Open Access
ABSTRACT
Computational Environment for the Multiscale, Multi-Physics Resin Transfer Molding Process
Team Member, Comp. Eng. Light-Weight Structures, U.S. Army Research Laboratory, APG, MD, USA
Team Leader, Comp. Eng. Light-Weight Structures, U.S. Army Research Laboratory, APG, MD, USA
The International Conference on Computational & Experimental Engineering and Sciences 2008, 7(1), 13-18. https://doi.org/10.3970/icces.2008.007.013
Abstract
The capability to predict the residual stresses induced during the manufacturing process in composite components is necessary for the timely fielding of new combat systems. At the U.S. Army Research Laboratory we have developed a computational environment to model the resin flow, heat transfer, curing, and residual stresses in composite components manufactured with the resin transfer molding (RTM) process. This computational environment uses object-oriented programming methods to provide model coupling capabilities and access to high performance computing assets. In this paper we will provide details of the physical models, software, and the validation/verification procedure used to develop this RTM simulation package.Cite This Article
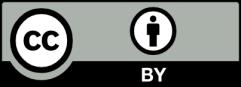
This work is licensed under a Creative Commons Attribution 4.0 International License , which permits unrestricted use, distribution, and reproduction in any medium, provided the original work is properly cited.