Open Access
PROCEEDINGS
Hot Corrosion Caused Damage to the Ni-Based Single Crystal Superalloy in the Presence of NaCl at 760℃
1 State Key Laboratory of Clean and Efficient Turbomachinery Power Equipment,School of Mechanics,Civil Engineering and Architecture, Northwestern Polytechnical University,Xi’an, 710072, China
* Corresponding Author: Xinmei Wang. Email:
The International Conference on Computational & Experimental Engineering and Sciences 2024, 30(2), 1-2. https://doi.org/10.32604/icces.2024.010965
Abstract
Ni-based superalloys are the main material for the high pressure turbine blades of modern gas turbine engines [1]. High temperature corrosion of the blade, also called hot corrosion, is inevitable due to the working environment which directly affects the performance and life of the engine [2]. The working environment is harsher if the turbine engine is used in the sea environment. The salt fog of high humidity in the sea results in the chloride of NaCl and KCl. Coupled hot corrosion and high temperature oxidation increase the decay of the blade performances. Therefore, it is necessary to study the damage of hot corrosion to the nickel based single crystal alloy.The material used is the standard heat-treated second generation nickel-based single crystal superalloy René N5. The salt-recoating (“deposit recoat”) method was used to simulate the service environment of the blade [3,4]. A dried salt layer of 3±0.2 mg/cm2 was achieved which was well distributed on the surface of the sample. Cyclic hot corrosion tests were performed in static air at 760 °C for totally 200h with 20 cycles. All the analysis were performed after the desalting of the specimens. Three samples were measured to get the average value of mass changes. The overall morphology of the specimens were analyzed by an optical microscope with super-high magnification lens zoom. A scanning electron microscope (SEM) with X-ray energy dispersive spectroscopy (EDS) was used to analyze the morphology and element distributions (point, line scan and area mapping). The corrosion products were analyzed by X-ray diffraction (XRD).
The mass change can be divided into three stages, i.e., oscillation period in the first 40 h, rapid change period from 40 h to 60 h and slow change periods after 60 h. Morphology analysis shows that the increase of corrosion layer is very slow at the first stage. It obviously increases at the second stage when a large amount of oxidation products and volatile chlorides are generated on the surface of the specimen. Apparently delaminates along the cross section are found at the third stage. The surface of the specimen is uneven with continuous oxide film in most areas and small holes in some areas. The corrosion products are mainly composed of NiO at the outer oxide layer, with some spinel presented. The inner layer is mainly composed of Al2O3 and Cr2O3, while the content of W, Ta, Mo, and Re in the transition layer is slightly higher. Sodium chloride causes diffusion of elements such as Cr, Al, Ni, Co. Elements Al and Cr mainly migrate outward, and some local areas are severely depleted of Cr elements, resulting in damage of γ/γ’ microstructure. Metal carbides MC are found in the Ta element enriched area. The generation of chlorine gas can destroy the corrosion layer and form holes as passageway for further corrosion of the specimen.
Keywords
Cite This Article
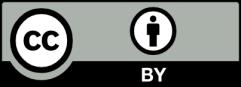
This work is licensed under a Creative Commons Attribution 4.0 International License , which permits unrestricted use, distribution, and reproduction in any medium, provided the original work is properly cited.