Open Access
ARTICLE
4-dimensional Printing of Multi-material, Multi-shape Changing Shape Memory Polymer Composites
1 Department of Automobile Engineering, PSG College of Technology, Coimbatore -641004, India.
* Corresponding Author: e-mail:
Journal of Polymer Materials 2021, 38(3-4), 327-336. https://doi.org/10.32381/JPM.2021.38.3-4.12
Abstract
In this research, a new method to fabricate multi-material, multi-shape changing polymer composites is proposed. The method aims to reduce the number of thermomechanical programming steps involved in achieving shape change in a shape memory polymer (SMP) composite structure by including the programming steps directly into the printing process. After a single step of mechanical deformation and thermal loading, the SMP fibers can be activated sequentially to control the shape change. Composite strip samples were fabricated using a Stratasys Objet 260 multimaterial printer. Two polymer inks VeroPureWhite and Agilus30 were used as primary materials. The composite strip consists of fiber layers made of digital materials (DM) namely RGD8525 and FLX9895 which are embedded in an elastomer matrix material Agilus30. The glass transition temperature of the sample materials was measured using the DMA fixture of Anton Paar MCR 102 rheometer in film tension mode and the values for the matrix, fiber 1 and fiber 2 are 4°C, 52°C and 32°C respectively. Fiber 1 and fiber 2 materials have distinct Tg values enabling the possibility of multiple shape memory effect. Uniaxial tensile tests were performed using a universal tensile testing machine, ZwickRoell Z010 to understand the stress-strain behavior of the sample materials. At 25°C, fiber 1 exhibits elastoplastic behavior and as the temperature is increased to 60°C the behavior changes to linear elastic. The Young’s modulus of the matrix material is considerably lower than the two fiber materials indicating that the fiber materials can induce shape change effect in the composite strip. The designed composite structure was able to display shape change in two different modes: bridge and cantilever. The shape change responses were achieved at 9 seconds and 7 seconds in the bridge and cantilever modes respectively which indicated that composite structures can be actuated sequentially. With the key advantages of multiple shape changes and an easy fabrication process, the direct 4D printing of shape memory polymer composite structures display vast potential in 4D printing applications including medical, automobile and aerospace applications.Keywords
Cite This Article
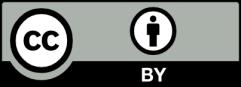
This work is licensed under a Creative Commons Attribution 4.0 International License , which permits unrestricted use, distribution, and reproduction in any medium, provided the original work is properly cited.