Open Access
PROCEEDINGS
Mechanics Model of Face-Core and Inner Core Debonding of Composite Honeycomb Sandwich Structures
1 Center for Composite Materials and Structures, Harbin Institute of Technology, No. 2, Yikuang Street, Xiangfang District, Harbin, 150001, China
* Corresponding Author: Jian Xiong. Email:
The International Conference on Computational & Experimental Engineering and Sciences 2024, 29(4), 1-3. https://doi.org/10.32604/icces.2024.011785
Abstract
Carbon fiber-reinforced plastic (CFRP) composite sandwich structures, due to their excellent mechanical properties and lightweight characteristics, are widely used in aerospace, marine, automotive, and wind turbine blade structures [1]. Different from traditional sandwich structures, composite honeycomb sandwich structures exhibit brittle properties, potentially leading to sudden and catastrophic debonding failure without any warning. Consequently, the interfaces between the face-core and the inner core may become the weakest parts of the structural system.This paper presents a theoretical and experimental investigation into the debonding behavior of the face-core and inner core in composite honeycomb sandwich structures. Based on the principle of minimum potential energy, a mechanics model for debonding between the face-core and the inner core of composite honeycomb sandwich structures is established. The face sheets are modeled using the Timoshenko beam theory, while the equivalent homogeneous orthotropic composite honeycomb core is modeled using the Extended High-Order Sandwich Panel Theory (EHSAPT) [2]. The equivalent mechanical properties of the honeycomb core are obtained through the Gibson homogenization theory [1]. The constitutive relationship at the interfaces between the face-core and the inner core is represented using a nonlinear exponential cohesive zone model [3]. Additionally, the double crack propagation mechanism is introduced to reveal the mechanical mechanisms of the face-core and the inner core debonding, as well as the competition between the two debonding modes.
Subsequently, the composite honeycomb sandwich beam specimens are fabricated in both the L and W directions based on the tailor-folding method [4]. Double cantilever beam (DCB) experiments are then conducted on an INSTRON 3344 testing machine.
By comparing the load-displacement curves and debonding modes, the theoretical results are in agreement with the experimental results, indicating that the established mechanics model can effectively predict the debonding mechanical responses of the composite honeycomb sandwich beams. Finally, a parametric analysis is conducted to investigate the influence of structural dimension parameters, defect location, and defect area on the debonding mechanical responses and modes of the composite honeycomb sandwich beams.
Keywords
Cite This Article
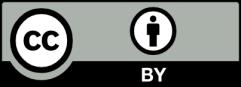
This work is licensed under a Creative Commons Attribution 4.0 International License , which permits unrestricted use, distribution, and reproduction in any medium, provided the original work is properly cited.