Open Access
PROCEEDINGS
Effect of Slender Bar Structures on the Boundary on Cavitation Bubble Dynamics Due to Self-Focusing Shockwaves
1 State Key Laboratory of Hydro Science and Engineering, and Department of Energy and Power Engineering, Tsinghua University, Beijing, 100084, China
2 Department of Soft Matter, Institute of Physics, Faculty of Natural Sciences, University of Magdeburg, Universitätsplatz 2, 39106, Magdeburg, Germany
* Corresponding Authors: Zhigang Zuo; Shuhong Liu; Claus-Dieter Ohl. Email: ;
;
The International Conference on Computational & Experimental Engineering and Sciences 2024, 30(4), 1-1. https://doi.org/10.32604/icces.2024.012155
Abstract
When cavitation bubbles collapse near a boundary, they can cause severe cavitation erosion to the boundary, which is a dangerous threat to the rapidly rotating turbines. Prior research has established that for single bubbles a possible mechanism is energy focusing of shockwaves during the non-spherical collapse of cavitation bubbles [1]. This however needs a particularly symmetric environment. A possible approach to reduce the shockwave focusing and thus the erosion would be through suitable modification of the boundary. In a first approach to modify this phenomenon, we introduce the symmetry breaking structure on the boundary in the shape of a slender bar to explore the effect of the asymmetry on the order and speed of the cavitation bubble torus collapse quantitatively. The dynamics of a single laser-induced cavitation bubble in the presence of this symmetry breaking structure is measured with two high-speed cameras. The asymmetry depending on the distance from the bubbles causes the split up of the torus into two. With decreasing distance between the bubble and the structure the speed of the torus collapse initially decreases and then increases. Our findings may guide the design of microstructures on surfaces to reduce cavitation erosion or enhance energy focusing from single cavitation bubbles which can be exploited for engineering applications.Keywords
Cite This Article
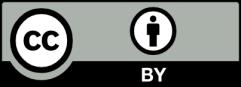
This work is licensed under a Creative Commons Attribution 4.0 International License , which permits unrestricted use, distribution, and reproduction in any medium, provided the original work is properly cited.