Open Access
PROCEEDINGS
Macroscopic Deflections of Fatigue Crack in Direct Energy Deposited Ti–5Al–5Mo–5V–1Cr–1Fe
1 Hangzhou International Innovation Institute, Beihang University, 166 Shuanghongqiao Street, Pingyao Town, Yuhang District, Hangzhou, 311115, China
2 School of Aeronautic Science and Engineering, Beihang University, Xueyuan Road, Haidian District, Beijing, 100191, China
* Corresponding Author: Binchao Liu. Email:
The International Conference on Computational & Experimental Engineering and Sciences 2024, 29(1), 1-1. https://doi.org/10.32604/icces.2024.011835
Abstract
With the everlasting pursuit for weight reduction, efforts are devoted to applying additively manufactured (AM) structures in aeronautic vehicles; however, anomalous fatigue crack growth (FCG) behaviors, such as deflection and branching, are recently observed in macroscale, which deviates from the predictions by classic fracture mechanics. In this work, FCG behaviors of direct energy deposited (DED) Ti–5Al–5Mo–5V–1Cr–1Fe (TC18 in China) are investigated, in which fatigue crack deflections induced by combined impacts of loading and microstructures are revealed. Experiment results show that cracks are more deflected in columnar grains due to the preferred distribution of acicular a phase in direction, and the effects of microstructure gradient due to solidification rate gradient by AM processing in thickness direction prove to be remarkable. On this basis, the model of net driving force is proposed to explain crack deflection, i.e. FCG behaviors are driven by loading and resisted by material. Such model is then verified by peridynamic (PD) simulations and crack deflection behaviors are well captured; to be specific, directional material resistance to cracking is described as anisotropic critical bond stretch (CBS), while fatigue damage by cyclic loading is described by CBS degradation. This work can not only enrich the present FCG analysis methods based on assumptions of heterogeneity and isotropy, but also support the damage tolerance evaluations on high-performance lightweight aircraft metallic structures.Keywords
Cite This Article
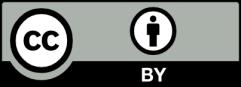
This work is licensed under a Creative Commons Attribution 4.0 International License , which permits unrestricted use, distribution, and reproduction in any medium, provided the original work is properly cited.