Open Access
PROCEEDINGS
Elastically Isotropic Open-Cell Lattice Metamaterials with Superior Stiffness
1 Department of Mechanical and Automation Engineering, Chinese University of Hong Kong, Sha Tin, Hong Kong, China
2 Meta Robotics Institute, Shanghai Jiao Tong University, Shanghai, 200240, China
3 State Key Laboratory of Mechanical System and Vibration, Shanghai Jiao Tong University, Shanghai, 200240, China
4 School of Engineering, Great Bay University, Songshan Lake, Dongguan, 523808, China
* Corresponding Authors: Xu Song; Michael Yu Wang. Email: ;
The International Conference on Computational & Experimental Engineering and Sciences 2024, 29(2), 1-1. https://doi.org/10.32604/icces.2024.011319
Abstract
Elastically isotropic open-cell lattice metamaterials exhibit identical elastic properties along arbitrary directions, and are ideal candidates for applications with unknown primary loading directions. Their open-cell properties are preferred for additive manufacturing processes and multifunctional applications requiring mass and heat transfer. This presentation focuses on the design, simulation, fabrication, and experimental tests of elastically isotropic open-cell lattice metamaterials with superior stiffness. First, a family of elastically isotropic truss lattices are analytically devised through combining elementary cubic lattices with contrary elastic anisotropy. The proposed stretching-dominated truss lattices can reach nearly 1/3 of the Hashin-Shtrikman upper bounds at low relative densities. Next, two shape optimization approaches are proposed to devise elastically isotropic open-cell shell lattices to achieve more exceptional stiffness, including variable thickness design with triply periodic minimal surface maintained as the mid-surface, and uniform thickness design with optimized mid-surface shape. The optimized shell lattices exhibit superior stiffness and significantly outperform elastically isotropic truss lattices of equal relative densities. The selected uniform and variable thickness N14 lattices are fabricated by micro laser powder bed fusion (µLPBF) in stainless steel 316 L (SS316L) for experimental tests, demonstrating that the elastic anisotropy of variable thickness N14 lattices is reduced compared to that of uniform ones, while the anisotropy of SS316L materials leads to non-negligible errors between experimental and numerical results. Afterwards, the process-induced anisotropy of SS316L materials is further introduced into the design framework to achieve a better accuracy of the design and analysis model. The transversely isotropic elasticity model is used to characterize the µLPBF process-induced anisotropic elasticity of SS316L. The designed lattices from anisotropic materials achieve better agreements to design targets than those designed from isotropic materials, thereby validating the superiority of the proposed design method. The selected variable thickness N14 lattices are fabricated via µLPBF in SS316L for experimental tests, demonstrating that their anisotropic elasticity is further reduced compared to that of uniform/variable thickness samples designed from isotropic constitutive materials. Overall, these studies deliver effective guidelines for the design of elastically isotropic open-cell lattice metamaterials with superior stiffness for multifunctional real-world applications.Keywords
Cite This Article
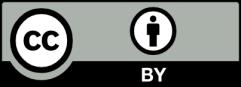
This work is licensed under a Creative Commons Attribution 4.0 International License , which permits unrestricted use, distribution, and reproduction in any medium, provided the original work is properly cited.