Open Access
PROCEEDINGS
High Strain Rate Behavior of Harmonic Structure Designed Pure Nickel: Mechanical Characterization, Microstructure Analysis and Modelisation
1 Université de technologie de Compiègne, CNRS, Roberval (Mechanics, energy and electricity), Centre de
recherche de Royalieu, Compiègne cedex, 60203, France
2 Thiot Ingenierie, Puybrun, 46130, France
3 Université Sorbonne Paris Nord, Laboratoire des Sciences de Procédés et des Matériaux (UPR 3407),
Villetaneuse, 93430, France
4 College of Science and Engineering, Ritsumeikan University, 1-1-1 Noji-Higashi,Kusatsu Shiga 525-8577, Japan
* Corresponding Author: Daniel Varadaradjou. Email:
The International Conference on Computational & Experimental Engineering and Sciences 2022, 24(1), 1-3. https://doi.org/10.32604/icces.2022.08673
Abstract
The development of new architecture metallic alloys with controlled microstructures is one of the strategic ways for designing materials with high innovation potential and, particularly with improved mechanical properties as required for structural materials [1]. Indeed, unlike conventional counterparts, metallic materials having so-called harmonic structure displays strength and ductility synergy. The latter occurs due to a unique microstructure design: a coarse grain structure surrounded by a 3D continuous network of ultra-fine grain known as “core” and “shell”, respectively. In the present study, pure harmonic-structured (HS) Nickel samples were processed via controlled mechanical milling and followed by spark plasma sintering (SPS), detailed in previous work [2].In previous studies, the mechanical behavior under quasi-static loading at room temperature has been evaluated and showed the superior mechanical properties of HS pure Ni over the homogeneous conventional counterpart [3]. The present work aims at characterizing the mechanical properties of HS pure Ni under room temperature dynamic loading, through a Split Hopkinson Pressure Bar (SHPB) test, and the underlying microstructure evolution. A stopper ring was used to maintain the strain at a fixed value of about 20% (Fig. 1). Five samples (named B1 to B5) were impacted using different striker bar velocity (V0) from 14 m/s to 28 m/s, yielding strain rate in the range 4000-7000 s-1. Results were considered until a 10% deformation value, which is the deformation threshold for the constant strain rate assumption [4].
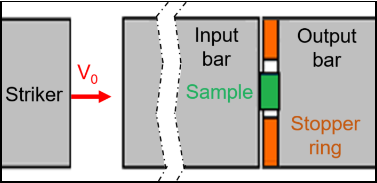
Figure 1: SHPB test mounting with a stopper ring
The evolution flow stress with the strain rate for harmonic and conventional structure (CS) (using data from quasi-static and high rate experiments) makes it possible to identify two domains with a transition around 3000 s-1. First domain operating at low deformation rates is conventionally associated with the thermal activated movement of dislocation, whereas the second domain at high strain rates is associated with viscous drag.
The non-deformed (INIT), and post-SHPB microstructure (B1 to B5), were investigated by EBSD (Fig. 2) and show that while strain rate increase, grains size within the core decrease. An in-depth analysis of grains and grain boundaries were made to highlight the thermal (such as dynamic recrystallization) or mechanical (such as grains fragmentation by dislocation) contribution within the “core” and “shell”.

Figure 2: Cross section EBSD map of the initial sample from post-SPS process (INIT)
One of the most widely used methods for determining dynamic behavior of materials is the SHPB technique developed by Kolsky [6]. A 3D simulation of SHPB test was created through ABAQUS in dynamic explicit. This 3D simulation allow taking into account all modes of vibration. An inverse approach was used to identify the material parameters from the equation of Johnson-Cook (JC) by minimizing the difference between the numerical and experimental data. The JC’s parameters were identified using B1 and B5 samples configuration. Predictively, identified parameters of JC’s equation shows good result for the others sample configuration (Fig. 3)
(a)

(b)
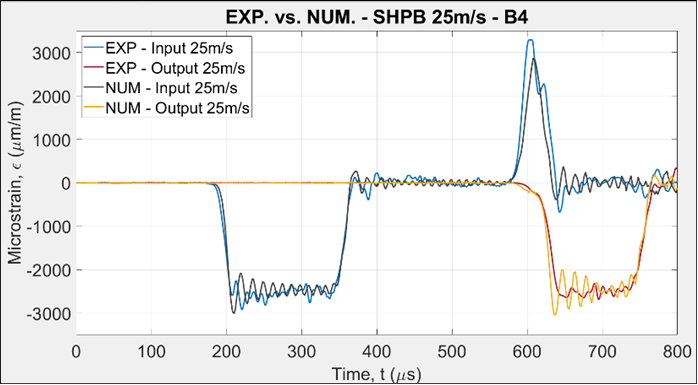
Figure 3: 3D simulation assembly of SHPB test from ABAQUS (a) and output data of SHPB test from experiment and numerical test for the sample B4 (b)
Furthermore, mean rise of temperature within the harmonic Nickel sample can be obtained through ABAQUS and show an elevation of about 35°C for all fives sample. At this temperature, thermal mechanism cannot be activated. Therefore, grains fragmentation within the core is mainly due to mechanical phenomena for a fixed final strain of 20%
Keywords
Cite This Article
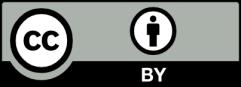
This work is licensed under a Creative Commons Attribution 4.0 International License , which permits unrestricted use, distribution, and reproduction in any medium, provided the original work is properly cited.