Open Access
ARTICLE
Preparation of Natural Rubber/Cloisite-Na+ nanocomposite in Latex Stage and its Characterization for Mould Application
1
Malaysian Rubber Board, Engineering and Technology Division, 47000,
Sungai Buloh, Selangor, Malaysia.
2
School of Chemical Engineering, Hanoi University of Science and Technology,
No 1 Dai co Viet, Hanoi, Vietnam.
* Corresponding Author: e-mail:
Journal of Polymer Materials 2022, 39(1-2), 151-166. https://doi.org/10.32381/JPM.2022.39.1-2.10
Abstract
In this work, a pure gum mould made of prevulcanized natural rubber/cloisite-Na+ nanocomposite (PVNR/CN) was prepared and characterized for ornament application. The suitable conditions to prepare PVNR/CN latex mixtures and the properties of the resulting PVNR/CN nanocomposites were investigated. The optimum CN concentration in the latex mixture was 1.0 phr, with the properties of 60 wt% total solid content, more than 600 sec mechanical stability time, lower than 350 cP Brookfield viscosity, and pH 10. The properties of PVNR/CN nanocomposite showed high strength, moderate hardness, and good thermal stability. The morphology by TEM showed well dispersion of CN particles in between the rubber dispersoid. The PVNR/CN nanocomposite as a mould was evaluated by shrinkage measurement. The presence of 1.0 phr CN in the PVNR/CN nanocomposite achieved the least shrinkage. The reproduced object using the PVNR/ CN nanocomposite as a mould showed complete fine details similar to the original object via visual observation.Keywords
Natural rubber /Cloisite-Na+ (NR/CN) nanocomposite is one of the propitious green materials, so it is deemed to be worthy of being used for making a gum mould, for instance, it is indispensable in decorative ornament and architectural applications. Moreover NR/CN nanocomposite has a multiphase structure comprises of nanoparticles of inorganic filler, i.e., naturally occurring nanoclay dispersed in the microparticles of naturally occurring polymer, i.e., natural rubber. Such a hierarchical structure could reflect the outstanding properties of the nanocomposite for the preparation of NR pure gum mould.
NR/CN nanocomposite can be obtained by incorporating CN dispersion into NR in the latex stage by mixing techniques. Cloisite-Na+ (CN) or Na+-montmorillonite belongs to the family of the phyllosilicate clay mineral with layered structure in the order of 1 unit of octahedron layer of alumina sandwiched by 2 units of silica tetrahedral layers in a 2: 1 structure. The layered silicates of CN may be intercalated and exfoliated in the aqueous medium of latex after being induced by mixing. Besides, water molecules could easily penetrate the CN structure due to the weak intermolecular forces between the CN layers by the presence oxygen atoms on top and base of the lattice layers of CN[1], in which it is possible to easily disperse the CN throughout the NR latex. Hence, it is anticipated that NR/CN nanocomposite prepared in the latex stage could provide a better distribution of CN in the NR matrix and subsequently improve the properties of the NR/ CN pure gum mould[2-3].
The properties of NR pure gum mould may be distinguished from the reported works[4-8] since it is tailored to ornament and architecture applications. The intended application in this study requires specific properties instead of high mechanical properties such as tensile and hardness, as compared to the current research focuses, especially in the automobile industry[9].
In the present work, NR latex, a naturally occurring polymer derived from tree saps of Hevea brasiliensis, is proposed as a starting material to prepare pure gum mould. NR owns a very long chain with high entanglement of cis-1,4 polyisoprene units giving the molecular weight more than 106 g/mol[9]. These characters reflect remarkable properties such as good elasticity, flexibility, durable, and very versatile art material. Thus, it is expected that NR in the latex stage, when suitably compounded, could be an ideal starting material for malleable gum mould preparation.
Pure gum mould is defined as a shaped cavity used to construct a definite form of fluid material, i.e., NR latex[10-11]. The purpose of making pure gum mould is to produce replicates from the original object that acts as a master. As reported in the previous work[12], any natural latex was suitable for making mould due to several advantages such as cheaper, greener, easy to remove casting object from mould, and could retain its shape after being used repeatedly. synthetic rubber moulds are usually more costly and may release offensive odour. Some are very difficult to remove the casting object due to high adherence and sensitivity to moisture. The mould-making process was more complicated as users will need to prepare two different parts of starting liquid materials accurately to achieve a useable mould. In this case, a compounded natural latex is what one's needs to make a mould, as simple as pouring and waiting for the mould to set and dry.
In the commercial market, the final product is ready in liquid form before being moulded. Therefore, a liquid form of NR latex mixture with a suitable condition must be prepared to withstand the structure or shape of the mould upon drying. Thus, it is thought that the presence of nanoclay, i.e., cloisite-Na+ could help to reduce the shrinkage of the mould and withstand the shape since it is known that NR latex would have shrinkage after drying. This is partly due to the latex has high water content as well as the presence of volatile matters. Besides, throughout the years of developing NR/nanoclay nanocomposites, there was no quantitative data reported on the preparation of NR pure gum mould. Very limited work reported on this area and only highlighted more on a qualitative study such as the visual observations of resulting mould and object. Thus, in this preliminary work, we will quantitatively determine the suitable condition of NR/CN latex mixture before being moulded and the properties of mould prepared from the optimized latex mixture.
In the current work, the effect of CN concentrations on the properties of NR/CN latex mixture and NR/CN nanocomposite was studied. NR used in this study was prevulcanized NR latex (PVNR). The physicochemical properties of PVNR/CN latex mixture were determined, for instance, mechanical stability time (MST), Brookfield viscosity, zeta potential and pH. These latex properties are essential to ensure latex stability during storage and transportation, and study flow behaviour during mould making process. The mechanical properties of the PVNR/CN nanocomposite, such as tensile and hardness, were investigated. Other supporting characterizations include thermal properties measured by the thermal gravimetric analyzer (TGA), and morphology observations using a transmission electron microscope (TEM) were also presented. For the preparation of pure gum mould, the shrinkage studies of the PVNR/CN pure gum mould and observations of reproduced objects prepared using optimized pure gum mould also were discussed.
Natural rubber latex in the prevulcanized form, PVNR was purchased from Getahindus. Cloisite® Na+ was purchased from Galin Enterprise, Worldwide. Wingstay L was purchased from Excelcos Sdn Bhd and plaster of paris (POP) used was obtained commercially.
Nanoclay Cloisite-Na+ (CN) and antioxidant Wingstay L dispersions were prepared by mixing the respective powder with water and dispersing agent. The dispersion was then transferred into a milling jar containing ceramic pebbles and subjected to milling process on a rolling machine for 48 hours at room temperature (RT). The total solid content (TSC) of the dispersion was then determined.
Preparation of prevulcanized natural rubber-Cloisite Na+ (PVNR/CN) nanocomposite
PVNR latex was firstly sieved to remove the small coagulum. The antioxidant and various concentrations of nanoclay dispersions, i.e., 0.5, 1.0, 1.5, and 2.0 phr, were added into the PVNR latex. After that, the mixture was stirred homogeneously at RT. The homogeneous latex mixture was then poured into an aluminum paper-coated support case measuring 14 cm × 10.5 cm until half of the mould was filled. Then, the latex mixture was dried via two routes, i.e., (1) at RT and (2) in an oven at 70°C. Once the top layer was gelled, the object was placed on the gelled surface and the remaining latex mixture was poured into the support case until the object was fully covered before drying according to the two routes mentioned above, respectively, to form PVNR pure gum moulds. Once dried, the object was taken out and the PVNR pure gum mould was formed and ready to be filled with plaster of paris (PoP) to reproduce the object. The flowchart of the preparation of PVNR pure gum mould is shown in Figure 1, respectively. The weight of the weight were constant. The length and width shrinkages PVNR pure gum mould was recorded weekly until the were calculated according to the equations below:
Figure 1: Flowchart of preparation of PVNR/CN nanocomposite as a pure gum mould.
About 1 gram of latex was weighed (m0) and was poured into a petri dish. The latex was swirled until the latex covered the petri dish completely. Then, it was dried in the conventional oven for 2 hours at 100°C. The dried rubber was then transferred into a desiccator and cooled to RT. The weight of dried rubber was recorded (m1). TSC was calculated based on the equation below. The TSC was carried out with triplicate[14]
Mechanical Stability Time (MST)
MST of latex with ± 60 w/w% of TSC was determined at 35°C using a Klaxon Mechanical Stability Tester as specified by the International Standard Organisation (ISO). The MST was taken by observing the endpoint in time (seconds) of the first sign of flocculation. The sign of flocculation was determined by spreading in a thin film of latex on the palm of the hand.
Viscosity of the latex was determined by using Brookfield viscometer Model LVF by Brookfield Engineering Laboratories, Inc., based on ISO 1652. The latex was tested at 30 rpm and 60 rpm using various spindles from 1 to 4 depending on the viscosity of the latex.
The zeta potential of the latex was measured using a ZetaPlus Zeta Potential Analyser, Brookhaven Instrument Corporation. Latex weighed about 0.02 grams was diluted with 15 ml of distilled water. The zeta potential of the latex was measured from their electrophoretic mobility by employing photon correlation spectroscopy of quasi-elastically scattered light, which is based on the fluctuation of the average, scattered, laser light intensity. The average zeta potential values of five replicates were then calculated.
pH of the latex was measured using a Hanna pH meter, Model HI 2211 equipped with the electrode probe, M 411087. The electrode probe was placed in the beaker filled with latex, and pH reading was then recorded.
The tensile properties were measured according to ISO 37. The film samples, with a thickness of about 1 mm, were cut with a Dumbbell-shaped Type 2. The test piece was stretched at a crosshead speed of 500 mm/ min using Universal Testing Machine INSTRON. The data of the stress and strain of the sample were plotted in a stress-strain curve.
The hardness of the rubber was carried out according to ISO 48[13]. The hardness is expressed in international rubber hardness degrees (IRHD). The results were taken as a median.
Thermogravimetric Analysis (TGA)
The thermal stability of rubber was determined using TGA (Perkin Elmer TGA-STA 6000). The measurement was performed at a heating rate of 20°C/min under nitrogen flow over a temperature range of 30 to 800°C. A sample weighed approximately 15-20 mg and was placed in a ceramic pan before being positioned on the thermo-balance and heated with high-temperature furnace. The weight change of the sample as a function of temperature was measured and recorded as a thermogram.
The morphology at high magnification was observed by a transmission electron microscope (TEM), FEI TECNAI G2, at an accelerating voltage of 200 kV. Ultra- thin sections of the samples were prepared using a Leica UC7 at 183 K before being transferred to a copper grid for TEM analysis. The samples were stained with 2 w/w% osmium tetroxide solution for 3 hours.
Reproduce object from plaster of paris (PoP) - casting object
The object was reproduced using PoP mixture. PoP and water were mixed with a ratio of 2:1 homogenously. The PoP mixture was slowly poured into the PVNR/CN pure gum mould until the space was evenly filled with the mixture. Then, the PoP mixture was dried at RT for 2 days. The PoP object was then taken out from the PVNR/CN pure gum mould after dried.
Physicochemical properties of PVNR/CN latex mixture
Table 1 shows the TSC, MST, Brookfield viscosity, zeta potential and pH for PVNR latex, CN dispersion, and PVNR/CN latex mixtures.
The TSC of the PVNR latex was 61.02 w/w%, and the CN dispersion was 23.40 w/w%. The TSC of PVNR/CN latex mixtures were adjusted similar to PVNR latex.
The MST is an important parameter for colloidal stability by applying high shear force onto PVNR latex. The PVNR latex was stable for about 800 seconds after being exposed to high shear force. The MST of PVNR/CN latex mixtures decreased as the CN concentration increased. The lowest stability time was about 390 seconds for PVNR/CN- 2.0 phr latex mixtures. It indicates that the colloidal stability of PVNR/CN latex mixture is weakened by high shear force. This is possibly due to (1) CN is suspended by high-speed stirring, which forms an interaction between the exchangeable cation of the CN, i.e., Na+ and negatively charged ions that present at the outer layer of latex particles, or (2) high-speed stirring applied would induce faster coagulation due to shear force between CN and NR latex particles. Higher MST is more suitable for the stability of PVNR/CN latex mixtures since it is to ensure their colloidal stability during transportation and could be kept at a longer storage period.
The Brookfield viscosity of the PVNR latex was about 100 cP which was higher than high ammonia natural rubber (HANR) latex. This is due to the presence of additives in the PVNR latex that cause latex thickening. The viscosity was gradually increased as the concentration of CN increased up to 1.5 phr before an abrupt increase at the CN concentration of 2.0 phr. The higher the CN concentration, the higher the viscosity of the latex mixtures. The overall increase in viscosity may be related to the interactions of the CN and PVNR latex that restrict the motion of particles. This is due to swelling hydration of CN in water[15] that increased the volume by high water absorption, which may promote unrestrained thickening under shear. Hence, the latex mixture that is able to flow, which has low viscosity, is suitable to be used to make a pure gum mould. Since it can follow the shape of an object uniformly. In this case, Brookfield viscosity value for PVNR/CN latex mixture should be controlled at below 350 cP to make a good pure gum mould. Furthermore, high viscosity latex mixture may cause instability for long-term storage as explained by MST values.
The properties of PVNR/CN latex mixtures were further investigated by zeta potential measurement. The zeta potential indicates the surface charges adsorbed on the outer layer of latex particles, which is negative for PVNR latex due to its high pH nature, and it is a common feature of any commercial NR latex. The zeta potential of PVNR latex and CN dispersion was measured to be -48 mV and -50 mV, respectively. The zeta potential was consistent as the CN concentration increased. Relatively constant zeta potential was observed in all dispersions prepared i.e. in the range of -45 mV to -50 mV, indicating that all the respective mixtures were very stable. Relating to pH, the values of latex mixtures was about more than 10, even at higher CN concentrations. This implies that the pH values were not affected by the addition of CN into the PVNR latex. Interestingly, these findings were in contradiction with the MST, where the MST decreased as the CN concentration increased. This may be explained by the factor of high shear force in MST measurement. This indicates that high shear force or vigorous stirring of the PVNR/CN latex mixtures will cause destabilization. If the latex mixture was slowly stirred or unstirred before the preparation of pure gum mould, the PVNR/CN latex mixtures would remain stable.
Properties of PVNR/CN nanocomposites
In this section, the PVNR/CN latex mixtures were used to prepare PVNR/CN nanocomposites. The properties of the resulting nanocomposites were investigated in terms of mechanical, hardness, thermal properties, and morphology.
For nanocomposite materials, tensile strength reflects the ability of the material to withstand the pulling forces applied onto the material. In the case of nanocomposite materials used for pure gum mould, the ability to resist breaking under tensile stress is one of the most important indication for strength and elasticity, for example, when the applied forces are used to demould a casting object from the mould.
Figure 2(A) depicts plots of the stress-strain for PVNR and PVNR/CN nanocomposites dried by heat-assisted at 70°C. The stress at break for PVNR as control was about 13.5 MPa at a strain of 680%. The stress at break was then increased to the highest, i.e., 16 MPa for PVNR/CN-0.5 phr and PVNR/CN-1.0 phr, respectively, with higher strain at breaks, i.e., 750% compared to PVNR. The stress at break of the PVNR/CN nanocomposites at 1.5 phr and 2.0 phr of CN was then decreased substantially to about 12 MPa, and the strains were decreased to 650%. The higher stress at break for the PVNR/CN nanocomposites at 0.5 and 1.0 phr of CN may be due to the presence of a suitable amount of CN, where it may have the optimum interaction with the rubber matrix. The decrease in stress at break at high CN concentration may be due to the agglomeration of CN particles, thus resulting in the weak interaction with rubber particles. The agglomeration of CN particles may easily break into small clusters upon straining. Besides, the curves were steeper as the CN concentration increased, indicating that the CN increases the stiffness of the PVNR/CN nanocomposite.
Figure 2.: Stress strain curve and initial stress at break at strain 300%, of (A) PVNR and (B) PVNR/CN nanocomposites- heat assisted at 70°C.
In order to confirm the role of CN in the PVNR pure gum mould, the initial stress at breaks was observed, as shown in Figure 2(B). The initial stress of PVNR/CN nanocomposite was abruptly increased compared to that of PVNR. The higher CN concentration, the higher stress at break at a strain of 300%. This may be due to the role of CN as a reinforcing filler in the pure gum mould, which may promote strain- induced crystallization[16-17]. Hence, the presence of a suitable amount of CN could enhance and improve the strength of PVNR/ CN nanocomposite.
Figure 3 shows the hardness for PVNR and PVNR/CN nanocomposites. The hardness of PVNR/CN nanocomposites was higher, i.e. more than 20, than that of PVNR, i.e., 18. The hardness increased gradually as the CN concentration increased. This indicates that the CN could resist the mould from mechanical deformation such as indentation or abrasion. According to ISO 48[13], the hardness of rubber less than 35 is categorized as low, which means soft. Likewise, the suitable characteristics of pure gum mould should be soft but then has good strength and elasticity. Hence, the hardness for PVNR/CN nanocomposites were less than 30, which implies that these nanocomposites were soft type.
Figure 3.: Hardness of PVNR and PVNR/CN-0.5 phr and NR/CN-2.0 phr - heat assisted at 70°C.
The thermal properties of PVNR, PVNR/CN-1.0 phr and PVNR/CN-2.0 phr nanocomposites are shown in Figure 4. The purpose of the measurement is mainly to investigate the resistance of the nanocomposite after adding CN (nanofiller) that is exposed to heat by high temperature during storage.
Figure 4.: Thermal gravimetric (TG) curves for PVNR, PVNR/CN-1.0 phr and PVNR/CN-2.0 phr nanocomposites (heat assisted at 70°C).
The TG curves showed a single-step degradation for PVNR and PVNR/CN nanocomposites, which indicated the degradation of one primary polymer, i.e., NR. The weight decomposition percentage of PVNR was in the range of 92 - 94 wt.%, respectively. A small second-step degradation with weight decomposition of about 2 wt.% may represent the loss of some minor impurities naturally present in PVNR, and the additives in the PVNR.
Table 2 shows the onset and maximum degradation temperature and mass residue at 600°C of PVNR and PVNR/CN nanocomposites. The onset and maximum degradation of PV rubber were 348°C and 375°C, respectively. The onset and maximum degradation temperature were dependent on the CN concentration, where the temperatures were shifted to a higher as the CN concentration increased. This may be contributed by the role of CN as an insulator, where it inhibited the motion of NR chains during heating. Furthermore, the CN may substitute the evaporated volatile matters during heating and leave them as a char, refer as mass residue after thermal decomposition[18]. The mass residue at 600 °C for PVNR, PVNR/CN-1.0 phr, and PVNR/CN-2.0 phr nanocomposites was 0.3 wt%, 1.2 wt%, and 2.3 wt%, respectively. These residue percentages were consistent with the amount of CN added into the PVNR/CN nanocomposites. Hence, it can be deduced that the thermal stability of PVNR/ CN nanocomposites was improved even in the presence of small amount of CN.
The intrinsic morphologies of CN, stained PVNR, and PVNR/CN-1.0 phr, captured with transmission electron microscope are shown in Figure 5. The morphology of CN exhibited a typical nanolayer structure of the ultrathin 2D, as illustrated in Figure 5A.
Figure 5.: Transmission electron microscopy images for (A) CN, (B) PVNR and (C) PVNR/CN-1.0 phr.
It was observed that PVNR and PVNR/CN nanocomposite were composed of about 1 micron of rubber particles, as shown Figure 5B and 5C. The gloomy domain represents the rubber particles, whilst the bright domain represents the CN particles. In the case of NR (Figure 5B), some rubber particles (blue arrow) exhibited gloomy colour compared to other rubber particles. This suggests the occurrence of intra-crosslinking by prevulcanisation[19-20] since prevulcanized natural rubber latex was used as a starting material.
The bright domains of CN were dispersed well in between the rubber particles after the addition of CN into NR. Range sizes of CN nanostructures, i.e., from 20 to 180 nm (less than 200 nm), were observed. Smaller nanosize particles (x) were postulated to be well distributed of CN. Whilst, bigger size particles, (y) may be form the agglomeration of CN. Interestingly, these nanometer sizes of CNs located surrounding the rubber particles form a matrix. It may be attributed to the mixing of CN with PVNR in the latex medium, conferring a better dispersion of CN in the rubber phase. As reported in the previous work[21], CN particle is strongly hydrophilic and easily suspended in the water medium, resulting in better interaction with latex particles in the water medium.
Thus, it is possible that the filler nanomatrix structure[22-23] in PVNR/CN nanocomposite is formed, which reflected the improved properties of PVNR/CN nanocomposite, particularly tensile properties even in the presence of a small amount of CN, as shown in stress-strain curve, Figure 2.
Properties of PVNR/CN Pure Gum Mould
The prepared PVNR/CN nanocomposite was hypothesized to be suitable for making a pure gum mould. To verify the suitability of the PVNR/CN nanocomposite for preparing pure gum mould, the shrinkage studies were investigated. The shrinkage study is essential since the mould is prepared from a latex mixture, which consists of about 30-40% of water. Therefore, it is anticipated that the incorporation of CN could hamper the shrinkage effect of the mould. Furthermore, the reproduction of the real object was also observed to confirm the hypothesis.
Figure 6 illustrates the length and width shrinkage percentages of the pure gum moulds made from PVNR latex and PVNR/CN latex mixture (0.5 – 2.0 phr of CN) dried at RT (A) and (B), and heat-assisted 70°C (C) and (D). The pure gum mould shrinkage was calculated based on the length and width that taken almost every day for the first 30 days and weekly afterward for over 4 months (130 days) observation, assuming that there was no shrinkage occurred on the first day the mould was prepared.
Figure 6.: Length and width shrinkage percentages of PVNR and PVNR/CN pure gum moulds (from 0.5 – 2.0 phr of CN) dried at RT (A) and (B), and heat assisted at 70 °C (C) and (D).
The length and width shrinkage for PVNR/CN pure gum moulds dried at room temperature RT) (Figure 6(A) and 6(B)) were declined gradually until 40 days of drying and constant up to 130 days. The longer period of drying was due to the absence of heat. The PVNR pure gum mould showed the highest length and width shrinkages, i.e., 5 and 8 %, respectively. The lowest shrinkages amongst all were calculated to be for pure gum mould made from PVNR/CN-0.5 phr and PVNR/CN-1.0 phr. The length and width shrinkages for the moulds were about 3 and 5 %, respectively.
In comparison to the moulds dried at RT, the length and width shrinkages of PVNR/CN gum moulds dried by heat-assisted (Figure 6(C) and 6(D)) were abruptly declined to less than 30 days and then almost constant to 130 days. A shorter drying period was expected due to the presence of heat. The length and width shrinkages for PVNR pure gum mould were calculated to be 7 and 10 %, respectively. These shrinkages were higher than pure gum mould dried at RT, as expected.
The pure gum mould prepared from PVNR/CN- 0.5 phr and PVNR/CN-1.0 phr showed the least length and width shrinkages, i.e., about 3 % compared to PVNR, PVNR/CN-1.5 phr, and PVNR/CN-2.0 phr. These findings were consistent with the observation that the PVNR/ CN-0.5 phr and PVNR/CN-1.0 phr latex mixtures showed better properties than PVNR/ CN-1.5 phr and PVNR/CN-2.0 phr latex mixtures. Furthermore, PVNR/CN pure gum mould dried in the oven showed a faster drying rate and less shrinkage; thus, dried mould using an oven at 70°C was chosen for further evaluation.
Overall, the shrinkages occurred for either PVNR or PVNR/CN pure gum moulds. The PVNR/CN-0.5 phr and PVNR/CN-1.0 phr pure gum moulds showed the least shrinkages when dried at RT and by heat-assisted at 70°C, suggesting the PVNR/CN nanocomposite with 0.5 and 1.0 phr of CN concentration may be suitable for preparing pure gum mould.
The proposed shrinkage occurrence for PVNR and PVNR/CN pure gum moulds is illustrated in Figure 7. The more shrinkage that occurred in PVNR pure gum mould may be due to the coalescent of latex particles during drying. In the case of PVNR/CN pure gum mould, the presence of CN silicate layers that localized in between the rubber particles upon drying, as observed by TEM (Figure 5), may hinder severe coalescence of the particles during drying. Hence, less shrinkage was observed for the PVNR/CN gum mould. Another hypothesis is that the round or layer shape of fillers may also influence the shrinkage, where the layer-shape filler may contribute to less shrinkage compared to round-shape filler. In other words, the presence of CN could maintain the final volume of the mould by filling the voids of evaporated volatile matters, mainly from the latex, during the drying stage.
Figure 7.: Illustration diagram of shrinkage phenomena upon drying for PVNR and PVNR/CN pure gum moulds.
Figure 8 shows the reproduced objects using (A) PVNR pure gum mould as control and (B) 1.0 phr PVNR/CN pure gum mould. Here, we chose 1.0 phr PVNR/CN pure gum mould to make reproduced object since it gave the least shrinkage of pure gum mould, suitable mechanical properties, and physicochemical properties of PVNR/CN latex mixture. PoP mixture was used as a casting material (reproduced object).
Figure 8.: The reproduced objects using (A) PVNR pure gum mould as a control and (B) PVNR/CN -1.0 phr pure gum mould.
It was observed that the reproduced objects from PVNR and 1.0 phr PVNR/CN pure gum moulds resembled the original object. The fine details of reproduced objects were palpable and accurately similar to the original ones. The reproduced object was found smaller by about 10% by length and width for PVNR pure gum mould calculated based on object size. In the case of PVNR/CN-1.0 phr pure gum mould, the reproduced object shrank lesser, i.e., about 3 % by length and width compared to the original one. Hence, it is confirmed that the addition of CN in the pure gum mould could hinder the shrinkage of the reproduced object when compared to control PVNR pure gum mould.
Based on the observation, PVNR/CN-1.0 phr pure gum mould was malleable; for instance, the mould did not damage when the reproduced object was demoulded. The reproduced object was easily demoulded from the mould since the mould was soft and high strength. The mould could withstand the weight of casting material without distortion. It is consistent with the mechanical properties such as tensile strength and hardness shown in previous figures. Furthermore, it was also observed that the shape and elasticity remained unchanged when the mould was kept at RT for more than a year. Hence, it can be deduced that the PVNR/CN pure gum mould, is easy to handle, durable, and successfully produced the casting material or reproduced object similar to the original object.
PVNR pure gum mould from PVNR/CN nanocomposite was successfully prepared in the latex stage via mixing technique and a subsequent drying process. The suitable CN concentration was found to be 1.0 phr for making a suitable PVNR/CN latex mixture and pure gum mould. The properties of PVNR/CN nanocomposite with 1.0 phr CN were found to be the highest with stress at break of 16 MPa and strain at break of 740%. However, the PVNR/CN nanocomposite was considered soft due to the hardness value less than 30. Morphology of PVNR/CN nanocomposite demonstrated that CN nanoparticles were well dispersed in between rubber particles forming a matrix. The gum mould made from 1.0 phr PVNR/CN nanocomposite exhibited the least shrinkages upon drying, about 3% for both width and length as compared to 7 and 10% in the control PVNR mould. The shrinkage has resulted in a marginally smaller reproduced objects, but it was undoubtedly able to produce high-quality copies with fine details, as seen by visual observation. It is concluded that the PVNR/CN mould with malleable and good strength could become a potential material for making mould for ornament application.
ACKNOWLEDGEMENT: This research was funded by the Malaysian Rubber Board for Scientific and Economic Advisory Council (SEAC) under project code S17HVRP0666. Special thanks and appreciate to Mr Shafuddin Omar, Mdm. Faezah Ismail, Mr. Hamdan Abu Bakar, Mr. Muhammad Saiful, Mdm. Siti Mahirah Romli, for their great assistance throughout the work.
CONFLICT OF INTEREST: On behalf of all authors, the corresponding author states that there is no conflict of interest.
References
1. J. Sapkota. Influence of clay modification on curing kinetics of natural rubber nanocomposites. MS thesis. (2011). [Google Scholar]
2. N. H. Yusof, M. S. Fauzi, M. S. Mazam, J. Rubber Res. (2011): 14, 4, 185-199. [Google Scholar]
3. N. T. Thuong, N. P. D. Linh, C. H. Ha, P. T. Nghia, S. Kawahara, Rubber Chem. Technol. (2020): 93, 2, 286-296 [Google Scholar]
4. M. Bhattacharya, M. Maiti, A. K. Bhowmick, Rubber Chem. Technol. (2008): 81, 5: 782-808. [Google Scholar]
5. S. Jayaraj, S. M. Egodage, S. Walpalage, J. Natl. Sci. Found. (2017): 45, 2. [Google Scholar]
6. S. C, George, R. Rajan, A. S. Aprem, S. Thomas, S. S. Kim, Polym. Test. (2016): 51, 165-173. [Google Scholar]
7. M. I. Fathurrohman, S. Rugmai, N. Hayeemasae, K. Sahakaro, Polym. Eng. Sci. (2019): 59, 9: 1830-1839. [Google Scholar]
8. K. Roy, S. C. Debnath, P. Potiyaraj, J. Elastomers Plast. (2020): 52, 2, 167-193. [Google Scholar]
9. S. K. Srivastava, B. Bhuyan, Rubber Nanocomposites and Nanotextiles in Automobiles. (2011). [Google Scholar]
10. S. G. McFeely, Teaching sculpture: a rationale and resource kit. PhD Thesis. (1983). [Google Scholar]
11. O. C. Z. Gotel, S. J. Morris, Crafting the requirements record with the informed use of media. First International Workshop on Multimedia Requirements Engineering. (20065-5 [Google Scholar]
12. R. M. Tsotorvor, Exploring natural latex for mould making in teaching sculpture. PhD. Thesis. (2016). [Google Scholar]
13. ISO 48:2010. Rubber, vulcanized or thermoplastic —Determination of hardness (hardness between 10 IRHD and 100 IRHD). [Google Scholar]
14. ISO 2004:2010. Natural Rubber Latex Concentrate —Centrifuged or Creamed, Ammonia-Preserved Types —Specifications. [Google Scholar]
15. F. Uddin F, Montmorillonite: An introduction to properties and utilization; Intech Open: London, (201811-12. [Google Scholar]
16. J. Carretero-González, H. Retsos, R. Verdejo, S. Toki, B. S. Hsiao, E. P. Giannelis, M. A. LopezManchado, Macromolecules. (2008): 41, 18, 6763-6772. [Google Scholar]
17. Y. Nie, L. Qu, G. Huang, B. Wang, G. Weng, J. Wu, Polym. Adv. Technol. (2012): 23,1, 85-91. [Google Scholar]
18. J. Wang, D. Chen, J. Nanomater. (2013). [Google Scholar]
19. K. L. Mok, A. H. Eng, Malays. J. Chem. (2018): 20, 118-127. [Google Scholar]
20. R. Roslim, K. S. Tan, J. Jefri, J. Rubber Res. (2018): 21,1, 1-16. [Google Scholar]
21. L. Bokobza, Nanomaterials, 2019, 9,1, 12. [Google Scholar]
22. N. H. Yusof, K. Noguchi, L. Fukuhara, Y. Yamamoto, S. Kawahara, Colloid Polym. Sci. (2015): 293, 8, 2249-2256 [Google Scholar]
23. N. T Thuong, T. A. Dung, N. H. Yusof, S. Kawahara, Polymer. (2020): 195, 122444. [Google Scholar]
Cite This Article
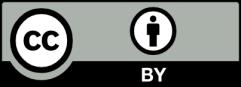
This work is licensed under a Creative Commons Attribution 4.0 International License , which permits unrestricted use, distribution, and reproduction in any medium, provided the original work is properly cited.