Open Access
ABSTRACT
In Situ Microscopic Observation and Crystal Plasticity Simulation of Fatigue Crack Formation in Ti-6Al-4V Alloy
Department of Materials Engineering, The University of Tokyo, 7-3-1 Hongo, Bunkyo-ku, Tokyo, Japan.
*Corresponding Author: Fabien Briffod. Email: .u-tokyo.ac.jp.
The International Conference on Computational & Experimental Engineering and Sciences 2019, 22(2), 125-125. https://doi.org/10.32604/icces.2019.05319
Abstract
The fatigue behavior of metallic materials is a multi-scale problem (from a time and length-scale perspective) intimately influenced by microstructural features that determine the early stages of crack propagation. Prediction of fatigue life is traditionally based on the evaluation of macroscopic mechanical fields at the structure level and on the application of empirical rules. However, these structure-oriented methods are material-specific and do not consider the material variability at lower scales. Hence, reliable prediction of fatigue performances and its variability requires on one side the characterization and quantification of early damage mechanisms and on the other side the incorporation of local microstructural attributes and deformation mechanisms at the grain scale into microstructure-sensitive models. The present study aims at investigating the fatigue behavior of a Ti-6Al-4V alloy through a combination of experimental and numerical works. At first, fatigue crack formation and early growth are measured by means of in situ optical microscopy observation during load-controlled fatigue experiments. The effect of microstructural attributes (phase distribution, crystal orientations…) on crack initiation and propagation are then quantified through a combination of scanning electron microscopy (SEM) and electron back-scattered diffraction (EBSD) measurements. Finally, the local plastic state at the grain scale is investigated by crystal plasticity finite element (CPFE) simulations of polycrystalline aggregates. The model is calibrated against strain-controlled cyclic experiments using a Gaussian process regression combined with a Markov chain Monte Carlo (MCMC) method for the finding of the global optimum. Mesoscopic critical plane fatigue criterion for crack initiation is finally evaluated and compared with experimental results.Cite This Article
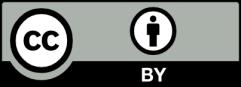
This work is licensed under a Creative Commons Attribution 4.0 International License , which permits unrestricted use, distribution, and reproduction in any medium, provided the original work is properly cited.