Open Access
PROCEEDINGS
Topology Optimization of Mega-Casting Thin-Walled Structures of Vehicle Body with Stiffness Objective and Process Filling Constraints
1 National Engineering Research Centre for Electric Vehicles, Beijing Institute of Technology, Beijing, 100081, China
* Corresponding Author: Yingchun Bai. Email:
The International Conference on Computational & Experimental Engineering and Sciences 2024, 29(3), 1-2. https://doi.org/10.32604/icces.2024.011393
Abstract
Mega-casting techniques are widely used to manufacture large piece of thin-walled structures for vehicle body in Automotive industries, especially with the rapid growing electric vehicle market. Topology optimization is effective design method to reach higher mechanical performance yet lightweight potential for casting structures [1-3]. Most of existing works is focused on geometric-type casting constraints such as drawn angle, partion line, undercut, and enclose holes. However, the challenges in mega-casting arise from the complexities in the casting process such as filling and solidification, and the corresponding defects have larger influences on the structural performances [4-6]. Partial consideration of the complicated filling process constraints in topology optimization can generate designs with more balance between the mechanical performance and process feasibilities. In this work, a topology optimization approach is developed for the design of mega-casting thin-walled structures of vehicle body with stiffness objective and process filling constraints [7,8]. Fundamental topology description model and corresponding material interpolation model is built for both the structural evaluation and fluidic filling process within the densify framework. The casting filling process is simulated in combination with S-A (Spalart-Allmaras) turbulent flow model for more accurate solutions [9]. Adjoint sensitivity method is used for both structural analysis and filling analysis, and MMA is used to update the topology [10]. The algorithm is coded in combination with the Open Field Operation and Manipulation (OpenFOAM) library. Two numerical examples are presented to demonstrate the effectiveness and robustness.Keywords
Cite This Article
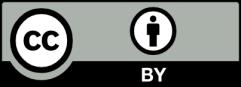
This work is licensed under a Creative Commons Attribution 4.0 International License , which permits unrestricted use, distribution, and reproduction in any medium, provided the original work is properly cited.