Open Access
PROCEEDINGS
Integrated Workflow of Design for Additive Manufacturing: From Topology Optimization to Distortion Compensation
1 Singpaore Institute of Manufacturing Technology, 5 Cleantech Loop #01-01, CleanTech Two Block B (CT2B), 636732, Singapore
* Corresponding Author: Chen Wang. Email: -star.edu.sg
The International Conference on Computational & Experimental Engineering and Sciences 2024, 31(1), 1-2. https://doi.org/10.32604/icces.2024.011846
Abstract
Industry 4.0 promises to bring significant changes to general additive manufacturing (AM) systems, ushered by the incorporation of digital twin development to capture high-volume data in an integrated and automated way [1]. During this transformation, it is required to develop advanced methods to solve main problems in the large-scale industrial use of AM technology. One of the challenges is how to eliminate or mitigate the structural distortion due to thermal effect during AM processes [2-4]. To reduce the level of distortion, a general hands-on approach is to compensate the geometry based on physical measurements of the trial-printed and distorted shape [5].This study presents a digital and integrated method to solve the three-dimensional distortion problems in the Design for Additive Manufacturing (DfAM) stage. The method extends the DfAM from topology optimization to distortion compensation. In industry case studies including a satellite part support and a long bracket, predictions of thermal distortion were integrated with the design stage. After topology optimization, the designs were numerically analyzed considering interaction between heat and material in the AM process. Distortion data was collected from every element of the part, instead of a few discrete points from measurement. To create a reliable processing model, the study started with effects of part geometries and thermal parameters on the part’s distortion, followed by validating relationships between computed results and experimental measurements from AM parts using the coordinate measuring machine. Subsequently, a nonlinear compensation method was developed based on the nodes of mesh structures, mapping a compensated new geometry for AM. The algorithm was developed based on coordinate adjustments from independent axis to coupling coordinate directions. The ultimate printing accuracy in case studies showed this method enables perform direct geometrical modifications to a given part’s STL model to help counteract the thermal shrinkage and three-dimensional deformations. The research outcome provides an automated platform for design and virtual manufacturing. The strategy of integration can also be leveraged to other advanced manufacturing processes, as illustrated in a multi-material overmoulding case.
Keywords
Cite This Article
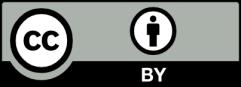
This work is licensed under a Creative Commons Attribution 4.0 International License , which permits unrestricted use, distribution, and reproduction in any medium, provided the original work is properly cited.