Open Access
PROCEEDINGS
Concurrent Topology Optimization of Shell Structures with Multi-Configuration and Variable-Density Infill
1 National Engineering Research Centre for Electric Vehicles, Beijing Institute of Technology, Beijing, 100081, China
* Corresponding Author: Yingchun Bai. Email:
The International Conference on Computational & Experimental Engineering and Sciences 2024, 29(3), 1-2. https://doi.org/10.32604/icces.2024.011338
Abstract
The superior stiffness-to-weight and strength-to-weight mechanical advantages of shell-infill structures can be fully exploited through concurrent design of the entire topology and infill configuration. This inherent design freedom can be guaranteed by additive manufacturing, through which complicated geometry can be fabricated. The existing approaches are typically focused on topology optimization with porous infill [1-3], un-prescribed lattice configuration with uniform density [4-8], or prescribed single lattice configuration with non-uniform density [9-10]. Towards higher performance yet lightweight, this work proposes a concurrent topology optimization approach to directly generate shell-infill structures in which the inner infill consists of multi-configuration and variable-density lattices. This proposed approach will update the entire topology, infill configuration, and lattice diameter simultaneously. Mathematically, it is an optimization problem with continuous and discrete variables in the base model. To improve the material property prediction efficiency for the infills, the multi-response latent-variable Gaussian process (MR-LVGP) [11] is utilized to establish a surrogate model for the lattice equivalent elastic tensor and its structure through two design variable fields, including topology density variables and continuous latent variables projected from infill configuration variables. As for the feature description, the double smoothing and projection (DSP) [9] method is employed for strict separation between the void, infill and shell domain. A concurrent topology design problem with topology density variable and transformed infill configuration variables is formulated in combination with the shell-infill type material interpolation model, which is solved through MMA efficiently. To improve the optimization accuracy, the following topology optimization is conducted with pure topology density variable is performed due to the deviation from the optimized continuous latent variables to the corresponding infill configuration. Several numerical examples are systematically investigated to demonstrate the effectiveness of the proposed method.Keywords
Cite This Article
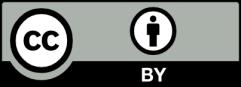
This work is licensed under a Creative Commons Attribution 4.0 International License , which permits unrestricted use, distribution, and reproduction in any medium, provided the original work is properly cited.