Open Access
PROCEEDINGS
Investigation on Microscopic Properties of Copper Concentrate Particles by Combining Experiments and DEM Modelling
1 School of Energy Science and Engineering, Central South University, Changsha, 410083, China
* Corresponding Author: Zhuo Chen. Email:
The International Conference on Computational & Experimental Engineering and Sciences 2024, 29(2), 1-4. https://doi.org/10.32604/icces.2024.011777
Abstract
1 General introductionThe flash smelting is one of the dominant technologies for copper matte production. To meet the increasing demand, the production capability of flash smelting furnace has been increased several times. However, under current conditions, the segregation of concentrate particles becomes an escalating issue, impacting production efficiency and safety [1]. The DEM modelling is a powerful tool for investigating particle behaviors such as contact and collision, but the lack of accurate microscopic properties of copper concentrate particles makes it challenging to conduct reliable DEM simulations [2]. To address this gap, this study employs both experimental and numerical methods to jointly calibrate the particle parameters required for DEM. These calibrated parameters are then used to simulate particle segregation behavior, validating their effectiveness in DEM modelling.
2 Methodology
2.1 Test object
The copper concentrate particles used as the test object were sampled from the metallurgical plant. The sampled particles are then used in experimental calibrations, including bulk density, elastic moduli, restitution coefficient, etc. The particle size distribution (PSD) is tested by the laser particle size analyzer, as shown in Fig. 1a. In the DEM simulation, the PSD is simplified into four groups of size as shown in Fig. 1b, to save computational resources.

2.2 Experimental methods
The joint calibration aims at the parameters that are difficult to ascertain directly from experiments. The other easily accessible properties are directly determined from universal tests (standards) [3,4] or reported experiments [5-7], providing the necessary basis for the joint calibration. These calibrated properties and correspondingly applied methods are listed in Table 1.

2.3 Joint calibration method
The calibration of the rolling friction coefficient utilizes the joint method, as illustrated in Fig. 2. In this study, two rolling friction coefficients are set to be unknown factors, and the obtained static friction coefficient is also regarded as the unknown factor due to the requirement of Box-Behnken Design (BBD). The repose angle in the pilling process is used as the target value. Through the BBD, fifteen sets of assumed parameters are determined for DEM modelling to obtain target values. Subsequently, a regression equation can be established to connect factors with the target value. Then, the insignificant terms are dropped after the significance test to obtain the optimal regression equation. Finally, along with the known factor C, the true value of unknown factors can be retracted from the equation by introducing the experimental value of the repose angle. Additionally, the DEM simulation is performed through the open-source software LIGGGHTS® with the Hertz-Mindlin model for validation.

3 Results and discussion
3.1 Experimental results
The microscopic properties determined by experiments are summarized in Table 2. The standard deviations (SDs) and coefficient of variations (CVs) are listed as well. It can be found that both the SDs and CVs are low enough for multiple-time experiments, which guarantees the results with accuracy.

3.2 Joint calibration results
Through the Pearson test, the optimal regression equation is obtained by dropping the insignificant terms from the original equation, as shown in Eq. (1). The original and optimal regression models are evaluated through the analysis of variance, as compared in Table 3. The indices after optimization show better accuracy.

where θ represents the repose angle, A and B are the coefficients of rolling friction between particle-particle (p-p) and particle-wall (p-w), respectively, and C is the coefficient of static friction between p-p.

As the optimized regression equation is determined, the rolling friction coefficients can be calculated according to Eq. (1). In experiments, the repose angle and static friction coefficient are determined as 32.16° and 0.503, respectively. The obtained coefficients of rolling friction between p-p and p-w are 0.0629, and 0.0762, respectively.
3.3 DEM validation
The determined microscopic properties of copper concentrate particles are used for DEM modelling to make validation. The DEM modelling includes two parts, i.e., the particle pouring process and the segregation in the feeding chute, which are validated from the repose angle and segregation coefficient, respectively. The results are shown in Fig. 3 and Table 4, which report low relative errors.

4 Conclusions
Multiple experiments and DEM modelling are applied jointly to obtain the microscopic properties of copper concentrate particles, which provides a solid basis for further DEM investigation of the flash smelting process. The calibrated parameters are used in the DEM modelling. The numerical results are validated against the experiments, showing good agreement.
Keywords
Cite This Article
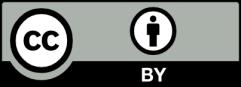
This work is licensed under a Creative Commons Attribution 4.0 International License , which permits unrestricted use, distribution, and reproduction in any medium, provided the original work is properly cited.