Open Access
PROCEEDINGS
Multiscale Modeling for Thermomenchanical Fatigue Damage Analysis and Life Prediction for Woven Ceramic Matrix Composites at Elevated Temperature
1 Institute of Mechanics, Chinese Academy of Sciences, Beijing, 100190, China
2 Institute for Aero engine, Tsinghua University, Beijing, 100084, China
3 Department of Mechanical Engineering, University of Bath, Bath, BA2 7AY, UK
4 Aero Engine Academy of China, Aero Engine (Group) Corporation of China, Beijing, 100097, China
* Corresponding Author: Zhengmao Yang. Email:
The International Conference on Computational & Experimental Engineering and Sciences 2023, 26(4), 1-1. https://doi.org/10.32604/icces.2023.09229
Abstract
Woven ceramic matrix composites (CMCs), exhibiting excellent thermomechanical properties at high temperatures, are promising as alternative materials to the conventional nickel-based superalloys in the hot section components of aero-engines. Therefore, understanding and predicting the lifetime of CMCs is critical. Fatigue prediction of woven CMCs currently involves long-term and costly testing. A feasible alternative is to use predictive modelling based on a deep understanding of the damage mechanisms. Therefore, this study develops a multiscale analysis modelling method for predicting the fatigue life of CMC materials at high temperature by investigating the thermomechanical fatigue damage evolution. To represent the global thermomechanical properties of a composite structure, a repeat unit cell (RUC) of woven composites is proposed. The RUC integrates a micromechanics model and a shear-lag model with a statistical model to predict the damage evolution and fatigue life of the composite structures. The present methodology defines global structure failure as the degradation of thermomechanical properties of the RUC caused by constituent failures and nonlinear material properties in the RUC. The elastic modulus evolution is used to determine material failure, which can affect the thermomechanical properties of the RUC. The methodology is evaluated using the experimental test performed on woven SiC/SiC CMC with an environmental barrier coating.Cite This Article
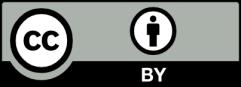
This work is licensed under a Creative Commons Attribution 4.0 International License , which permits unrestricted use, distribution, and reproduction in any medium, provided the original work is properly cited.