Open Access
ABSTRACT
Prediction Method of Vibration and Noise Regarding Mechanical Systems by Means of Experimental Modeling
Master Course, Department of Mechanical and Aerospace Engineering, Tokyo Inst. of Tech., Japan
Power Products R&D Center, HONDA R&D Co., Ltd., Japan
Department of Mechanical and Aerospace Engineering,Tokyo Inst. of Tech., 2-12-1-I3-15, O-okayama, Meguro-ku, Tokyo, 152-8552, Japan, E-mail:mokuma@mech.titech.ac.jp
The International Conference on Computational & Experimental Engineering and Sciences 2008, 6(2), 145-150. https://doi.org/10.3970/icces.2008.006.145
Abstract
The accurate modeling of structures is very important for any engineering analysis such as simulation and design optimization of mechanical systems for noise and vibration. It is desired that such a modeling process should not be time-consuming and that the created model must have structural dynamic properties corresponding with the actual ones. But in practice, it is often difficult or even impossible to satisfy the desire by using conventional theoretical methods such as the Finite Element Method (FEM) when we consider actual mechanical systems which consist of many substructures. In this paper, under the assumption that vibration tests can be carried out for actual substructures, we introduce an experimental method for composing the spatial matrix of a whole mechanical system based on the superposition of the substructures' spatial matrices, and for computing prediction analysis about vibration and noise of the whole mechanical system. The substructures' spatial matrices are acquired using an experimental spatial matrix identification method [1\hbox {}][2\hbox {}]. It can make it easy and reliable to make computational models of actual and complex substructures as a database, and can make prediction analysis be carried out smart for the whole systems composed of various combination choices of substructures. The method also works efficiently for structural modification analysis in the case that some of substructures of the whole system are to be modified in the design process. We show a case study using a boat that consists of mainly three substructures, namely a boat hull, an outboard engine and its suspension.Cite This Article
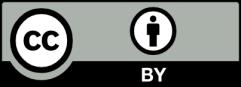
This work is licensed under a Creative Commons Attribution 4.0 International License , which permits unrestricted use, distribution, and reproduction in any medium, provided the original work is properly cited.