Open Access
ABSTRACT
Experimental Fracture Mechanics for Adhesive Joint Design
Sr. Research Engineer/Manager, National Institute for Aviation Research, Wichita State University, Wichita, Kansas , KS 67260-0093.
Executive Director
Research Engineer
The International Conference on Computational & Experimental Engineering and Sciences 2007, 4(2), 81-86. https://doi.org/10.3970/icces.2007.004.081
Abstract
An experimental study was conducted to investigate the use of fracture mechanics to predict failure initiation of adhesive joints. Most practical plane fracture problems are mixed mode and failure initiation of adhesive joints is a result of such conditions. It is widely accepted that a useful method for characterizing the toughness of bonded joints is to measure the fracture toughness; energy per unit area needed to produce failure. For a given adhesive, mode mixity has a dependency towards fracture toughness and fracture toughness is directly associated with stress. Main goal in this investigation was to demonstrate the capability of utilizing experimental fracture mechanics data to predict the failure initiation of an adhesive joint. First, critical energy release rates for several mode mixities were experimental determined (Tool 1) for selected adhesives using double cantilever beam (DCB), end-notch flexure (3ENF), and mixed-mode bending (MMB) test methods to determine mode I, mode II, and mixed-mode I & II fracture toughness values, respectively. Then, a stress analysis was conducted to determine the mode mixity at a crack tip of the adhesive joint design (Tool 2); crack-tip location must be selected based on previous experimental observations. Further, a relationship between applied load and the energy release rate was obtained from the same model (Tool 3). Once the mode mixity of the crack tip was determined from Tool 2, Tool 1 can be used to determine the critical energy release rate corresponding to the crack tip of a particular adhesive joint. Finally, Tool 3 can be used to determine the critical state of stress or the failure initiation load corresponding to that critical energy release rate. Singe-lap adhesive test specimens were fabricated and tested for two adhesive types and the failure loads were compared with the predictions made using the proposed approach. It was concluded that failure loads predicted by mode mixity-fracture toughness curves were in good agreement with those obtained experimentally.Cite This Article
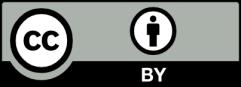
This work is licensed under a Creative Commons Attribution 4.0 International License , which permits unrestricted use, distribution, and reproduction in any medium, provided the original work is properly cited.