Open Access
PROCEEDINGS
Comprehensive Simulation of Hot Shape Rolling by Considering the Casting Defects
1 Institute of Metals and Technology, Lepi pot 11, Ljubljana, SI-1000, Slovenia
2 University of Ljubljana, Faculty of Mechanical Engineering, Aškerčeva 6, Ljubljana, SI-1000, Slovenia
* Corresponding Author: Umut Hanoglu. Email:
The International Conference on Computational & Experimental Engineering and Sciences 2023, 27(2), 1-1. https://doi.org/10.32604/icces.2023.09610
Abstract
In this research, a rolling simulation system based on a novel meshless solution procedure is upgraded considering casting defects in the material model. The improved model can predict the final stage of the defects after multi-pass rolling. The casted steel billet that enters the rolling mill arrives with casting defects. Those defects may be porosity due to the shrinkage and cavity or micro-cracks near the surface due to hot tearing. In this work, porosity is considered the main defect source since it can easily be determined experimentally. The damage theory develops a damaged stiffness matrix with a scalar damage value. The damage value is obtained at different compression stages based on our thermo-mechanical experiments using steel samples from continuous casting that contain defects. The damage values of each sample is obtained by accurately measuring its density with Archimedes’ technique. Multiple samples from the different sections of a casted billet C45 are put on compression tests to obtain the evolution of the damage. The experimental results are then mapped into the damage model and used in the simulations with actual rolling schedules considering different casting defects. The thermo-mechanical solution of the ideal plastic model is achieved by using the meshless local radial basis function collocation method. Sensitivity studies are made with different roll pass designs, and damage evolution is observed based on our numerical model. By definition, damage value increases with the increasing strains. However, this rare study shows that porosities might even disappear with the proper roll pass design.Keywords
Cite This Article
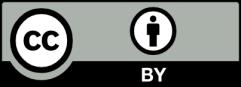
This work is licensed under a Creative Commons Attribution 4.0 International License , which permits unrestricted use, distribution, and reproduction in any medium, provided the original work is properly cited.