Open Access
PROCEEDINGS
Data-Driven Enhanced Combined Finite-Discrete Element Method for Simulating Rock Failure Progress
1 School of Civil Engineering, Wuhan University, Wuhan, 430072, China
* Corresponding Author: Zhijun Wu. Email:
The International Conference on Computational & Experimental Engineering and Sciences 2023, 25(1), 1-2. https://doi.org/10.32604/icces.2023.09814
Abstract
The combined finite-discrete element method (FDEM) can effectively simulate the continuousdiscontinuous failure process of rocks, and is now widely adopted to investigate the issues related to rock mechanics and engineering. The conventional FDEM requires pre-defines constitutive models to calculate the element stress from element deformations [1]. However, the constitutive model used in conventional FDEM is obtained by empirical fitting of rock mechanics test data, and large amount of rock physical and mechanical information present in the test data, such as the nonlinear properties of rock presented in the initial compaction stage, are lost in the process of fitting test data [2]. Thus, there are discrepancies between the numerically reproduced rock mechanical behaviors and rock mechanical behaviors in laboratory tests. Inspired by the concepts of data-driven computational mechanics [3, 4], to reduce the discrepancies coming with conventional constitutive model, a data-driven combined finite-discrete element method (DDFDEM) is proposed to update elements stress directly through laboratory test data rather than through conventional constitutive models of FDEM. In this newly proposed DDFDEM, a data-driven solver is first introduced to directly obtains the stress state of finite elements by searching material point from a prespecified data set that is closest to satisfying the conservation laws. Then, a new nodal force update algorithm for joint elements is proposed to mitigate the error accumulation effect during the k-d tree searching. After that, a multi-density data sets generator is proposed to improve the computing efficiency with little loss of precision. After the above improvements, the convergence and accuracy of DDFDEM in predicting the failure process of rock is validated by conducting several examples, including the static equilibrium of plate tensile test, uniaxial compressive strength test and Brazilian disk test. And the above validation results also show that DDFDEM can accurately simulate the rock fracture process while retaining information lost by conventional FDEM with constitutive model, such as the nonlinear elastic deformation of rock in the initial compaction stage.Keywords
Cite This Article
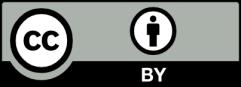
This work is licensed under a Creative Commons Attribution 4.0 International License , which permits unrestricted use, distribution, and reproduction in any medium, provided the original work is properly cited.