Open Access
PROCEEDINGS
Topology Optimization for Multi-Axis Additive Manufacturing
1 University of Alberta, 116 St and 85 Ave, Edmonton, Alberta, T6G 2R3, Canada
2 Shandong University, Shanda S Rd, Jinan, 250100, China
3 Southern University of Science and Technology, 1088 Xueyuan Blvd, Shenzhen, 518055, China
* Corresponding Authors: Yongsheng Ma; Rafiq Ahmad. Email: ;
The International Conference on Computational & Experimental Engineering and Sciences 2024, 30(2), 1-2. https://doi.org/10.32604/icces.2024.011177
Abstract
Multi-axis additive manufacturing (AM) is an advanced manufacturing method with advantages over traditional 3-axis additive manufacturing. A formidable challenge in AM is widely acknowledged in utilizing support materials, a process characterized by temporal and material resource consumption. Extensive research endeavors have been dedicated to mitigating or eliminating reliance on support materials, particularly emphasizing pioneering self-supporting design strategies. Empirical investigations reveal that when the overhang angle of a structure surpasses a predefined threshold (typically 45°), support structures may become dispensable for assisted printing. In traditional 3-axis AM systems, achieving support-free printing for structures exhibiting overhang angles below this threshold is insurmountable. However, within the domain of multi-axis AM systems, the realization of self-supporting requirements becomes feasible by manipulating the printing platform's orientation. Not only can we rotate the platform at the beginning of printing, but we can also do so during the printing process. The feasible platform allows structures with significant differences in overhang angles to achieve self-supporting printing, which presents an excellent opportunity for structural design for AM. Therefore, this work presents a computational method for fabrication sequence optimization for self-support structure in multi-axis additive manufacturing, in which the fabrication sequence is not limited to planar layers only.In this method, the topology, fabrication sequence, and building directions are concurrently optimized to achieve better structural performance. This method establishes the overhang constraint using a novel convolution approach, which avoids the commonly observed "dripping effect" in self-supporting designs. A pseudo-time field is introduced to represent the printing order in the fabrication sequences. The manufacturing process can be divided into multiple steps by partitioning the time field. The printing platform angle remains constant in each step, and the structure printed in this step is self-supporting. Moving to the next step, the printing platform angle can be optimized and changed while ensuring that the structure printed in this step remains self-supporting relative to the new printing platform angle. This process is repeated until the printing is completed. For simplicity, we assume a constant fabrication speed, i.e., each step has the same material volume. In addition, this work also addresses the avoidance of collisions between the print head and the already printed structure by introducing a collision constraint. In this constraint, users can define the direction and shape of the print head.
Fig.1 shows the 2D numerical results of the proposed method. It is impossible to complete self-supporting printing of the structure shown in Fig. 1(a) with a 3-axis printing system. The upper part of the structure has a near-horizontal overhang that must be supported. However, in a multi-axis system, it can complete self-supporting printing by rotating the printing platform as shown in Fig. 1(b)-(d). Meanwhile, the finished structure at each step will not collide with the printing head. Fig.2 shows the 3D numerical results.

Fig. 1. The fabrication sequences of multi-axis AM for MBB in 2D, (a) the optimized structure, (b) the first step, (c) the second step, (d) the final step.

Fig. 2. The fabrication sequences of multi-axis AM for MBB in 3D, (a) the optimized structure, (b) the first step, (c) the second step, (d) the final step.
Keywords
Cite This Article
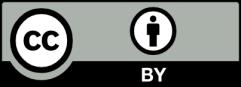
This work is licensed under a Creative Commons Attribution 4.0 International License , which permits unrestricted use, distribution, and reproduction in any medium, provided the original work is properly cited.