Open Access
ARTICLE
Toughening of Unsaturated Polyester Resin by Blending with Polyether Telechelics. Dependency of Toughening Efficacy on End Groups
1 School of Chemical Sciences, Mahatma Gandhi University, Kottayam-686560, Kerala, India.
2
Polymer Science and Rubber Technology, Cochin University of Science and Technology,
Cochin-682022, Kerala, India.
* Corresponding Author: e-mail:
Journal of Polymer Materials 2022, 39(1-2), 111-120. https://doi.org/10.32381/JPM.2022.39.1-2.7
Abstract
Polyether telechelics based on ethylene glycol,1,2-propylene glycol and 1,4- butylene glycol of with various molar masses and bearing at both terminals functional groups such as maleimide, itaconimide, nadimide and hydroxyl groups were individually examined as toughening agents for an unsaturated polyester resin (UPER). For a given telechelic, the toughening effect was evaluated at different mass ratios. The difference in toughening efficacy arose from the differential reactivity of the telechelics end groups combined with the unsaturation of the UPER with the reactive diluent, styrene. This causes a differential distribution of the polyether groups in the UPER matrices, resulting in a differential dipolar interaction of the polyether segments among themselves and with the UPER itself. The matrices cohesive strength is decided by these interactions, the possibility for which is decided by the spacing of these polyether segments in the matrix, as per the reactivity ratios between styrene-maleic complex pair and the polyether end groups. An increased inter-segmental spacing of polyether could diminish the chance for inter-segmental dipolar interactions that can stake the cohesive strength and thus the mechanical properties of the matrices. These aspects have been quantified in terms of their efficacy factors which conformed well to the strength and fracture properties of UPER blended in small proportions with the end-functionalized polyether telechelics.Keywords
Unsaturated polyester resins (UPER) continue to dominate the polymer industry even after a century of their introduction. Over these years, they were witnessing revolutionary changes in their structure or compositions to address various technical issues encountered then and there[1]. Unsaturated polyesters are, in reality, low molar mass polymers made from glycols and di- acids, dissolved in a vinyl monomer such as styrene. When catalyzed with a free radical initiator, they cure by copolymerization of the vinyl monomer with the unsaturated groups in the polyester backbone to yield a cross-linked or three-dimensional network. They are used widely due to their attractive properties like low cost, easy processability, good corrosion resistance and accessibility in a diversity of grades. Though they have stable structures and reasonably decent mechanical and thermal properties, they are not fit for pioneering engineering applications due to their poor fracture characteristics. Attempts to improve the fracture resistance through blends, interpenetrating polymer networks (IPNs), composites, nanocomposites etc. have met only with partial success[2]. Messori et al. produced toughened UPER by using poly (ɛ-caprolactone)-perfluoropolyether- poly (ɛ-caprolactone) block copolymers. A great enhancement observed in the absorbed energy at break display the finest toughening result of prepared copolymer[3]. Cherian et al. used polyurethane prepolymers for the modification of unsaturated polyester resin. The hybrid network's structure was developed by the copolymerization reaction between terminal hydroxyl groups of unsaturated polyester and isocyanate groups of polyurethane prepolymer.
Substantial enhancement was observed in the mechanical properties of the prepared blends[4]. Ternary polymer blends of unsaturated polyester (UP), polysulphide rubber (PSR), and poly-methyl methacrylate (PMMA) were shown a great enhancement in mechanical strength. The polymer blends that replace PSR with natural rubber (NR) possess superior mechanical properties to the former blend[5].
Poly (ethylene oxide) or poly (propylene oxide) and maleic anhydride were used to create ion conductive UPER. Synergistic conductivity effects, rubber elasticity, and high-water tolerance are all demonstrated by the cross- linked PEO-PPO network. These features enable extensive use under mechanical stress, ambient conditions, and even in water settings, which is difficult for ordinary ion-conducting systems[6,7].
Kozera et al. modified unsaturated polyester resin with triple functionalized polyhedral oligomeric silsesquioxanes (POSS) and double organo-functionalized polysiloxanes to provide it hydrophobic and ice-phobic qualities[8]. In line with these studies, we attempted to improve the toughness of the UPER matrix by combining it with a variety of end functional polyethers[9, 10, 11]. The end functional oligomers imparted good toughness characteristics which varied with the polyether, specifically with their end groups' reactivity with the reactive diluent.
In this paper, we present the impact of unsaturated imide-functionalized hydroxyl end capped polyols such as polypropylene glycol (PPG), and polyethylene glycol (PEG) with different molecular weight on the toughening of unsaturated polyester resin matrix and comparative strength and toughness of various UPER matrices blended with diverse molar-mass polyethers possessing maleimide, itaconimide, nadimide and hydroxyl end groups. An attempt has been done to correlate the differing toughening capability of the polyethers, based on the reactivity ratio of the unsaturated groups in the main chain and the reactive solvent with the end groups on polyethers. These reactivity ratios have a direct bearing on the distribution of the polyether and their dipolar interactions and crystallizability, adding to or staking the cohesive and fracture properties of the blend. All these changes in fracture properties are quantitatively evaluated and correlated to the nature of the end groups and their reactivity with the unsaturation in the UPER backbone and the reactive diluent. This paper examines all these from a quantitative perspective.
Polypropylene glycol (PPG) and poly tetramethylene oxide (PTMO) were obtained as gift samples from m/s Riotech Ltd., Pala, India. Polyethene glycol was purchased from Sigma Aldrich. UPER, methyl ethyl ketone peroxide and cobalt octoate were obtained from the open market. Other chemicals were used as received. UPER was a gift sample from M/s Riotech Industries, (MIE Mini Industrial Estate, Valavoor, Kerala 686635) of undisclosed composition (proprietary). The reactive diluent used is styrene (33-37 weight%). This permitted estimation of total “maleic-type” unsaturation in the UPER.
3. Method of preparation of different imide end functionalized polyether telechelics
At first, 4-maleimide/itaconimide/nadimide benzoic acid (MBA/IBA/NBA) was formed from maleic/itaconic/nadic anhydride and para-aminobenzoic acid. The formed amic acid was dehydrated by using acetic anhydride and sodium acetate to get MBA/IBA/NBA. The corresponding acid chlorides (MBC/IBC/NBC) were prepared by using thionyl chloride. Maleimide/Itaconimide/Nadimide end-capped oligomers (telechelics) were synthesized by reaction of maleimide/ itaconimide/nadimide benzoyl chlorides with the corresponding hydroxyl telechelics with varying molar masses, i.e. polypropylene glycol [PPG (with molecular mass 2000g/mole, 1000g/mole, and 400g/mole)], polytetramethylene oxide [PTMO (with molecular 2000g/ mole)], and polyethylene glycol [PEG (with molecular mass 2000g/mole)] using triethylamine for scavenging the HCl produced. The imide derivatives were yellow oily liquids and were characterized. Complete conversion of hydroxyl groups in the polyol backbone was confirmed from the absence of residual hydroxyl groups in the product. Characterization using FTIR, NMR, UV, and OH value calculations also confirmed the formation of the expected structure. The detailed synthetic procedures and characterization methods put out in our previous publications.[9,10,11]
Blends of UPER with the hydroxyl end polyethers were prepared by cell casting technique. The UPER was stirred well with the additives (1.5 phr, 2.5 phr, 5 phr, and 10 phr) using a mechanical stirrer at 2000 rpm for 45 minutes. The initiator methyl ethyl ketone peroxide (1.3 wt. %) and the promoter cobalt octoate (0.5 wt. %) were used to process the resin. The resin was then poured into a Teflon mould coated with a releasing agent. Samples for tensile test, impact test, flexural test, and fracture toughness tests were cast separately in appropriate moulds. Curing was done at room temperature for 24 hours followed by post-curing at 80°C for 3 hours. The unmodified UPER was also cast similarly.
Gel content of cross-linked UPER was estimated by a 24-hour Soxhlet extraction method using toluene as the solvent. The experimental results show that all the blends show gel content greater than 90% which indicates that the prepared blends are reasonably good cross-linked. Interestingly, the blends are more crosslinked than the neat resin.
Tensile properties were evaluated by using a Shimadzu Universal Testing Machine (UTM), equipped with a 10kN load cell at a displacement rate of 5 mm/min at room temperature using Dumb-bell shaped specimen asper ASTM D638 Type V.
The flexural properties were determined using rectangular bars having a dimension of 127 mm × 12.5 mm × 4 mm on the same machine, at a speed of 5 mm/min as per ASTM D 790. For each datum, at least 5 coupons were tested.
The impact strength was determined according to ASTM D 4812-99 using a Ceast Resil Impact analyzer (Junior). A single-edge-notch, three-point-bending (SEN-TPB) test was conducted to achieve the critical stress intensity factor (toughness, KIC) of cured UPER and its blends according to ASTM D 5045 by using the rectangular specimen at a crosshead speed of 10 mm/min.
UPER blends toughened with hydroxyl end- capped polyether (PPG and PEG) exhibited only a little improvement in mechanical qualities. The blend's tensile strength increases somewhat until it reaches 2.5 phr, after which it falls. The tensile property of UPR-PPG blends improved by 10% at 2.5 phr. The tensile strength of UPR-PEG blends decreased while addition of PEG. At 2.5 phr, UPR-PPG blends showed a 22 % improvement in flexural characteristics, but UPR-PEG blends showed just a 6 % improvement. When the unsaturated polyester resin is blended with PPG (hydroxyl end- functionalized) of molar mass 2000, the resultant blend systems exhibit a 40% increase in fracture toughness properties compared to pure UPR. However, only 10% improvement was obtained on toughening with PEG. PPG - based one is the best telechelic when compared to other polyethers. The decrease in properties for PEG blended UPER resin may be due to the high propensity for crystallization of PEG in comparison to PPG. PPG has the ideal structure in the sense, its crystallization is relatively inhibited by the protruding methyl group. High crystallinity can result in brittleness. Tensile and Flexural values for UPER-PPG and UPER-PEG blends are depicted in Table 1.
Among the four-systems studied, hydroxyl, maleimide, itaconimide and nadimide end- capped polyether telechelics as toughening agents for UPER blends, itaconimide end- functionalized polypropylene glycol displayed the superlative toughening competence in terms of fracture toughness[9,10,11]. On varying the end functionality of polyethers, they exhibit diverse toughening proficiency on UPER. This difference in toughening efficiency can be due to the difference in the distribution of the polyether segments in the matrix as dictated by the copolymerization of the chain-end groups together with the unsaturation in UPER with the styrene monomer.
5.1 Quantification of Toughening Effect; Toughening Efficacy
We also calculated the efficacy factor for diverse end groups of the polyethers in imparting the change in properties. The efficacy factor of the telechelic was measured from the initial slope of the plot of the increase in fracture energy or impact strength vs. loading of the telechelics till the optimum loading. Typical plots for efficacy factor (Plots of % increase of fracture toughness or impact strength as compared with neat UPER against NPPG and IPPG) are shown in Figure 1. The Efficacy Factor (EF) is the highest for IPPG [Itaconimide end-capped PPG] loaded systems. This confirms the high efficiency of IPPG for the toughening of the UPER matrix. The efficacy factor decreased in the order itaconic> maleic> nadic> hydroxyl groups. Dependency of efficacy factor on nature of end group is revealed in Figure 2.
Figure 1.: (a) Plot of % Increase of fracture toughness against NPPG loading and (b) Plot of % Increase of Impact strength against IPPG loading for determination of efficacy factor.
Figure 2.: Dependency of efficacy factor on nature of end group.
This study showed that the polyether bearing itaconic end groups showed the best toughening effect. This was attributed to a favourable reactivity ratio of the itaconic end groups with styrene [effectively styrene-maleic CTC] that permitted the optimum distribution of the pendant polyether segments among the polyester chains. The formation of the CTC in such cases have been evidenced in a recent UV investigation[12] This distribution of polyether must be conducive for a tough matrix by way of strong dipolar interactions that act as pseudo crosslinks. Eventually, as their loading increases, the polyether segments undergo crystallization. These crystallites serve as stronger physical crosslinks, adding but to the brittleness of the matrix. Thus, by way of achieving moderate dipolar interactions, a stronger and tougher matrix results. In other words, the higher reactivity ratios of the itaconimide groups permit distribution of the polyether segments conducive for a stronger and tougher matrix. The cohesive energy is maximum for itaconimide-born polyether. In the maleimide case, the high reactivity of the maleic groups with styrene, providing a strictly alternating copolymer[13, 14] (maleic and styrene) sequence leads to an apparent accumulation of the polyether segments along the polyester chain in the matrix. This permits strong dipolar interactions among the polyether segments localizing the crosslinks with increased crosslink density but to a lesser extent than the itaconic system. The nadimide end groups were found to be readily copolymerizing (with styrene) as evident from their reactivity ratios (r1 (NI) = 0.34, r2 (St) =0.84). But this didn't favour the distribution of the polyether (bearing nadimide groups) to permit a good interaction among the polyether moieties.
Efficacy factor decreased in the order, itaconic> maleic> nadic> hydroxyl. This is in league with how they enter the polyester matrix by reaction (of end groups in combination with the unsaturation in the UPER) with the reactive solvent that dictates their sequence distribution in the copolymer chain. Overall, it is concluded that the toughening effect of the polyether was effective at a very low concentration level but it depends mainly on the distribution of the polyether in the polyester matrix. This, in turn, is dictated by their reactivity ratios with the reactive solvent. A good reactivity of the end groups with the reactive solvent may permit an even distribution of a large number of the polyether segments. But this does not necessarily ensure the formation of a strong and tough matrix. The spacing among the polyether segments is the decisive factor that can be quantified in terms of the molecular spacing of the imide groups while copolymerizing.
5.2 Distribution of Polyether Segments
The following calculations pertaining to the distribution of polyether segments in the polyester matrix explains the property variation among polyethers with different chain ends. It is assumed that the added imide reacts fully with the reactive diluent (say, styrene). From the imide's concentration and reactivity ratios, one can evaluate the concentration of this monomer that enters into the polymer chain by reaction with the styrene-maleimide CTC pair. Reactive diluent, styrene's concentration corresponds nearly 1:1 molar concerning the unsaturation.
Number of moles of reactive solvent (styrene) present in quantity, 100g UPER = 30/104.15 =0.2880 mole Concentration of maleimide born poly ether of molecular weight 2000, (Molar concentration at optimum loading) = 2.5/1216 = 0.0020 mole.
Mole ratio of polyether born maleimide and UPER born maleimide = 0.0020:0.2880 = 1:144
Now styrene and maleimide (0.2880 mole each) can be considered to exist and react in pairs as they are well known to form a charge transfer complex (CTC) between the two monomers in pairs. This pair reacts with maleimide of the polyether with equal reactivity.
For finding the copolymer composition with respect to the feed composition[15-20]
M1=1-M2=(r1m21+m1m2)/(r1m21+2m1m2+r2m22) (1)
M1 = (0.288×0.288)/ (2×0.288×0.288) = ½
The reactivity ratio, r1=r2=0 21, 22
M2 = 1-M1 = ½
For maleimide case M1=0.5 and M2 is also = 0.5
The polymer composition is always 1:1 alternating polymer irrespective of feed composition (as long as the feed contains both the monomers).
Extending the reactivity ratio concept to the pair (styrene -maleimide) and using the equation [1]
M1=M2=0.5 (2)
This permits a spacing between the two reacted polyether-born maleimide as roughly the ratios of their composition, i. e, 0.288/ 0.002= 144. This means the spacing between two polyether segments is on average corresponding to 144 reacted maleimide-styrene pairs.
The amount of the polyether-born itaconimide is 0.002 moles; reacting with styrene- maleimide (0.288 moles), therefore for best amount of approximation, we can consider a random distribution of the itaconimide across the styrene-maleimide copolymer.
Applying the same concept, we get the initially spacing of 1 monomer unit. This is refined by the reactivity ratios. From equation 1, we get
(Here, r1 (IT) = 0.78, r2 (STYR) =0.015) 23
M1 = 0.62(Itaconimide),
But, in non-cross linked UPER mix, m1=0.002/(0.288+0.002) =0.007, m2 =0.993
M2 = 0.383 both for maleimide and styrene.
The itaconimide reacts and gets intercalated in UPER cured matrix.
In fact, 0.0020 moles of itaconimide with pendant polyether, being very small when compared to 0.288 moles of styrene-maleimide pair, this macromer can also be considered as distributed evenly in the backbone of 0.288 moles of styrene (and maleimide) evenly. Therefore, the average spacing between the two itaconimide is 0.288/0.002 = 144 styrene-maleimide units. However, one can consider that the itaconimide is 1.5 times more favoured for entry into the chain [from M1 and M2]. In other words, the spacing between two adjacent itaconimide decreases by a factor of 2/3 (of 144). Applying this, we get the spacing as 96 styrene-maleimide units for this case.
Here r1 = 0.340 r2 =0.840 24
M1 = 0.404, M2 = 0.596
Applying the same reasoning and logic as in previous cases, we get a spacing of 144 × 1.5 = 216 styrene-maleimide units (arbitrary) for nadimide in UPER.
Nadimide distribution in polymer chain causes different spacing situations for the polyether- born imides. As the distance between the two imide groups increases, the toughening effect decreases. The reason is that even at the ‘optimum” concentration of the polyether, the proximity of the polyether chains is not optimum for achieving good cohesive interaction among the polymer segments.
The variations in cohesive strength and fracture propensities are tabulated in Table 2 and their trends are demonstrated in Figure 3 for various cases.
As the proximity of polyether chain increases, stronger dipolar interactions increases thereby increasing cohesive strength. Inter polyether chain interactions increases, this increases the toughening effect.
Figure 3.: Dependency of efficacy factor on polyether spacing.
UPER was toughened with maleimide/itaconimide/nadimide end-capped polyether telechelics. The mechanical and fracture resistance properties of the itaconimide end- capped polypropylene glycol blends were superior to the nadimide and maleimide end- capped versions. The toughening efficiency is quantified in terms of an efficacy factor. The efficacy factor is the highest for the itaconimide case and it leads to high toughening. The results are explained based on the possibility of dipolar interactions among the polyether segments distributed in the polyester matrix as per the reactivity ratios of the terminal imide groups (together with the unsaturation present in UPER) with the reactive solvent, typically styrene.
CONFLICTS OF INTEREST: “The authors declare no conflict of interest.”
REFERENCES
1. I. Yulianti, N. D. Putra, A. L. Dewi, and D. Paradita, Optik (2021):167305. [Google Scholar]
2. A. A. Athawale, and J. A. Pandit, Unsaturated Polyester Resins, (2019):1-42. [Google Scholar]
3. M. Messori, M. Toselli, F. Pilati, and C. Tonelli, Polymer, (2001):09877-85. [Google Scholar]
4. A. B. Cherian, B. T. Abraham, and E. T. Thachil, J. Appl. Polym. Sci. (2006):449-56. [Google Scholar]
5. S. O. Abdulghani, S. I. Salih, and K. H. Razzeg, Mater. Today: Proc. (2021) (In Press) [Google Scholar]
6. P. B. Sassmann, and O. Weichold, Ionics, (2021):3857-67. [Google Scholar]
7. P. B. Sassmann, and O. Weichold, Ionics, (2019):3971-8. [Google Scholar]
8. R. Kozera, B. Przybyszewski, K. - o3yñska, A. Boczkowska, B. Sztorch, and R. E. Przekop, Processes (2020):1635. [Google Scholar]
9. P. A. Jeemol, S. Mathew, and C. P. R. Nair, J. Polym. Res. (2020):1-4. [Google Scholar]
10. P. A. Jeemol, S. Mathew, and C. P. R. Nair, Polym. Adv. Technol. (2021):1727-41. [Google Scholar]
11. P. A. Jeemol, S. Mathew, and C. P. R. Nair, Polym. Eng. Sci. (2021):2931-44. [Google Scholar]
12. C. P. R. Nair, P. K. Manshad, A. M. Ashir, S. Athul, Eur. Polym. J. (2020):109688. [Google Scholar]
13. S. Bag, S. Ghosh, S. Paul, M. E. Khan, and P. De, Macromol. Rapid Commun. (2021):2100501. [Google Scholar]
14. K. Nishimori, M. Sawamoto, and M. Ouchi, J. Polym. Sci. A: Polym. Chem. (2019):367-75. [Google Scholar]
15. J. R. Fried, Polymer science and technology. Pearson Education (2014). [Google Scholar]
16. C. Walling, J. Am. Chem. Soc. (1949):1930. [Google Scholar]
17. F.R. Mayo, and F.M. Lewis, J. Am. Chem. Soc. (1944):66, 9, 1594-1601. [Google Scholar]
18. F.T. Wall, J. Am. Chem. Soc. (1944):2050. [Google Scholar]
19. T. Alfrey, and G. Goldfinger, J. Chem. Phys. (1944):205. [Google Scholar]
20. V.E. Meyer, and G.G. Lowry, J. of Poly Sci. Part A (1965):2843-2851. [Google Scholar]
21. J.M Barrales-Rienda, J.G De La Campa, and J.G Ramos, J. Macromol. Sci. (1977):267-86. [Google Scholar]
22. L.E Coleman Jr, and J.A. Conrady, J. Polym. Sci. (1959):241-5. [Google Scholar]
23. J. Drougas, and R.L. Guile, J. Polym. Sci. (1961):297-302. [Google Scholar]
24. P. A. Jeemol, S. Mathew, and C.P. R. Nair, Polym. Adv. Technol. (2021):1888-94. [Google Scholar]
Cite This Article
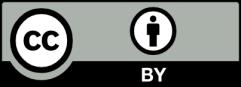
This work is licensed under a Creative Commons Attribution 4.0 International License , which permits unrestricted use, distribution, and reproduction in any medium, provided the original work is properly cited.