Open Access
PROCEEDINGS
Concurrent Design of Composite Structure and Continuous Toolpath for Additive Manufacturing of Fiber-Reinforced Polymer Composites
1 School of System Design and Intelligent Manufacturing, Southern University of Science and Technology, Shenzhen, 518055, China
2 Institute of High Performance Computing (IHPC), Agency for Science, Technology and Research (A*STAR), 138632, Singapore
* Corresponding Author: Yi Xiong. Email:
The International Conference on Computational & Experimental Engineering and Sciences 2024, 30(1), 1-1. https://doi.org/10.32604/icces.2024.010920
Abstract
The advancement of continuous fiber-reinforced polymer additive manufacturing (CFRP-AM) enables the fabrication of structures with complex geometries and superior properties. However, current design methodologies consider toolpath design and structure optimization as separate stages, with toolpath design typically serving as a post-processing step after structure optimization. This sequential methodology limits the full exploitation of fiber reinforced polymer composites (FRPC) capabilities, particularly in achieving optimal structural integrity and manufacturability. In this paper, a manufacturing-oriented method is proposed for designing continuous FRPC structures, in which the structural layout and continuous fiber toolpaths are simultaneously optimized. The integrated design with manufacturable fiber toolpaths is achieved by a scalar field projection topology optimization (SFPTO) method, where the scalar field projection is used to simulate periodic and continuous toolpaths. Given the scalar field corresponding to the geometry layout and toolpaths, the gradients of the field are formulated as the design variables in a compliance minimization problem and solved with a non-convex gradient-based optimization scheme. The ability of the proposed approach to handle integrated optimization of material densities and continuous toolpaths on both single and multiple load case scenarios is demonstrated. The results show that the proposed approach bridges the gap between structural integrity and precise toolpath planning, providing a comprehensive framework for the concurrent optimization of CFRP-AM.Keywords
Cite This Article
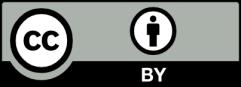
This work is licensed under a Creative Commons Attribution 4.0 International License , which permits unrestricted use, distribution, and reproduction in any medium, provided the original work is properly cited.