Open Access
ABSTRACT
Transient hydroplaning simulation of automotive tires using the fluid-structure interaction finite element method
Corresponding author. E-mail: stjenq@mail.ncku.edu.tw, Fax: +886-6-2083641.
Department of Aeronautics & Astronautics, National Cheng Kung University, Tainan, 70101,Taiwan, R.O.C.
The International Conference on Computational & Experimental Engineering and Sciences 2009, 9(4), 263-264. https://doi.org/10.3970/icces.2009.009.263
Abstract
The purpose of this work is to study the transient hydroplaning behavior of inflated pneumatic 195/65R15 radial tires with various tread patterns and the tires were loaded with a quarter car weight. The tires were analyzed numerically to roll over a water film with a thickness of 5 mm, 10 mm and 15 mm on top of a flat-road pavement. Current tire structure contains the outer rubber tread and the inner advanced reinforcing composite layers. The Mooney-Rivlin constitutive law and the classical laminated theory (CLT) were used to describe the behavior of the large-deformable rubber tread material and reinforcing composite layers, respectively. The complex tire hydroplaning phenomenon was solved by the commercial LS-DYNA explicit solver. Both Arbitrary Lagrangian {\&} Eulerian (ALE) and Eulerian formulations were adopted to depict the fluid behavior and the fluid-structure interaction (FSI) in LS-DYNA simulation. Dynamic contact forces between the tread pattern and road surface were also examined numerically by using the LS-DYNA. The normal contact force and hydroplaning velocity of the tire with smooth tread pattern were simulated and computed results were compared with the corresponding numerical and test results reported by Okano, et al. (2001, \textit {Tire Science {\&} Technology, TSTCA}) The tire finite element models with three tread patterns, i.e. the smooth tread pattern, the 9mm and 18mm main groove width longitudinal grooved tread patterns, were constructed in order to perform hydroplaning analysis. Current tire was initially inflated to 200 kPa and then loaded with a vertical quarter car weight of 4000N within a period of time in the numerical simulations. Tire was subsequently accelerated from the rest on a flat pavement to a speed of 120 km/hr and then run over the water layer with a specific water films thickness of height for fluid structure interaction analysis. The normal contact force between the tread pattern and road surface for the tires with smooth and longitudinal-grooved tread pattern interacted with the water film were obtained and reported. Notice that the normal contact force of tire with smooth tread pattern rolling over dry and flat roadway was also calculated and compared numerical results edited by Nakajima et al. (2000, \textit {Int. J. Auto. Tech.}) Good agreement between each other was reported.Keywords
Cite This Article
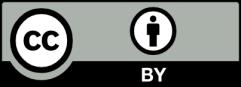
This work is licensed under a Creative Commons Attribution 4.0 International License , which permits unrestricted use, distribution, and reproduction in any medium, provided the original work is properly cited.