Open Access
PROCEEDINGS
A Study on the Extraction and Evaluation Method of Virtual Strain
1 Department of Engineering Mechanics, Northwestern Polytechnical University, Xi’an, 710129, China
2 Shenyang Aircraft Design Institute of AVIC, Shenyang, 110035, China
* Corresponding Author: Peiyan Wang. Email:
The International Conference on Computational & Experimental Engineering and Sciences 2024, 30(3), 1-1. https://doi.org/10.32604/icces.2024.011318
Abstract
The virtual test is supported by the physical test data, and a high-precision simulation model needs to be established to maximize the alignment between the simulation prediction results and the physical test data. It can replace other physical tests and achieve the goal of reducing the design cycle time and cost. However, due to the errors caused by the position and angle deviation of the strain gauge paste, as well as the sensitivity coefficient of the strain gauge and the wire, it is difficult for the simulation results to correspond to the test results in space. In this paper, the simulation model obtains the strain of the observation point in real time using the inverse distance interpolation method, while also considering the random uncertainty of position and angle. Then the simulated strain value on the typical structure was all obtained, and a comprehensive strategy for virtual tests was constructed through the analysis of the test strain and virtual strain. The comparative analysis of wing leading edge tests and simulation reveals that the method in this paper has the characteristics of simplicity, efficiency, and high accuracy in constructing a virtual test model with exceptional precision. This approach effectively integrates physical testing and simulation modeling.Keywords
Cite This Article
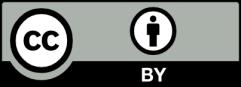
This work is licensed under a Creative Commons Attribution 4.0 International License , which permits unrestricted use, distribution, and reproduction in any medium, provided the original work is properly cited.