Open Access
PROCEEDINGS
3D-Printable Centimeter-Scale Tensegrity Structures for Soft Robotics
1 National University of Singapore, 09 Engineering Drive 1, Singapore, 117575, Singapore
* Corresponding Author: Hongying Zhang. Email:
The International Conference on Computational & Experimental Engineering and Sciences 2024, 31(3), 1-3. https://doi.org/10.32604/icces.2024.012193
Abstract
Tensegrity metamaterial, well-known for its unique synergy between compressed bars and tensile strings, enable a remarkable deformation and distinctive vibration characteristic [1]. These materials are increasingly recognized for their potential to facilitate advanced locomotion in soft robots. Tensegrity metamaterials, primarily constructed manually, have found applications in large-scale sectors like architecture and aerospace engineering [2]. However, their integration into soft robots necessitates scaling down to a centimeter scale, presenting challenges in automatic prototyping and kinematic simulation to guide the design process [3].Recent advancements advocate for 3D-printed tensegrity structures to achieve integrated, one-piece systems [3,4]. Yet, challenges persist, particularly in prestressing strings and actuating structural tensegrity. Kinematic models have been developed to predict tensegrity responses to various stimuli [5-7], however, these predominantly macro-scale analyses fall short when applied to millimeter-scale structures.
Our study proposes an innovative 3D printing approach to fabricate a cohesive tensegrity system, integrated with shape memory polymer (SMP) bars as actuators. We illustrate this fabrication process using the tensegrity structure in Fig. 1(a)-(h), which undergoes a two-step 3D printing and sequential molding protocol. Initially, we fabricate SMP bars with zero-Poisson’s ratio designs, allowing extensive elongation without altering cross-sectional dimensions, as shown in Fig. 1(a)-(c). Concurrently, a water-soluble mold is printed to situate the SMP bars and rubber strings (Fig. 1(d)-(e)). Sequentially, mixed silicone rubbers are injected into the mold, solidified (Fig. 1(f), and the mold is dissolved to unveil the finalized tensegrity structure Fig. 1(g). A zoom-in of the tensegrity structure is provided in Fig. 1(h). The SMP bars are then heated to introduce elongation and prestress in the silicone rubber strings.
Furthermore, we develop a kinematics simulator in MATLAB tailored for centimeter-scale tensegrities, capable of universally modeling dynamics across various configurations once the structure of tensegrity metamaterials is defined. Preliminary results, as demonstrated in Fig. 1(i)-(j), showcase simulations for 4-bars and 6-bars cubes under compression, juxtaposed with ABAQUS/CAE simulations shown in Fig. 1(k) and (l), with discrepancies within 11% for the 4-bars cube and 15% for the 6-bars cube, affirming the simulators precision. This simulator has the potential to give actionable insights into the control and actuation of these intricate structures.
The proposed methodology and simulator promise to significantly impact the design, simulation, and production of millimeter-scale tensegrity robots, offering a new frontier in soft robotic locomotion and manipulation.
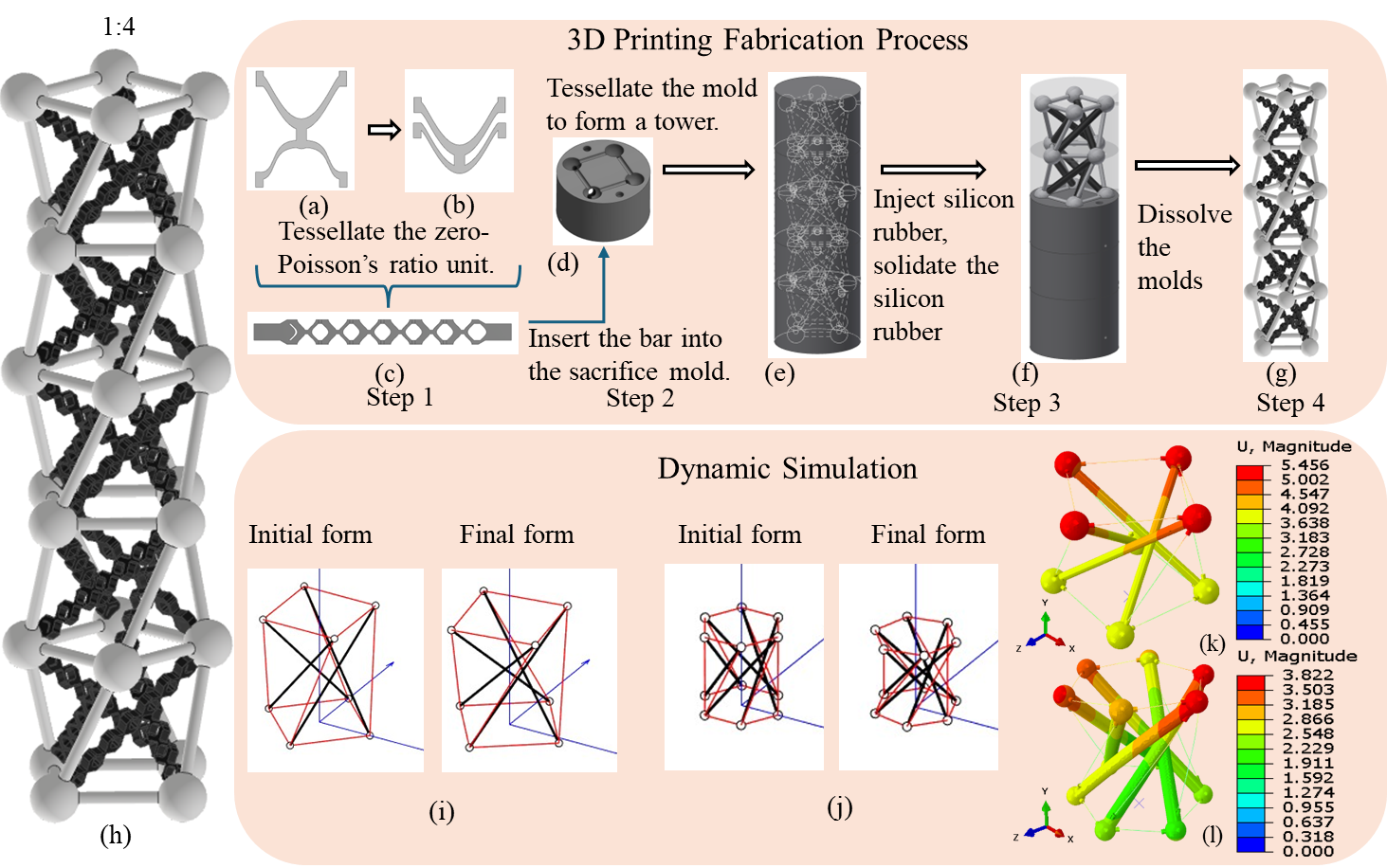
Fig. 1. 3D printing fabrication process and the dynamic simulation of 3D-printed tensegrity structure integrated with SMP bars. (a) and (b) shows bistable states of zero-Poison’s ratio unit. (c) shows the bar formed by tessellating the pre-mentioned units. (d) shows a water dissolvable mold units that will be integrated with the bars in (c) and tessellated into a tower in (e). Inject the silicone rubber into the mold and solidate them in (f), where the bars colored in black are connected by silicone rubbers in grey to form a tensegrity tower structure. Dissolve the mold and the final structure is given in (g). A zoom-in of the SMP-bars integrated 3D-printed tensegrity tower is provided in (h). Preliminary simulation results of the promoted tensegrity simulator is given in (i)-(j). (i) shows the initial and final form of a 4-bars tensegrity unit cube under compression at the top nodes. The size of the cube is 5*5*5.5(cm3). (j) shows the initial form and the final form of a 6-bars tensegrity unit under compression load at top nodes. The diameter of the hexagon is 3cm and the height of the cube is 3cm. (k) and (l) shows the ABAQUS/CAE simulation for the same cases in (i) and (j) accordingly for the verification of accuracy. The discrepancies lie within 11% for the 4-bars cube and 15% for the 6-bars cube.
Keywords
Cite This Article
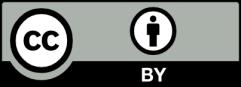
This work is licensed under a Creative Commons Attribution 4.0 International License , which permits unrestricted use, distribution, and reproduction in any medium, provided the original work is properly cited.