Open Access
PROCEEDINGS
Multi-Scale Microstructure Manipulation of an Additively Manufactured CoCrNi Medium Entropy Alloy for Superior Mechanical Properties and Tunable Mechanical Anisotropy
1 School of Mechanical and Manufacturing Engineering, The University of New South Wales (UNSW Sydney), Sydney NSW 2052, Australia
2 Sandia National Laboratories, Albuquerque, NM 87185, United States
3 School of Materials Science and Engineering, The University of New South Wales (UNSW Sydney), Sydney NSW 2052, Australia
* Corresponding Author: Xiaopeng Li. Email:
The International Conference on Computational & Experimental Engineering and Sciences 2024, 31(4), 1-2. https://doi.org/10.32604/icces.2024.011290
Abstract
Laser powder bed fusion (LPBF) additive manufacturing (AM) technology has become a versatile tool for producing new microstructures in metal components, offering novel mechanical properties for different applications. In this work, enhanced ductility (~55% elongation) and tunable mechanical anisotropy (ratio of ductility along vertical to horizontal orientation from ~0.2 to ~1) were achieved for a CoCrNi medium entropy alloy (MEA) by multi-scale synergistic microstructure manipulation (i.e., melt pool boundary, grain morphology and crystallographic texture) through adjusting key LPBF processing parameters (e.g., laser power and scan speed). By increasing the volumetric energy density (VED) from 68.3 to 144 J/mm3, the melt pool size enlarges, and the crystallographic texture transitions from <100>//BD to <110>//BD due to the maximum thermal flux direction changing for different melt pool dimensions, which affects the proportion of grains that have different growth directions. Moreover, excellent mechanical properties of 890 MPa ultimate tensile strength and ~55% elongation to failure can be achieved for loading perpendicular to the build direction with only a ~15% reduction in properties for loading along the build direction. The superior combination of mechanical properties is achieved by processing parameter-controlled strengthening of melt pool boundary interfaces, heterogeneous deformation induced strengthening through bimodal grain structures, and favorable grain orientation for dislocation slip and twinning formation, which was significantly more activated in the <110>//BD texture than in the <100>//BD. This study offers new insights into achieving multi-scale synergistic microstructure manipulation via LPBF for desired strength, ductility, and mechanical anisotropy in a CoCrNi MEA.Keywords
Cite This Article
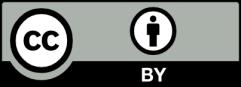
This work is licensed under a Creative Commons Attribution 4.0 International License , which permits unrestricted use, distribution, and reproduction in any medium, provided the original work is properly cited.