Open Access
PROCEEDINGS
Advancing Ultrasonics-Based Techniques for Non-Destructive Evaluation of Additive Manufactured Composites
1 School of Astronautics, Beihang University, Beijing, 100191, China
2 Unmanned System Research Institute, Northwestern Polytechnical University, Xi’an, 710072, China
3 Department of Mechanical Engineering, Imperial College London, Exhibition Road, London SW7 2AZ, United Kingdom
* Corresponding Author: Xudong Yu. Email:
The International Conference on Computational & Experimental Engineering and Sciences 2024, 32(2), 1-2. https://doi.org/10.32604/icces.2024.011546
Abstract
The continuous advancement of Additive Manufacturing (AM) technologies has revolutionized the production of intricate components and reinforced composites with tailored mechanical properties. However, the variability in AM techniques and processing parameters often leads to discrepancies in fibre volume fraction, porosity, and interfaces in AM composites, resulting in dispersed elastic moduli and mechanical responses, which necessitates robustness non-destructive evaluation (NDE) methods. Additionally, AM introduces new defect morphologies, dimensions, and locations, demanding new and more reliable non-destructive testing (NDT) techniques.This research commences by quantifying orientation-dependent mechanical properties of laser-sintered nanocomposites of carbon nanotube (CNT) reinforced polyamine (PA). An immersion ultrasonic technique is employed to measure the energy loss and propagation speeds of ultrasonic elastic waves in the CNT-coated PA12 composites. The study investigates the relationship of process-structure-property between ultrasonic attenuation/speed and process parameters, linking them to the layer-by-layer fusion induced microstructures and internal imperfections, such as interlayer/innerlayer defects, fibre agglomeration and interface quality of fibre/matrix. The results are validated using optical microscopy and mechanical testing.
Furthermore, the study proposes an immersion ultrasonics-based method with inversion schemes for measuring the effective anisotropic stiffness matrix of continuous fibre reinforced composites. Material properties of thin composite plates are derived by numerically inverting the transmitted ultrasonic fields obtained for different incident angles, thus finding the best-fit solution for all the independent components of stiffness matrix. Two types of T700/PA plates with transversely isotropic and orthotropic symmetries are experimentally characterized, and the reliability of the measured stiffness properties is verified via mechanical testing.
Moreover, the research presents a single-sided, air-coupled ultrasonic NDT capability for automated fiber placement (AFP) based composite structures, via the generation and reception of the Lamb-type ultrasonic guided waves, scanning over the surface of AM plate-like structures. The baseline of intact quality is established; temporal and frequential signal processing procedures are performed to quantify the reflection and transmission coefficients and mode conversion of guided waves scattered by defects in manufactured composites. The validity and precision of defect detection are verified by the monitoring data during the AM process, and the associated in-situ NDT module can potentially be integrated into future AM systems.
The proposed series of techniques demonstrate the potential and strong incentives of ultrasonics-based NDT&E for in-process and continuous monitoring of AM composites, aiming at quality control and structural safety inspection in end-use applications.
Keywords
Cite This Article
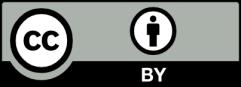
This work is licensed under a Creative Commons Attribution 4.0 International License , which permits unrestricted use, distribution, and reproduction in any medium, provided the original work is properly cited.