Open Access
PROCEEDINGS
Effects of Friction and Strain Hardening on ELS Mode II Interlaminar Fracture Test
1 School of Aeronautics and Astronautics, Shanghai Jiao Tong University, Shanghai 200240, China
* Corresponding Author: Wu Xu. Email:
The International Conference on Computational & Experimental Engineering and Sciences 2023, 27(4), 1-2. https://doi.org/10.32604/icces.2023.09634
Abstract
Accurate determination of the interlaminar mode II fracture toughness is much more difficult than that of mode I delamination, due to friction and crack closure. In this paper, A-scan is used to measure the crack growth length of end-loaded split (ELS) test through cyclic unloading and reloading. Interesting hysteresis loops are observed in the experimental load-displacement curve, which has not been fully understood by the existing literature. The frictional effect from the load fixture is analytically determined and numerically validated. It absorbs considerable energy during the creation of new crack surface, but has been overlooked. A simple method is proposed to determine the frictional coefficient and effect. To reduce the frictional effect, a new load fixture is proposed and validated by finite element analysis. The hysteresis loop is found to be caused by the friction and strain hardening during cyclic loading.The load-displacement relationship from the ELS test is depicted in Fig.1. A single loop of the loaddisplacement represents a loading and unloading cycle. Stable crack growths are observed from the first and subsequent circles. A small amount of crack growth is observed in each loading and unloading cycle. The crack lengths are measured using A-scan after the finish of each unloading procedure. The crack lengths are also given in Fig.1.
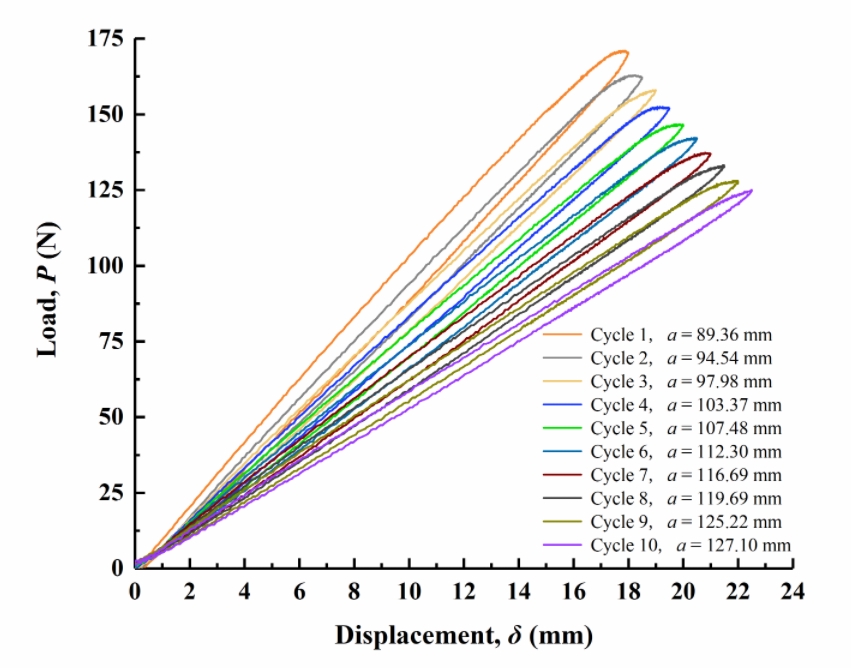
Figure 1: Load-displacement relationship obtained from the ELS test subjected to 10 loading and unloading cycles
There are two interesting phenomena observed from the load-displacement curve shown in Fig.1. One is a hysteresis loop observed between two adjacent unloading and loading sequences. The other is the obvious difference in the maximum loads of two adjacent unloading and reloading sequences.
In this paper, the load-displacement relationship and strain energy release rate of ELS test are quantitatively given by combining beam theory with finite element analysis. The reason why hysteresis loops exists and load values discontinue in Fig.1 is revealed by theoretical and numerical simulation.
Fig.2 shows the analysis curve of ELS load-displacement relationship considering the effect of friction and strain hardening at the crack tip under loading and unloading. It can be seen from the analysis results that the friction between cracks and clamps will cause obvious hysteresis loops in the loading and unloading process, and the maximum load after unloading does not coincide with the load during unloading, which agree well with the experiment as shown in Fig.1. On this basis, the interlaminar fracture toughness R curve considering the effect of friction is obtained.
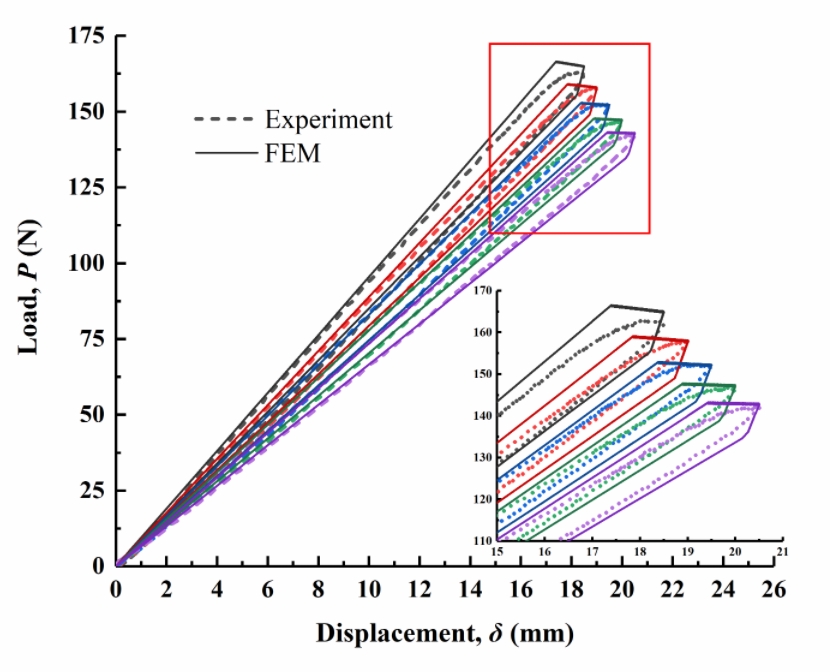
Figure 2: Load-displacement relationship obtained from FEM
Keywords
Cite This Article
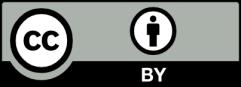
This work is licensed under a Creative Commons Attribution 4.0 International License , which permits unrestricted use, distribution, and reproduction in any medium, provided the original work is properly cited.