Open Access
PROCEEDINGS
TPMS-Based Topology Optimization Design with Multiple Materials via MMC Method
1 National Engineering Research Center of Novel Equipment for Polymer Processing, the Key Laboratory of Polymer
Processing Engineering of the Ministry of Education, Guangdong Provincial Key Laboratory of Technique and Equipment
for Macromolecular Advanced Manufacturing, South China University of Technology, Guangzhou, 510641, China
2 Department of Mechanical Engineering, Northwestern University, Evanston, 60208, USA
3 State Key Laboratory of Digital Manufacturing Equipment and Technology, Huazhong University of Science and
Technology, Wuhan, 430074, China
* Corresponding Author: Yingjun Wang. Email:
The International Conference on Computational & Experimental Engineering and Sciences 2023, 26(2), 1-2. https://doi.org/10.32604/icces.2023.09085
Abstract
Topology optimization (TO) designs involving multiple materials suffer either difficult interface modeling or finding physically meaningful transition domains with an accurate structural representation. Simple interpolation approaches are usually used in multi-material designs to represent the overlapped regions of different materials, which cannot solve either of these problems. In this paper, a moving morphable component (MMC)-based TO is developed to overcome this issue by leveraging the triply periodic minimal surfaces (TPMS). The TMPS-based architecture will serve as the infilling microstructure to accurately represent the overlapped domains of different materials. A TPMS function interpolation scheme is used to generate new microstructures for the overlapped region, which allows a direct combination of the topology description for multiple architected materials and the configuration of the composed TPMSs. The properties of the new microstructures are consistent with material properties of overlapped regions. The proposed method reaches the effect that the TPMS microstructure of the overlapping regions can always be well defined and unambiguously represented during the TO. Three numerical examples and a 3D printing model of an optimized geometry are reported to demonstrate the effectiveness and efficiency of the proposed approach. An engineering case is presented to verify the applicability of the proposed method in practical engineering. Comparing to conventional methods, the proposed method is capable to generate exact microstructures with equivalent properties in overlapped regions, which successfully facilitates manufacturing and avoids the discontinuity and high stress concentrations caused by the microstructure mismatch in conventional methods.Keywords
Cite This Article
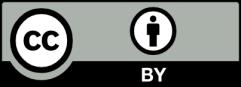
This work is licensed under a Creative Commons Attribution 4.0 International License , which permits unrestricted use, distribution, and reproduction in any medium, provided the original work is properly cited.