Open Access
REVIEW
Study of Intelligent Approaches to Identify Impact of Environmental Temperature on Ultrasonic GWs Based SHM: A Review
1 Department of Mechanical Engineering, University of Engineering and Technology Lahore, Narowal Campus, Narowal, 51600, Pakistan
2 Institute of Vibration, Shock and Noise, State Key Laboratory of Mechanical System and Vibration, Shanghai Jiao Tong University, Shanghai, 200240, China
3 Department of Mechanical Engineering, National Fertilizer Corporation (NFC), Institute of Engineering and Technology, Multan, 61000, Pakistan
4 The School of Information Science and Engineering, Xiamen University, Xiamen, 361005, China
* Corresponding Author: Saqlain Abbas. Email:
Journal on Artificial Intelligence 2023, 5, 43-56. https://doi.org/10.32604/jai.2023.040948
Received 05 April 2023; Accepted 17 August 2023; Issue published 22 September 2023
Abstract
Structural health monitoring (SHM) is considered an effective approach to analyze the efficient working of several mechanical components. For this purpose, ultrasonic guided waves can cover long-distance and assess large infrastructures in just a single test using a small number of transducers. However, the working of the SHM mechanism can be affected by some sources of variations (i.e., environmental). To improve the final results of ultrasonic guided wave inspections, it is necessary to highlight and attenuate these environmental variations. The loading parameters, temperature and humidity have been recognized as the core environmental sources of variations that affect the SHM sensing mechanism. Environmental temperature has the most significant influence on SHM results. There is still a need for extensive research to develop such a damage inspection approach that should be insensitive to environmental temperature variations. In this framework, the current research study will not only illuminate the effect of environmental temperature through different intelligent approaches but also suggest the standard mechanism to attenuate it in actual ultrasonic guided wave based SHM. Hence, the work presented in this article addresses one of the open research challenges that are the identification of the effect of environmental and operating conditions in practical applications of ultrasonic guided waves and impedance-based SHM.Keywords
The inspection of different structures such as rods, tubes, bridges, rails, aircraft, etc., is usually performed through different SHM techniques. In this regard, ultrasonic guided wave damage detection is considered an efficient approach in real-world nondestructive assessment because of the reliable sensing mechanism and better perception of the basic physics [1]. To understand the fundamental knowledge of the acoustic ultrasonic method and guided wave generation process, sufficient information was provided in the literature [2]. The work in [3] explained the excitation potential of guided waves in anisotropic materials, phased-array approach and tomography. The research in [4] described the major developments in the adhesive bond examination. The results mentioned in [5] signified the integration of ultrasonic guided waves to direct shear energy. The critical inspection results of the honeycomb structure and aircraft components have been described in [6,7]. The development of small inexpensive sensors has played an important role to cover the research gap from nondestructive testing to structural health monitoring (SHM) [8,9]. The work mentioned in [9] highlighted the concept of ultrasonic guided wave tomography. The data of [10] has identified new SHM techniques such as tomographic and phased array methods including the knowledge of sensors. Approaches for mode and frequency selections were explained in detail in [11]. Real-time guided wave phased array approaches were described in [12] and [13]. To cover the research gap from transient ultrasonic guided wave analysis to modal vibration approaches, a new ultrasonic vibration technique was introduced. The practical application of guided waves for ice detection and de-icing in aircraft was unique in all aspects [14–16]. The work presented in [17] demonstrated the exact circumferential defect-locating skill of the ultrasonic guided-wave phased-array focusing method [17].
Piezoelectric materials are widely used for different functions in engineering infrastructures. These materials are effective for high potential safety and maintenance in case of initiation of cracks due to several reasons such as fatigue/corrosion [18–26]. Piezoelectric materials were employed for the monitoring of mechanical structures such as concretes, aircraft and photovoltaic solar panels. Further, the implementation of piezoelectric-based SHM has helped to introduce the concept of innovation in different industries. However, there are still some problems with the execution of current non-destructive research tools in real structures. To achieve the most efficient SHM systems, the inspection procedure requires a single piezoelectric for exciting and detecting the host structure. In this regard, the research community is fully committed to working on the experimental parameters of the ultrasonic guided wave inspection and electromechanical impedance (EMI) technique. EMI technique can detect structural interference, sensor/actuator irregularities, and delamination. To avoid the malfunction of the device, the sensor’s self-monitoring is significant because it can affect the inspection procedure. Hence, the SHM research community is also concentrating on sensor self-diagnosis. Fig. 1 highlights the recent trends in piezoelectric research and its applications in engineering structures. It is expected to achieve more progress and growth soon in this field. These materials have developed new potentials to deal with different engineering concerns [27].
Figure 1: Trends in piezoelectric research
Henceforth, for the inspection of both surface and subsurface defects, ultrasound-guided wave detection is recognized as suitable. It can also identify the defect in depth by using “ultrasonic” (high-frequency) sound energy. The most common defects inspected and measured by ultrasonic guided waves are voids, disbands, fatigue, delamination, surface discontinuities and matrix cracking in rotor blades [28].
The ultimate purpose of this research is to endorse the idea that ultrasonic guided wave inspection has great potential in structural health monitoring (SHM) of mechanical structures to maintain their optimal and long-term performance. This research work deals with one of the open research challenges that are the effect of environmental and operating conditions in practical applications of ultrasonic guided waves and impedance-based SHM.
2 Achievements for Guided-Wave (GW) Based SHM
Fig. 2 shows the process diagram of SHM. Most of the researchers working in the SHM field deal with some parts of the process [29].
Figure 2: Structural health monitoring (SHM) process
The SHM is an advanced system developed from non-destructive testing (NDT) and equipped with sensors and intelligent algorithms to monitor a health condition. These algorithms are implemented through different models such as the Statistical model to identify and quantify the severity of the damage. Fig. 3 illustrates the two main categories of these algorithms [27]. In general, these algorithms examine the statistical distributions of the extracted features to increase the reliability of the damage detection process.
Figure 3: Algorithms classification for Statistical model development for SHM
There are several achievements for guided-wave based SHM such as water loading effects, illustration and selection of optimal mode and frequency, respectively and crack detection sensitivities, etc. Some significant achievements in composite materials, pipe inspections and aircraft applications are listed in Table 1 [17].
3 Challenges for Guided-Wave and Impedance Based SHM
Although their many benefits, the practical application of ultrasonic guided waves for SHM is still relatively limited [30–35]. The significant challenges can be expressed in three ways: (a) Multi-path reflections, (b) Multiple modes, and (c) Sensitivity to environmental and operational conditions (EOCs) [36–40]. This research work deals with the difficulties and challenges to applying SHM techniques (ultrasonic guide wave inspection and EMI) in actual inspections, which is variations in environmental and operating conditions (EOCs).
Utilizing small number of sensors and intelligent algorithms, ultrasonic guided waves can cover a long-distance and perform the accurate assessment of complex and large structures [41–43]. Conversely, the working of the SHM mechanism can be affected by some environmental resources [44]. It is necessary to identify and attenuate these environmental variations. The loading parameters, temperature and humidity have been recognized as the core environmental sources of variations that affect the SHM sensing mechanism. Environmental temperature has the most significant influence on SHM results. There is still a need for extensive research to develop a damage inspection technique that can attenuate the impact of environmental temperature variations. Elastic properties of inspected material are greatly influenced by temperature may cause unwanted fluctuations in the amplitude of propagating wave signals [45]. Group and phase velocities of ultrasonic guided waves including modulation envelope are demonstrated in Fig. 4.
Figure 4: Group and phase velocities of GWs
The impedance-based SHM technique is certainly capable to employ it in complex structures to classify initial crack growth, but certain specific features have limited its reliability in real-life applications. In maximum situations, the specimen that is being inspected is constantly experiencing the numerous variable environmental parameters [46].
In the last two decades, several research scholars have worked on data analysis methods to attenuate the effect of some EOCs and improve the application of ultrasonic guided waves and impedance-based damage detection approaches [47–57]. Statistical and signal processing methods have revealed reasonable efficiency to evaluate damage sensitive parameters that are less sensitive to the specific EOCs. Still, developments are required to deal with the challenges such as the complex arrangement of sensor and actuator networks, requisite comprehensive knowledge about atomic configuration, case-specific tunning considerations, and linear disintegration of multi-modal signals whose bases might be related to the aspect of non-linearly.
3.1 The Supervised Approach (Sparse Discriminant (SD) Method) for Damage Detection and Its Thermal Sensitivity
A supervised approach is presented to identify a sparse subset of the ultrasonic guided-wave signals that have optimum crack data for inspection determinations. Preferably, if the entries dispersed from abnormality are recovered from the measured signals, they might be utilized for damage recognition. But, the research has revealed that fluctuation of EOCs disturbs the dispersed signals so that the crack data is intimidated by the effect of EOCs. The implementation of the sparse discriminant technique for constant operational damage inspection of a pipeline is illustrated in Fig. 5. The procedure involves the original training stage and the constant monitoring stage [58].
Figure 5: Inspection of pipelines through training and monitoring stage
3.2 The Unsupervised Approach (Sparse Energy (SE) Method) for Damage Detection and Its Thermal Sensitivity
The SD technique detailed in Subsection 3.1 deals with the limitations resulting from the complicated nature of ultrasonic guided waves and their sensitivity to EOCs distinctions. Its efficiency and the percentage detection accuracy being a supervised approach may be influenced by the alterations between training and test modules due to variation in EOCs, crack characteristics and location. The results of the SD technique propose that simple twofold labelled training observations of both damaged and undamaged cases attained under a partial range of EOCs are adequate for optimum execution of the SD technique. Conversely, the practical applications of the SD approach are inadequate to the circumstances where locating the training information from any pipe structure with irregularity is promising and practical. Furthermore, it is valuable to decrease the number of training values that influence the efficient working of a detection approach. Hence, to resolve these problems, an unsupervised sparse energy (SE) approach is industrialized for the crack identification in pipes; definitely, it deals efficiently with the complex nature of ultrasonic guided waves and their sensitivity to EOC variants [59]. This unsupervised approach aims to identify a subset of the ultrasonic guided-wave modules that includes the bulk of the signal’s energy. The ideal solution will be the subset having minimum sensitivity to EOC variants. The projected SHM structure using the SE approach for the constant crack inspection of the pipeline is illustrated in Fig. 6 [59].
Figure 6: Application of the SE approach for the inspection of pipelines
3.3 Mode Decomposition (MD) Method to Illuminate the Effect of Temperature Variations on the Group Velocity of Guided Waves
Numerous studies have been conducted to present a technique to calculate the influence of environmental temperature on the measured signal. In this framework, the two methods named optimal baseline selection (OBS) and baseline signal stretch (BSS) is established by utilizing the basic concept of signal processing [60,61]. The procedure of OBS includes many standard entries measured over a range of temperatures while the BSS technique includes the idea of extending the signal and varying its amplitude. It was determined that the permutation of OBS and BSS is a vigorous approach to compensate for the effect of temperature. Though significant research has been done on this subject, there are few efforts existing in the literature to compensate for the effect of temperature on composite materials. In certain studies, a linear dependence of composite material properties is anticipated to change them by varying the temperature [62]. The alteration in the phase of the measured module is generally a magnitude of varying the velocity of the propagating wave. The variation occurs in both phase and group velocities of propagating wave signal due to thermal expansion in the examined material. An experimental scheme shown in Fig. 7 was developed in [62] to investigate the influence of temperature deviations on ultrasonic guided waves propagating along with a glass-fibre composite specimen. Later, it is confirmed that by implementing mode decomposition and employing two stretch factors, it is possible to modify the results by improving the BSS method.
Figure 7: The schematic view of experimental setup [62]
3.4 Effect of Temperature Variations on the Natural Frequency of the Structure
The variations in environmental temperature have a significant impact on the natural frequency of inspected specimens and it changes the damage detections outcomes. A major decrease in the natural frequency of the inspected specimen is noticed with temperature because of variations in material properties, especially, the modulus of elasticity. The process of damage propagation is also influenced by this deviation in natural frequency due to the extreme normalized amplitude of stresses generated in the inspected structure. Thus, it affects the arrival time of the propagating signal because of stretching and shorting of the route between the transducers which disturbs the final damage assessment [63]. The whole phenomenon of variation in natural frequency of structure with temperature can be clearly observed in Fig. 8.
Figure 8: Variation in natural frequency of structure with temperature [63]
To analyze the behaviour of transmission and reflection signal under varying temperature environment, the laboratory test setup is developed and illustrated in Fig. 9 [64].
Figure 9: Experiment test setup
According to the attained time-domain and envelope curves, the amplitude and group velocities of the corresponding first wave packet of each received signal are estimated and demonstrated in Figs. 10 and 11, respectively [64].
Figure 10: The amplitude of measured signals at variable temperature and excitation frequency: (a) 100 kHz; (b) 175 kHz
Figure 11: The group velocity of measured signals at variable temperature and excitation frequency: (a) 100 kHz; (b) 175 kHz
Structural health monitoring of any mechanical structure is essential for its optimal and persistent performance. However, the working of structural health monitoring mechanism can be affected by some sources of variations (i.e., environmental). To improve the final results of ultrasonic guided wave-based structural health monitoring, it is necessary to highlight and attenuate these environmental variations. The loading parameters, temperature and humidity have been measured as the core environmental sources of variations that affect the structural health monitoring sensing mechanism. Environmental temperature has the most significant influence on structural health monitoring results. Hence, this research work deals with one of the open research challenges that are the identification of the effect of environmental and operating conditions in practical applications of ultrasonic guided waves and impedance-based structural health monitoring. The work highlights the identification of a sparse subset of the ultrasonic guided-wave signals that have optimum crack data for inspection purposes with less thermal sensitivity. Sparse discriminant and sparse energy techniques are considered in detail in terms of ideal damage measurement. The results of the sparse discriminant technique propose that simple twofold labelled training observations of both damaged and undamaged cases attained under a partial range of environmental and operating conditins are adequate for optimum execution of the sparse discriminant technique. Conversely, the practical applications of the sparse discriminant approach are inadequate to the circumstances where locating the training information from any pipe structure with irregularity is promising and practical. Furthermore, it is valuable to decrease the number of training values that influence the efficient working of a detection approach. Hence, to resolve these problems, an unsupervised sparse energy approach is industrialized for crack identification in cylindrical structures; definitely, it deals efficiently with the complex nature of ultrasonic guided waves and their sensitivity to environmental and operating conditions variants The mode decomposition method has revealed that the amplitude of the propagating wave signal reduces by decreasing the temperature because of sufficient effect of temperature deviation on the piezoelectric transducers. Furthermore, the presence of time lag in the measured signal and its variations due to dropping the temperature verify that the group velocity of propagating wave rises within the defined temperature range. The variations in environmental temperature have also a significant impact on the natural frequency of inspected specimens and it changes the damage detections outcomes. A major decrease in the natural frequency of the inspected specimen is noticed with temperature because of variations in material properties, especially, the modulus of elasticity. The process of damage propagation is also influenced by this deviation in natural frequency due to the extreme normalized amplitude of stresses generated in the inspected structure. Thus, it affects the arrival time of the propagating signal because of stretching and shorting of the route between the transducers which disturbs the final damage assessment. Hence, it is endorsed to consider and implement the outcomes of current research in actual ultrasonic guided wave inspection to provide an ideal solution for thermal attenuation and precision in structural health monitoring results.
Acknowledgement: The authors would like to gratefully acknowledge the support received from the Shanghai Jiao Tong University China, University of Engineering & Technology Lahore, and National Fertilizer Cooperation Institute of Engineering and Technology, Multan (NFC IET, Multan, Pakistan) to accomplish this research work.
Funding Statement: The authors received no specific funding for this study.
Author Contributions: The authors confirm contribution to the paper as follows: study conception and design: S.A, Z.A; data collection: S.A, Y.Z; analysis and interpretation of results: S.A, Z.A, X.T; draft manuscript preparation: S.A, X.T, Y.Z. All authors reviewed the results and approved the final version of the manuscript.
Availability of Data and Materials: Available on demand.
Conflicts of Interest: The authors declare that they have no conflicts of interest to report regarding the present study.
References
1. J. L. Rose, “Ultrasonic guided waves in structural health monitoring,” in Key Engineering Materials, vol. 270, Trans Tech Publications Ltd., Switzerland, pp. 14–21, 2004. [Google Scholar]
2. J. L. Rose, J. J. Ditri and A. Pilarski, “Wave mechanics in acousto-ultrasonic nondestructive evaluation,” Journal of Acoustic Emission, vol. 12, pp. 23–26, 1994. [Google Scholar]
3. J. J. Ditri and J. L. Rose, “Excitation of guided waves in generally anisotropic layers using finite sources,” ASME Journal of Applied Mechanics, vol. 61, no. 2, pp. 330–338, 1994. [Google Scholar]
4. A. Pilarski and J. L. Rose, “A transverse-wave ultrasonic oblique incidence technique for interfacial weakness detection in adhesive bonds,” Journal of Applied Physics, vol. 63, no. 2, pp. 300–307, 1988. [Google Scholar]
5. J. L. Rose, K. M. Rajana and M. K. T. Hansch, “Ultrasonic guided waves for NDE of adhesively bonded structures,” Journal of Adhesion, vol. 50, no. 1, pp. 71–82, 1995. [Google Scholar]
6. T. R. Hay, W. Luo, J. L. Rose and T. Hayashi, “Rapid inspection of composite skin-honeycomb core structures with ultrasonic guided waves,” Journal of Composite Materials, vol. 37, no. 10, pp. 929–939, 2003. [Google Scholar]
7. J. L. Rose and L. Soley, “Ultrasonic guided waves for anomaly detection in aircraft components,” Materials Evaluation, vol. 50, pp. 1080–1086, 2000. [Google Scholar]
8. X. Zhao, H. Gao, G. Zhang, B. Ayhan, F. Yan et al., “Active health monitoring of an aircraft wing with embedded piezoelectric sensor/actuator network: I. Defect detection, localization and growth monitoring,” Smart Materials and Structures, vol. 16, pp. 1208–1217, 2007. [Google Scholar]
9. H. Gao, Y. Shi and J. L. Rose, “Guided wave tomography on an aircraft wing with leave in place sensors,” in AIP Conf. Proc., Colorado, USA, vol. 760, pp. 1788–1794, 2005. [Google Scholar]
10. J. L. Rose, F. Yan and H. Gao, “New techniques in composite testing,” Materials Evaluation, vol. 65, no. 8, pp. 801–805, 2007. [Google Scholar]
11. J. L. Rose, “The upcoming revolution in ultrasonic guided waves,” in Nondestructive Characterization for Composite Materials, Aerospace Engineering, Civil Infrastructure, and Homeland Security, vol. 7983, pp. 21–50, 2011. https://doi.org/10.1117/12.897025 [Google Scholar] [CrossRef]
12. F. Yan and J. L. Rose, “Guided wave phased array beam steering in composite plates,” in Health Monitoring of Structural and Biological Systems, vol. 6532, pp. 142–150, 2007. https://doi.org/10.1117/12.716109 [Google Scholar] [CrossRef]
13. F. Yan and J. L. Rose, “Time delay comb transducers for aircraft inspection,” The Aeronautical Journal of the Royal Aeronautical Society, vol. 113, no. 1144, pp. 417–427, 2009. [Google Scholar]
14. J. L. Rose, F. Yan and Y. Zhu, “Ultrasonic guided wave modal analysis technique (UMAT) for defect reflection,” in Structural Dynamics, Volume 3: Proc. of the 28th IMAC, Springer: New York, USA, pp. 831–838, 2011. https://doi.org/10.1007/978-1-4419-9834-7_73 [Google Scholar] [CrossRef]
15. H. Gao and J. L. Rose, “Ice detection and classification on an aircraft wing with ultrasonic shear horizontal guided waves,” IEEE Transactions on Ultrasonics, Ferroelectrics, and Frequency Control, vol. 56, no. 2, pp. 334–344, 2009. [Google Scholar] [PubMed]
16. J. L. Rose, “Successes and challenges for ultrasonic testing in NDT and SHM,” Materials Evaluation, vol. 68, no. 5, pp. 494–500, 2010. [Google Scholar]
17. A. R. Diogo, B. Moreira, C. A. Gouveia and J. M. R. Tavares, “A review of signal processing techniques for ultrasonic guided wave testing,” Metals, vol. 12, no. 6, pp. 936, 2022. [Google Scholar]
18. F. Saraiva, “Development of press forming techniques for thermoplastic composites investigation of a multiple step forming approach,” Master’s Thesis, Delft University of Technology, Delft, The Netherlands, 2017. [Google Scholar]
19. D. Sun and D. Wang, “Distributed piezoelectric element method for vibration control of smart plates,” AIAA Journal, vol. 37, no. 11, pp. 1459–1463, 1999. [Google Scholar]
20. Q. Wang and S. T. Quek, “Repair of delaminated beams via piezoelectric patches,” Smart Materials and Structures, vol. 13, no. 5, pp. 1222–1229, 2004. [Google Scholar]
21. Q. Wang, W. H. Duan and S. T. Quek, “Repair of notched beam under dynamic load using piezoelectric patch,” International Journal of Mechanical Sciences, vol. 46, no. 10, pp. 1517–1533, 2004. [Google Scholar]
22. A. Alaimo, A. Milazzo and C. Orlando, “Boundary elements analysis of adhesively bonded piezoelectric active repair,” Engineering Fracture Mechanics, vol. 76, no. 4, pp. 500–511, 2009. [Google Scholar]
23. A. Alaimo, A. Milazzo and C. Orlando, “Numerical analysis of a piezoelectric structural health monitoring system for composite flange-skin delamination detection,” Composite Structures, vol. 100, no. 2, pp. 343–355, 2013. [Google Scholar]
24. S. Kapuria, M. Y. Yasin and P. Hagedorn, “Active vibration control of piezolaminated composite plates considering strong electric field nonlinearity,” AIAA Journal, vol. 53, no. 3, pp. 603–616, 2015. [Google Scholar]
25. C. Zhang, S. S. Nanthakumar, T. Lahmer and T. Rabczuk, “Multiple cracks identification for piezoelectric structures,” International Journal of Fracture, vol. 206, no. 2, pp. 151–169, 2017. [Google Scholar]
26. P. Krishna, S. Mallik and D. S. Rao, “Vibration control on composite beams with multiple piezoelectric patches using finite element analysis,” International Research Journal of Engineering and Technology, vol. 4, pp. 906–911, 2017. [Google Scholar]
27. A. Aabid, B. Parveez, M. A. Raheman, Y. E. Ibrahim, A. Anjum et al., “A review of piezoelectric material-based structural control and health monitoring techniques for engineering structures: Challenges and opportunities,” Actuators, vol. 10, no. 5, pp. 101, 2021. [Google Scholar]
28. S. Abbas, F. Li and J. Qiu, “A review on SHM techniques and current challenges for characteristic investigation of damage in composite material components of aviation industry,” Materials Performance and Characterization, vol. 7, no. 1, pp. 224–258, 2018. [Google Scholar]
29. C. R. Farrar and K. Worden, “An introduction to structural health monitoring,” Philosophical Transactions of the Royal Society A: Mathematical, Physical and Engineering Sciences, vol. 365, no. 1851, pp. 303–315, 2007. [Google Scholar]
30. S. Abbas, F. Li and X. Tu, “Model-based ultrasonic guided wave inspection to identify and attenuate the effect of environmental temperature in structural health monitoring,” Structural Health Monitoring, 2019. https://doi.org/10.12783/shm2019/32308 [Google Scholar] [CrossRef]
31. J. Qiu, F. Li, S. Abbas and Y. Zhu, “A baseline-free damage detection approach based on distance compensation of guided waves,” Journal of Low Frequency Noise, Vibration and Active Control, vol. 38, no. 3–4, pp. 1132–1148, 2018. [Google Scholar]
32. R. Guan, Y. Lu, W. Duan and X. Wang, “Guided waves for damage identification in pipeline structures: A review,” Structural Control and Health Monitoring, vol. 24, no. 11, pp. e2007, 2017. [Google Scholar]
33. M. Mitra and S. Gopalakrishnan, “Guided wave based structural health monitoring: A review,” Smart Materials and Structures, vol. 25, no. 5, pp. 053001, 2016. [Google Scholar]
34. H. R. Kess and D. E. Adams, “Investigation of operational and environmental variability effects on damage detection algorithms in a woven composite plate,” Mechanical Systems and Signal Processing, vol. 21, no. 6, pp. 2394–2405, 2007. [Google Scholar]
35. H. Sohn, “Effects of environmental and operational variability on structural health monitoring,” Philosophical Transactions of the Royal Society, vol. 365, no. 1851, pp. 539–560, 2007. [Google Scholar]
36. F. Chen and P. D. Wilcox, “The effect of load on guided wave propagation,” Ultrasonics, vol. 47, no. 1–4, pp. 111–122, 2007. [Google Scholar] [PubMed]
37. Y. Lu and J. E. Michaels, “Feature extraction and sensor fusion for ultrasonic structural health monitoring under changing environmental conditions,” IEEE Sensors Journal, vol. 9, no. 11, pp. 1462–1471, 2009. [Google Scholar]
38. J. Rose, “NDT solution: Guided wave testing of water loaded structures,” Materials Evaluation, vol. 61, no. 1, pp. 23–24, 2003. [Google Scholar]
39. B. Lee, G. Manson and W. Staszewski, “Environmental effects on Lamb wave responses from piezoceramic sensors,” Materials Science Forum, vol. 440, pp. 195–202, 2003. https://doi.org/10.4028/www.scientific.net/MSF.440-441.195 [Google Scholar] [CrossRef]
40. R. L. Weaver and O. I. Lobkis, “Temperature dependence of diffuse field phase,” Ultrasonics, vol. 38, no. 1–8, pp. 491–494, 2000. [Google Scholar] [PubMed]
41. M. Schafer, “The effect of experimental conditions on acousto-ultrasonic reproducibility,” in IEEE Symp. Ultrasonics, San Juan, PR, USA, pp. 771–778, 2000. [Google Scholar]
42. G. Konstantinidis, B. W. Drinkwater and P. D. Wilcox, “The temperature stability of guided wave structural health monitoring systems,” Smart Materials and Structures, vol. 15, no. 4, pp. 967, 2006. [Google Scholar]
43. S. Mariani, S. Heinlein and P. Cawley, “Compensation for temperature-dependent phase and velocity of guided wave signals in baseline subtraction for structural health monitoring,” Structural Health Monitoring, vol. 19, no. 1, pp. 26–47, 2020. [Google Scholar]
44. T. Clarke, F. Simonetti and P. Cawley, “Guided wave health monitoring of complex structures by sparse array systems: Influence of temperature changes on performance,” Journal of Sound and Vibration, vol. 329, no. 12, pp. 2306–2322, 2010. [Google Scholar]
45. M. Clough, M. Fleming and S. Dixon, “Circumferential guided wave EMAT system for pipeline screening using shear horizontal ultrasound,” NDT & E International, vol. 86, pp. 20–27, 2017. [Google Scholar]
46. S. Abbas, F. Li, Z. Abbas, T. Ur, X. Tu et al., “Experimental study of effect of temperature variations on the impedance signature of PZT sensors for fatigue crack detection,” Sound & Vibration, vol. 55, no. 1, pp. 1–18, 2021. [Google Scholar]
47. M. Eybpoosh, M. Berges and H. Y. Noh, “Sparse representation of ultrasonic guided-waves for robust damage detection in pipelines under varying environmental and operational conditions,” Structural Control and Health Monitoring, vol. 23, no. 2, pp. 369–391, 2016. [Google Scholar]
48. R. Gorgin, Y. Luo and Z. Wu, “Environmental and operational conditions effects on Lamb wave based structural health monitoring systems: A review,” Ultrasonics, vol. 105, no. 2087, pp. 106114, 2020. [Google Scholar] [PubMed]
49. H. Sun, J. Yi, Y. Xu, Y. Wang and X. Qing, “Identification and compensation technique of non-uniform temperature field for Lamb wave-and multiple sensors-based damage detection,” Sensors, vol. 19, no. 13, pp. 2930, 2019. [Google Scholar] [PubMed]
50. M. S. Salmanpour, Z. S. Khodaei and M. H. Aliabadi, “Guided wave temperature correction methods in structural health monitoring,” Journal of Intelligent Material Systems and Structures, vol. 28, no. 5, pp. 604–618, 2017. [Google Scholar]
51. Z. Wang, Y. Zhong, J. Zhou, C. Li and L. Zhong, “Environmental effects on piezoelectric sensors array signals and a compensated damage imaging method,” Materials, vol. 14, no. 22, pp. 6742, 2021. [Google Scholar] [PubMed]
52. S. Ahmed and F. Kopsaftopoulos, “Stochastic identification of guided wave propagation under ambient temperature via non-stationary time series models,” Sensors, vol. 21, no. 16, pp. 5672, 2021. [Google Scholar] [PubMed]
53. F. Du, S. Wu, C. Xu, Z. Yang and Z. Su, “Electromechanical impedance temperature compensation and bolt loosening monitoring based on modified Unet and multitask learning,” IEEE Sensors Journal, vol. 23, no. 5, pp. 4556–4567, 2023. [Google Scholar]
54. M. Djemana, M. Hrairi and N. H. M. Yatim, “Improving electromechanical impedance damage detection under varying temperature,” Journal of Advanced Research in Fluid Mechanics and Thermal Sciences, vol. 92, no. 1, pp. 123–133, 2022. [Google Scholar]
55. A. J. Croxford, J. Moll, P. D. Wilcox and J. E. Michaels, “Efficient temperature compensation strategies for guided wave structural health monitoring,” Ultrasonics, vol. 50, no. 4–5, pp. 517–528, 2010. [Google Scholar] [PubMed]
56. R. A. Antunes, N. E. Cortez, B. M. Gianesini and J. V. Filho, “Modeling, simulation, experimentation, and compensation of temperature effect in impedance-based SHM systems applied to steel pipes,” Sensors, vol. 19, no. 12, pp. 2802, 2019. [Google Scholar] [PubMed]
57. Z. Dworakowski, L. Ambrozinski and T. Stepinski, “Multi-stage temperature compensation method for Lamb wave measurements,” Journal of Sound and Vibration, vol. 382, no. 2, pp. 328–339, 2016. [Google Scholar]
58. C. Fendzi, M. Rebillat, N. Mechbal, M. Guskov and G. Coffignal, “A data-driven temperature compensation approach for structural health monitoring using lamb waves,” Structural Health Monitoring, vol. 15, no. 5, pp. 525–540, 2016. [Google Scholar]
59. M. E. Poosh, “A data-driven framework based on sparse representation of ultrasonic guided-waves for online damage detection of pipelines,” Doctoral Dissertation, Carnegie Mellon University, Pittsburgh, USA, 2015. [Google Scholar]
60. Y. Lu and J. E. Michaels, “A methodology for structural health monitoring with diffuse ultrasonic waves in the presence of temperature variations,” Ultrasonics, vol. 43, no. 9, pp. 717–731, 2005. [Google Scholar] [PubMed]
61. A. J. Croxford, P. D. Wilcox, G. Konstantinidis and B. W. Drinkwater, “Strategies for overcoming the effect of temperature on guided wave structural health monitoring,” in Health Monitoring of Structural and Biological Systems 2007, vol. 6532, pp. 590–599, 2007. https://doi.org/10.1117/12.719435 [Google Scholar] [CrossRef]
62. S. Shoja, V. Berbyuk and A. Boström, “Effects of temperature variations on guided waves propagating in composite structures,” in Smart Materials and Nondestructive Evaluation for Energy Systems. vol. 9806, pp. 980605, 2016. https://doi.org/10.1117/12.2218791 [Google Scholar] [CrossRef]
63. S. Abbas, F. Li, J. Qiu, Y. Zhu and X. Tu, “Optimization of ultrasonic guided wave inspection in structural health monitoring based on thermal sensitivity evaluation,” Journal of Low Frequency Noise, Vibration and Active Control, vol. 40, no. 1, pp. 601–622, 2021. [Google Scholar]
64. S. Abbas, F. Li, Y. Zhu and X. Tu, “Experimental investigation of impact of environmental temperature and optimal baseline for thermal attenuation in structural health monitoring based on ultrasonic guided waves,” Wave Motion, vol. 93, no. 11, pp. 102474, 2020. [Google Scholar]
Cite This Article
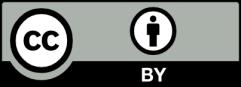
This work is licensed under a Creative Commons Attribution 4.0 International License , which permits unrestricted use, distribution, and reproduction in any medium, provided the original work is properly cited.