Open Access
PROCEEDINGS
Heat Generation, Plastic Deformation and Stresses Evolution in Inertia Friction Welding of Ni-Based Superalloy
1 Shandong University, 17923 Jingshi Road, Jinan, 250061, China
* Corresponding Author: Guoliang Qin. Email:
The International Conference on Computational & Experimental Engineering and Sciences 2024, 30(1), 1-1. https://doi.org/10.32604/icces.2024.012370
Abstract
The interactions among thermal history, plastic deformation and stress in inertia friction welding (IFW) under different welding parameters have been widely considered a crucial issue and still not fully understood. A novel 3D fully coupled finite element model based on a plastic friction pair was developed to simulate the IFW process of a Ni-based superalloy and reveal the omnidirectional thermo-mechanical coupling mechanism under different welding conditions. The numerical model successfully simulated the deceleration, deformation processes, and peak torsional moments in IFW and captured the evolution of temperature, plastic deformation, and stress. The simulated results were validated through measured thermal history, optical macrography, and axial shortening. The results indicated that interfacial friction heat was the primary heat source, and plastic deformation energy only accounted for 4% of the total. The increase in initial rotational speed and friction pressure elevated the peak temperature, reaching a maximum of 1525.5 K at 2000 rpm and 400 MPa. The interface heat generation could form an axial temperature gradient exceeding 320 K/m. The maximum heat flux and temperature located in a concentric ring distribution on the interface ranging from 2/5 to 2/3 radius. The phenomena were caused by increasing linear velocity along the radius and an opposite distribution of contact pressure, which could reach 1.7 times the set pressure at the center. The deflection and transformation of distribution in contact pressure and Mises stress, which were the indicators of plastic deformation and transition of quasi-steady state welding, was revealed for the first time during rotary friction welding, benefiting from the 3D model. The critical Mises stress was 0.5 times the friction pressure in this study. The plastic deformation results shown that the maximum circumferential plastic flow of the interface exceeded 130 °, and the removal rate of the original interface could exceed 95%. Based on the reliable simulation of thermo-mechanical behavior, the prediction of dynamic recrystallization microstructure of IFWed joints were successfully achieved.Keywords
Cite This Article
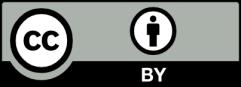
This work is licensed under a Creative Commons Attribution 4.0 International License , which permits unrestricted use, distribution, and reproduction in any medium, provided the original work is properly cited.