Open Access
PROCEEDINGS
Optimized Design Study of Subsea Hydrothermal Closed-Loop Heat Collection System Based on Numerical Simulation
1 Mechanical Engineering, College of Engineering, Ocean University of China, Qingdao, 266100, China
2 Department of Mechanical Engineering, National University of Singapore, 10 Kent Ridge Crescent, Singapore, 119260, Singapore
* Corresponding Author: Yan Li. Email:
The International Conference on Computational & Experimental Engineering and Sciences 2024, 32(3), 1-3. https://doi.org/10.32604/icces.2024.011165
Abstract
1 IntroductionWith dwindling terrestrial energy resources, there's a societal consensus to harness clean, renewable energy. Submarine hydrothermal vents, hosting abundant and unexplored energy potentials, draw international academic scrutiny [1]. Yet, comprehensive research on exploiting their thermal energy systems remains sparse. Existing technologies persist with stability and efficiency challenges. While promising ventures in hydrothermal power generation exist, they grapple with heat loss, instability, limited capacity, and heightened damage susceptibility [2]. This study scrutinizes submarine hydrothermal vents, amalgamating terrestrial closed-loop geothermal technology to resolve challenges and enable efficient energy utilization [3]. Given the complex geology of these vents, rigorous design and performance parameters for hydrothermal closed-cycle heat extraction devices are necessary. The study employs a unified physical model of a thermotube and hydrothermal reservoir, implementing ANSYS+LBM (Lattice Boltzmann Model) methodologies to investigate the influence of structural parameters on heat transfer. Using MATLAB for solving the programming of heat pipe heat transfer processes, it lays the groundwork for efficient utilization of hydrothermal reservoir thermal energy. Incorporating multidisciplinary techniques and practical applications, the study offers novel insights for exploiting seafloor thermal energy.
2 Research Methods
This study grapples with the hydrothermal reaction belt in the East Pacific Rise Mid-Ocean Ridge [4], characterized by igneous rock strata overlayed by sedimentary formations, robust fissure systems, and dual-phase seepage. The hydrothermal circulation and geological structure are illustrated in Fig.1(1,2,3). Herein, we propose the use of earth-encased coaxial pipes to harness thermal energy from these marine hydrothermal reservoirs in Fig.1(1,4). This concept incorporates the backfilling of drilled holes with suitable materials to stabilize placement and bolster heat transfer. The submarine hydrothermal closed-loop heat extraction model comprises a hydrothermal reservoir, an earth-encased pipe, and an annular backfill layer in Fig.2. This complex porous structure, informed by geological characteristics, primarily facilitates fluid flow. Employing ANSYS software and the LBM, a computationally simulated hydrothermal vent closed-cycle heat extraction system is analyzed to discern the optimal conditions for efficient thermal energy exploitation.
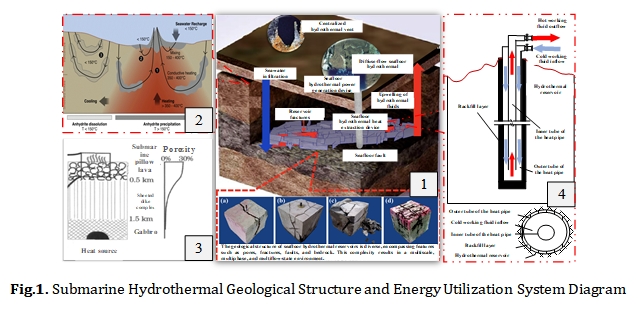
Fig.1. Submarine Hydrothermal Geological Structure and Energy Utilization System Diagram
3 Results and Discussion
3.1 DEM validation
At a permeation speed of 1×10-3 m/s, thermal fluid temperature of 523K, and porosity of 0.3, noticeable thermal/velocity variations occur around the heat pipe. The alterations in speed significantly impact thermal distribution, reaching 27.3% of maximum space at 5×10-4 m/s and diminishing to 12.1% at a higher velocity of 5×10-3 m/s. These phenomena, along with minimal thermal fluid temperature effects and significant porosity-induced thermal dispersal effects, inform optimization computations.
3.2 Backfill Layer Simulation Results
In response to heightened porosity (range 0.1-1) in the backfill layer, simulation results manifest a significant surge (11.7%-36.2%) in the pipe's heat exchange coefficient, enhancing heat exchange efficacy. The distribution of the flow field and the principles are depicted in Fig.3. Optimal heat transfer aligns with a porosity value of 0.8. An accelerated increase in backfill material's heat conductivity, beyond 1.4 times the reservoir rock's maximum (2.25 W/mK), does not explicitly enhance heat exchange—a trend evident in simulations. Optimum heat exchangement is witnessed when the backfill layer's thickness equals 1.1 times the pipe's diameter. Implementing high-conductivity metal foam as backfill material demonstrates superior heat exchange efficiency, justifying this innovative solution. Our composite backfill material, thereby, advances deep-sea thermal harvesting applications.
3.3 Thermotube Structural Calculation Results
A mathematical model facilitated studying parameter impact on heat exchange systems, using MATLAB generated solutions. Discerned optimal lengths and internal flow rates for the thermotube were 200m and 0.6kg/s, respectively.
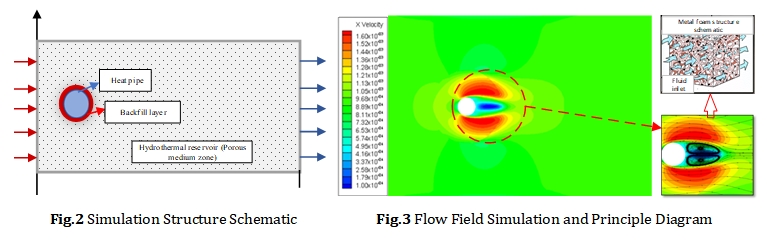
4 Conclusions
This research utilizes ANSYS+LBM methodology for a comprehensive model coupling heat pipes and hydrothermal reservoirs. Using high porosity metal foam as an isolation layer escalated temperature gradients and heat flow density by 81% and 62% respectively. With optimal parameters, the research anticipates a 30% efficiency increase, paving a new route for submarine clean energy development.
Keywords
Cite This Article
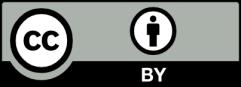
This work is licensed under a Creative Commons Attribution 4.0 International License , which permits unrestricted use, distribution, and reproduction in any medium, provided the original work is properly cited.