Open Access
PROCEEDINGS
The Utilization of Neutron Diffraction and Imaging Characterization Techniques in Engineering Materials
1 China Iron and Steel Research Institute Group, No. 76 Xueyuan South Road, Beijing, 100081, China
2 University of Science and Technology Beijing, No. 30 Xueyuan Road, Beijing, 100083, China
* Corresponding Author: Lixia Yang. Email:
The International Conference on Computational & Experimental Engineering and Sciences 2024, 29(4), 1-2. https://doi.org/10.32604/icces.2024.012690
Abstract
Neutrons possess unique advantages in the study of element and component distribution, internal damage defects, crystal structure, and multi-scale stress field evolution of engineering materials due to their strong penetrating ability, sensitivity to light elements, and non-destructive properties. This study introduces the application of neutron diffraction technology for characterizing residual stress in full-size high-speed iron wheels and neutron imaging technology for three-dimensional characterization of hydrogen distribution in titanium alloys treated with hot hydrogen.Residual stress plays a critical role in the design, manufacturing, assembly, and service life cycle of wheel structures. It is a significant factor that impacts the behavior and fatigue life of wheels. Given the limitations of current methods for characterizing wheel residual stress, such as low spatial resolution and imprecise results, this study utilized China's advanced research reactor engineering stress spectrometer and China's Spallation neutron source engineering material spectrometer. A fully automated multi-degree-of-freedom movement platform was constructed for full-size wheels, and the processing technique of stress-free "benchmark" samples was investigated. A non-destructive characterization technique based on neutron diffraction was developed to assess full-size wheel residual stress. The spatial resolution achieved was ≤3×3×3 mm³ with a measurement depth exceeding 15 mm. This allowed for the determination of residual stress distribution in deep sections of the rim and spoke plate before and after subjecting the wheel to service conditions at speeds up to 350 km/h. The neutron diffraction measurements were validated and complemented by simulation studies, ultrasonic method analysis, X-ray layer-by-layer stripping method examination, as well as contour method evaluation.
As a lightweight and high-strength structural material, titanium alloy holds significant potential for application in the aerospace industry. The utilization of hot hydrogen treatment technology, based on the principles of "hydrogen-induced phase transformation" and "reversible alloying of hydrogen," offers an advanced approach to reconstructing the microstructure of titanium alloys and enhancing their processing and service performance. This technique demonstrates promising prospects in the field of titanium alloy processing and manufacturing. Notably, precise quantitative characterization of hydrogen distribution plays a pivotal role in effectively controlling the microstructure and properties during hot hydrogen treatment. By leveraging China advanced research reactor's neutron imaging spectrometer, a non-destructive three-dimensional quantification technique for hydrogen distribution in titanium alloys has been developed through calibration sample preparation and establishment of a calibration curve for hydrogen content. The detection limit for hydrogen content is below 40 μg/g, with spatial resolution surpassing 50 microns. Consequently, this addresses the challenge associated with lossy data acquisition and accurate quantitative characterization of hydrogen distribution.
Keywords
Cite This Article
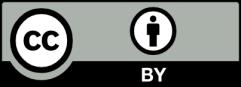
This work is licensed under a Creative Commons Attribution 4.0 International License , which permits unrestricted use, distribution, and reproduction in any medium, provided the original work is properly cited.