Open Access
ABSTRACT
Interaction Effect Analysis of Two Surface Cracks using S-version FEM
Tokyo University of Science, Japan
Tokyo University of Science Suwa, Japan
Graduate School, Tokyo University of Science, Japan
Northwestern Polytechnical University, China
The International Conference on Computational & Experimental Engineering and Sciences 2009, 9(4), 222-224. https://doi.org/10.3970/icces.2009.009.222
Abstract
Prediction of fatigue crack growth in mechanical component is one of the most important problems to prevent catastrophic fracture accident. FEM is generally used for this purpose, but as crack shape changes during growing process, it is necessary to re-mesh for new crack shape. It is time consuming and is very difficult especially for 3-d. problem.In this study, S-version FEM[1][2] is employed to solve this problem, and fully automatic crack growth simulation system is made by combining with automatic mesh generationsystem. In the 3-d. field, crack tip stressconditionbecomes under mixed mode condition, and three stress intensity factor, KI,KII and KIII are evaluated by S-FEM. Using crack growth rate criterion and crack growth path criterion, proposed by Richard et al.[3], new crack configurationis obtained. In S-FEM, crack exists in local region, and it is necessary to re-mesh the local mesh for this new crack configuration. As connectivity condition between local mesh and global mesh is unnecessary, re-meshing of local mesh is easy. After getting new local mesh, S-FEM is used to solve the stress field. By repeating these processes, crack growth simulation could be done fully automatically.
In this study, several 3-d. fatigue crack problems are solved using this system. At first, single surface crack subjected by mixed mode loading is solved. It is verified that crack growth occurs under pure mode I condition, and KII and KIII values vanish by fatigue crack growth. It is also shown that distribution of KI value along crack front becomes nearly constant by the crack growth.
Then 2 surface cracks problem is solved in several cases by changing distances between two crack tips. Fig. 1 and Fig.2 show examples of 2 surface cracks. Crack shapes change by the interaction between 2 cracks. It is shown that the distributions of Stress Intensity Factors along crack front are largely affected by the initial crack tip distances. Results are compared with Maintenance code for Nuclear Power Plant by JSME[4]. The coalescence condition of two cracks is studied and it is verified that JSME code gives conservative evaluation.
Cite This Article
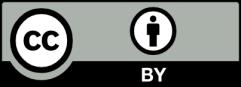
This work is licensed under a Creative Commons Attribution 4.0 International License , which permits unrestricted use, distribution, and reproduction in any medium, provided the original work is properly cited.