Open Access
PROCEEDINGS
Mechanisms of Thermo-Mechanical Fatigue Crack Growth in a Polycrystalline Ni-Base Superalloy
1 College of Energy and Power Engineering, Nanjing University of Aeronautics and Astronautics, Nanjing, 210016, China
2 State Key Laboratory of Mechanics and Control Mechanical Structures, Nanjing University of Aeronautics and Astronautics, Nanjing, 210016, China
* Corresponding Author: Lu Zhang. Email:
The International Conference on Computational & Experimental Engineering and Sciences 2024, 30(3), 1-2. https://doi.org/10.32604/icces.2024.012701
Abstract
Thermo-mechanical fatigue (TMF), as the main failure mode of hot components of an aeroengine, are increasingly investigated recently [1,2]. TMF crack growth is studied in a nickel-based powder metallurgy (PM) superalloy subjected to in-phase (IP) and out-of-phase (OP), as well as isothermal fatigue (IF) at peak temperature. The crack growth rate and path are evaluated for both coarse grain (CG) and fine grain (FG) structure, especially the effects of phase angle and polycrystalline microstructure. The results show that the TMF crack propagation is mainly transgranular in OP condition; while in IP condition, crack propagates intergranularly at low ∆K and transforms to transgranular after passing the transition region. The crack propagation resistance for FG microstructure is lower than that for CG microstructure at elevated temperature, as a result of slip activities and grain boundary weakening effect [3,4]. The turning point where da/dN vs ΔK curve changes from fluctuating to stable in IP condition, represents the change of fatigue crack growth from intergranular to transgranular feature. The formation of secondary cracks is closely related to local misorientation and crystallographic deformation during TMF crack propagation. The crack deflection in a single grain reveals competition mechanism between crystallographic slip and grain boundary effect, which explains the lower crack growth rate for OP when compared to than IP or IF. Finally, TMF in a polycrystalline nickel-based superalloy was well understood from damage to fracture, which provides guidance for the integrity design and life assessment of high-temperature components [5].Keywords
Cite This Article
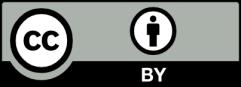
This work is licensed under a Creative Commons Attribution 4.0 International License , which permits unrestricted use, distribution, and reproduction in any medium, provided the original work is properly cited.