Open Access
PROCEEDINGS
4D Printing of Polymeric Reinforced Composites
1 School of Mechanical and Aerospace Engineering, Nanyang Technological University, 50 Nanyang Avenue, 639798, Singapore
2 School of Materials Science and Engineering, Nanyang Technological University, 50 Nanyang Avenue, 639798, Singapore
* Corresponding Author: Hortense Le Ferrand. Email:
The International Conference on Computational & Experimental Engineering and Sciences 2024, 31(2), 1-1. https://doi.org/10.32604/icces.2024.010990
Abstract
4D printing enables 3D-printed structures to morph upon being exposed to external stimuli. Amongst all engineering materials, polymers show high 3D printability as well as tunability regarding to its morphing behaviour and functionalities. Generally, composites with epoxy as matrix shows high modulus and strength, whereas its mechanically brittle property makes it difficult to be morphed and snapped-through at room temperature, thereby limiting its 4D printability and its functionality. On the other, Polydimethylsiloxane (PDMS), as an elastomer, shows its high elasticity and stretchability, yet its printability and mechanical properties of its printed composites still need improving for 4D printing and its intrinsic functions. In this work, we developed a group of printable PDMS composite ink, and used direct-ink writing (DIW) to fabricate an elastomer-like fibre-reinforced PDMS composites, which showed temperature-controlled morphing, thanks to the anisotropic morphology of the microstructure induced by fibre alignment due to the shear of the printing. The composite was printed on the flat substrate and cured under room or high temperatures, heated up and cooled down to study the morphing behaviour (curvature, directions, and shape). The experimental results revealed that by tuning the ink composition, DIW printing parameters, layup of the composite laminate, curing methods (temperature and time) and post-curing heating, the macroscopic structure can be controlled as programmed. As such, our work can prospectively fabricate functional composites with controlled morphing behaviours such as mechanical bistability, which can be used in applications such as actuation, sensing or self-deploying.Keywords
Cite This Article
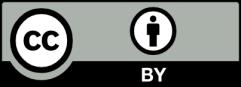
This work is licensed under a Creative Commons Attribution 4.0 International License , which permits unrestricted use, distribution, and reproduction in any medium, provided the original work is properly cited.