Open Access
PROCEEDINGS
Equivalent Elastic-Plastic Model of BCC Lattice Structures
1 Peking University, Haidian District 5 Yiheyuan Rd, Beijing, 100871, China
* Corresponding Author: Moubin Liu. Email:
The International Conference on Computational & Experimental Engineering and Sciences 2024, 29(2), 1-2. https://doi.org/10.32604/icces.2024.012192
Abstract
The lattice architecture, characterized by its methodical arrangement of repetitive units, exhibits compactness, uniformity, and lightweight properties. In additive manufacturing, such structures are widely utilized in support structures and internal fillings, playing a significant role in improving manufacturing efficiency and optimizing structural performance [1,2]. However, due to the complex microstructure of lattice materials, it is challenging to describe them using refined finite element models. The development of an equivalent performance model for these materials, employing a periodic single cell to represent the internal architecture for the comprehensive lattice system, can significantly improve computational efficiency and provide an effective method for supporting system optimization. Extensive study efforts have been dedicated to the equivalent performance calculation of lattice structures, predominantly focusing on the prediction of equivalent elastic and thermodynamic performances [3,4]. Given the substantially reduced stiffness of lattice structures in comparison to solid materials of analogous dimensions, the equivalent elastic limit of their surrogate models is markedly lower than the inherent elastic limit of the materials themselves. During the additive manufacturing process, areas proximal to the lattice support are often subjected to considerable cyclic thermal deformation, rendering the internal lattice material susceptible to plastic deformation. Hence, when deploying a single-cell equivalent performance surrogate model, it is imperative to calibrate the equivalent stress-strain curve based on the lattice configuration. This study establish a single-cell equivalent performance surrogate model for the Body-Centered Cubic (BCC) lattice structure. Through finite element analysis, it derives the equivalent stress-strain curves under various parametric conditions, elucidating the influence trends of different design parameters on the elastic-plastic transformations of the BCC lattice. This facilitates the provision of tailored recommendations for the lattice's optimization design. The research encapsulated in this manuscript introduces a parameter-driven, single-cell performance model for the BCC lattice structure, aimed at amplifying the simulation velocity of additive manufacturing models, elevating the precision of structural deformation predictions, and furnishing critical support for manufacturing process optimization.Keywords
Cite This Article
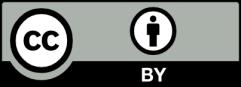
This work is licensed under a Creative Commons Attribution 4.0 International License , which permits unrestricted use, distribution, and reproduction in any medium, provided the original work is properly cited.