Open Access
ABSTRACT
Prediction Model for Weld Hydrogen Cracking in High Strength Steel Weld
* Corresponding Author: Nobuyuki Ishikawa. Email: .
The International Conference on Computational & Experimental Engineering and Sciences 2019, 22(2), 138-138. https://doi.org/10.32604/icces.2019.05518
Abstract
Prediction model for weld hydrogen cracking (so called cold cracking) in high strength steel weld was developed by a coupled thermo-elastic-plastic and hydrogen diffusion analysis in the y-grooved weld joint. Critical conditions of cracking was given as the function of principal stress and accumulated hydrogen concentration in the root region where the cracking occurs. In order to clarify the critical conditions of cold cracking, y-grooved cold cracking tests were first conducted using the steel plate with tensile strength level of 780MPa. Plate thickness of the plates were 25 mm and 50 mm. Hydrogen concentration in the weld metal was changed by applying hydrogen into the shield gas in the gas-metal arc welding (GMAW), and different pre-heating conditions were applied to evaluate the critical pre-heating temperature to prevent cold cracking. It was found that the critical pre-heating temperature was increased with thicker plate thickness and higher hydrogen concentration in the weld metal. The cracks were initiated at the weld metal in the root region which exhibits significant tensile residual stress by the welding. Hydrogen accumulation into the root region may have enhanced cracking. Based on the above y-grooved weld cold cracking tests, a simulation model for estimating the critical pre-heating temperature was developed. The y-grooved weld joints with different plate thickness were modeled by the FEM with the actual weld configuration and material properties in the base metal, heat affected zone (HAZ) and weld metal. Hydrogen was put in the weld metal as an initial condition, then welding simulation was conducted by coupled thermo-elastic-plastic and hydrogen diffusion analysis. In the hydrogen diffusion analysis, the α-multiplication method, which stress gradient term in the diffusion law was multiplied, was applied to express realistic hydrogen diffusion enhanced by hydrostatic stress field. Hydrogen accumulation occurred in the root region where showed highest hydrostatic stress. The point where showed the hydrogen accumulation was well corresponded to the crack initiation site. It was found that cracking was enhanced with thicker plate and higher initial hydrogen concentration because of higher tensile residual stress and higher hydrogen accumulation in the root region, respectively. These models were implemented into the Materials Integration (MI) System to estimate the critical pre-heating temperature in the y-grooved weld tests with different welding conditions. Although, further validation and optimization are needed for the models, this hydrogen cracking prediction system has a lot of potential as a material development support tool for reducing experimentation and speeding up the development.Cite This Article
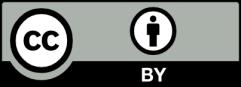
This work is licensed under a Creative Commons Attribution 4.0 International License , which permits unrestricted use, distribution, and reproduction in any medium, provided the original work is properly cited.