Ind. Eng. Chem. Res. (1950) 42: 2320–2325. [Google Scholar]
11. Z. Chen, L. Christensen and R. Dahn, J. Appl. Polym. Sci. (2003) 90, 1891–1899. [Google Scholar]
12. L.C. Mendes, E.S. Rufino, Filipe O.C. de Paula and A.C. Torres Jr., Polym. Degrad. Stab. (2003), 79: 371–383. [Google Scholar]
13. P. Pages, F. Carrasco, J. Saurina and X. Colom J., Appl. Polym. Sci. (1996) 60: 153–163. [Google Scholar]
14. A. V. Gonzalez, J. M. Cervantes-uc and L. Veleva, Polym. Degrad. Stab. (1999) 63: 253–260. [Google Scholar]
15. http://polymerdatabase.com/Commercial%20Polymers/HDPE.html [Google Scholar]
16. C. A. Harper, Handbook of Plastic Processes, John Wiley & Sons, Inc., publication, 2006, ISBN- 13-978-0-471-66255-6. [Google Scholar]
17. V. Shah, Handbook of Plastic testing technology, Wiley, 2007, ISBN: 0470100419. [Google Scholar]
18. ASTM G 154-04 Standard Practices for Operating Fluorescent Light Apparatus for UV Exposure of Non-metallic Materials. [Google Scholar]
19. ASTM D 638 Standard Test Method for Tensile Properties of Plastics. Annual book of ASTM standards, Philadelphia (PAAmerican Society for Testing and Materials. [Google Scholar]
20. ASTM D 256 Determining the pendulum impact resistance of notched specimens of plastics. Annual book of ASTM standards, Philadelphia (PAAmerican Society for Testing and Materials. [Google Scholar]
21. ASTM D2240 Standard test method for rubber property durometer hardness, Annual book of ASTM standards, Philadelphia (PAAmerican Society for Testing and Materials. [Google Scholar]
22. A. Torikai, H. Shirakawa, S. Nagaya and K. Fueki, J. Appl. Polym. Sci. (1990) 40: 1637–1646. [Google Scholar]
23. H. D. Hoekstra, J. L. Spoormaker and J. Brean, Macromol. Mater. Eng. (1997) 247: 91–110. [Google Scholar]
24. K. Rajakumar, V. Sarasvathy, A.T. Chelvan, R. Chitra, and C.T. Vijayakumar, J Polym. Environ. (2009): 191–202. [Google Scholar]
25. I. Chodak and I. Krupa, J. Mater. Sci., (1999) 18: 1457–1459. [Google Scholar]
26. H. Tang, Z. Y. Liu, J. H. Piao, X. F. Chen, Y.X. Lou and S. H. Li, J. Appl. Polym. Sci. (1994) 51: 1159–1164. [Google Scholar]
27. Y. W. Leong, M.Z.A. Ishak and A. Ariffin, J. Appl. Polym. Sci. (2004) 91: 3327–3336. [Google Scholar]
28. M. Rusu, N. Sofian, and D. Rusu, Polym. Test. (2001) 20: 409–417. [Google Scholar]
29. J. V. Gulmine, P. R. Janissek, H. M. Heise, and L. Akcelrud, Polym. Degrad. Stab. (2003) 20: 385–397. [Google Scholar]
Cite This Article
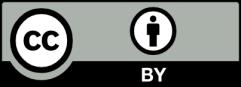
This work is licensed under a Creative Commons Attribution 4.0 International License , which permits unrestricted use, distribution, and reproduction in any medium, provided the original work is properly cited.