Open Access
ABSTRACT
Effect of chamfered brake pad patterns & lining friction coefficients on the vibration squeal response for automotive disc brake system
Department of Aeronautics & Astronautics, National Cheng Kung University, Tainan, Taiwan,R.O.C.
Corresponding author, Professor, Email: stjenq@mail.ncku.edu.tw, Fax: (Taiwan)-6-208-3641.
Dassault Systemes Simulia Central, Cincinnati, Ohio, USA
Department of Electronic engineering, Kao Yuan University, Kaohsiung County, Taiwan, R.O.C.
Aeronautical Systems Research Division, Chung-Shan Institute of Science & Technology(CSIST), Taichung, Taiwan, R.O.C.
The International Conference on Computational & Experimental Engineering and Sciences 2009, 9(4), 245-246. https://doi.org/10.3970/icces.2009.009.245
Abstract
The purpose of the present work is to study the disc brake squeal problem for passenger cars in order to reduce the instable high frequency squeal modes. The ABAQUS/Standard implicit method was used to perform dynamic contact vibration analysis of the current disc brake finite element model. The disc brake system studied here contains the caliper, bracket, brake disc, and brake pad. Notice that brake pad in general contains both brake lining and brake shoe. The brake pad with a specific chamfer pattern and the brake disc with a series of cooling ribs for ventilation were numerically constructed in the disc brake finite element model. Effect of the various chamfered brake pad patterns on the unstable vibration frequencies is studied and the unstable vibration may result in the brake squeal phenomenon. A 303 mm diameter brake disc with a rotational speed of 2.5 rad/s was numerically analyzed when the brake pad was subjected to a uniform hydraulic pressure of 1.379 MPa (i.e. 200 psi). The complex eigenvalue method was adopted to extract the corresponding unstable high frequency squeal modes for the present disc brake system which contains the brake pads with a series of different combination of the chamfer patterns and brake lining dry friction coefficients. In the current simulations, the brake lining friction coefficients were studied in the range from 0.1 to 0.5 and three types of chamfer patterns, i.e. the 21 mm parallel chamfers, a center slot and the top and bottom center V-chamfers, were also examined. The finite element simulated result of the unstable squeal frequencies and the corresponding unstable modes are presented and then compared with the dynamometer test results.Keywords
Cite This Article
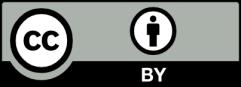
This work is licensed under a Creative Commons Attribution 4.0 International License , which permits unrestricted use, distribution, and reproduction in any medium, provided the original work is properly cited.