Open Access
PROCEEDINGS
Prediction of Ductile Fracture for Ti-6Al-4V Alloy Fabricated by L-PBF Based on Unit Cell Calculations
1 School of Aeronautics, Northwestern Polytechnical University, Xi’an, 710072, China
* Corresponding Author: Wei Huang. Email:
The International Conference on Computational & Experimental Engineering and Sciences 2023, 27(4), 1-2. https://doi.org/10.32604/icces.2023.010553
Abstract
Additive manufacturing of metallic components can result in initial defects that significantly reduce their mechanical properties [1]. Therefore, there has been considerable interest in studying the fracture and damage behavior of such components through theoretical and experimental studies [2, 3]. Developing a reliable model for predicting the ductile fracture of additively manufactured components is currently of great importance. In this study, we conducted unit cell calculations with the calibration of experimental tests to investigate the ductile fracture of Ti-6Al-4V alloy fabricated through additive manufacturing. The stress triaxiality and Lode parameter were enforced constant for the voided cubic unit cell model during the loading. An energy-based criterion was employed to identify the onset of void coalescence [4, 5], and the macroscopic effective strain corresponding to the minimum value of the energy work ratio was considered as the failure strain for a certain stress state. We determined the initial void fraction of the unit cell by conducting tensile tests on a series of specimens with different notch radii, which provided several different stress states. Note that finite element analysis was used to calibrate the internal parameters of specimens, such as the distribution of stress states and effective strain [6]. Our proposed unit cell model successfully predicted the failure strain for Ti-6Al-4V alloy fabricated by L-PBF under different stress states, and the test results confirmed its accuracy. Our study provides valuable insights for designing and applying metallic additive manufacturing in the future.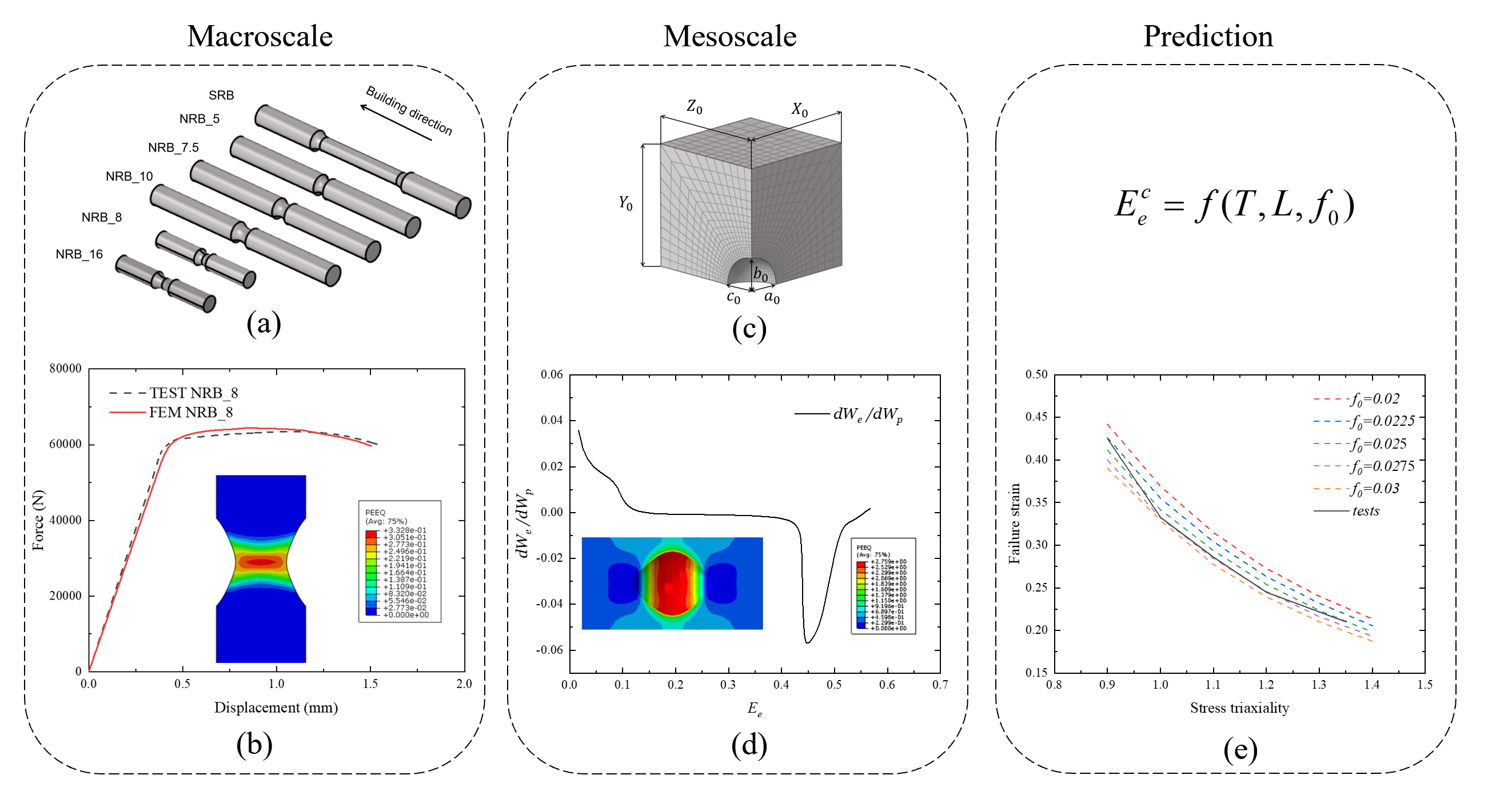
The specimens used in this study are shown in Fig. (a) The different geometries of notched specimens provide a series of stress states. The finite element analysis results fit well with the experimental data are shown in Fig. (b) Note that the inside parameters of specimens are obtained from numerical simulation. The unit cell model and the energy work rate ratio are depicted in Fig. (c) and Fig. (d), respectively, where the effective plastic deformation distribution also presented. In this study, the failure strain is considered as the function of stress triaxiality, Lode parameter and initial void fraction for unit cell calculation. Fig. (e) shows the failure strain from obtained both unit cell calculations and experimental tests under different stress states, indicating the high accuracy of the unit cell calculation in predicting ductile fracture of additively manufactured Ti-6Al-4V alloy.
Keywords
Cite This Article
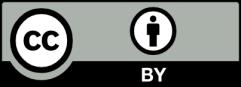
This work is licensed under a Creative Commons Attribution 4.0 International License , which permits unrestricted use, distribution, and reproduction in any medium, provided the original work is properly cited.