Open Access
ABSTRACT
Evaluation of Fatigue Performance in Welded Structures by Microstructure-Based Simulation
Department of Materials Engineering, The University of Tokyo, 7-3-1 Hongo, Bunkyo-ku, Tokyo 113-8656, Japan.
*Corresponding author: Takayuki Shiraiwa. Email: .u-tokyo.ac.jp.
The International Conference on Computational & Experimental Engineering and Sciences 2019, 22(2), 124-124. https://doi.org/10.32604/icces.2019.05311
Abstract
The purpose of this study is to evaluate fatigue performances of welded structures using numerical simulations. The fatigue life of welded joint is complicatedly affected by various factors such as geometries, defects, residual stress and microstructure. Conventional fatigue life assessments are generally based on fracture mechanics and predict the fatigue life for long crack propagation. In order to predict the total fatigue life more accurately, it is necessary to consider the lifetime for crack initiation and microstructually short crack (MSC) growth. In this study, a numerical framework to predict the fatigue life including crack initiation, MSC growth and long crack growth has been developed by several computational techniques. In the framework, the distributions of grain size and shape near the weld toe were estimated from a coupled finite element simulation of heat transfer and phase transformation in welding. The microstructural model was reconstructed by a tessellation method with the grain size distribution, and the mesoscopic stress field analysis was carried out by crystal plasticity finite element method (CPFEM). The crack initiation life was calculated based on the Tanaka-Mura model which considers the local plastic shear strain amplitude over potential crack paths. The MSC growth rate was analyzed by a phenomenological model which takes into account the grain boundary resistance and plastic shear strain at the crack tip. The prediction results for crack initiation and total fatigue life were compared with experimental data. Also, the sensitivities of various factors on fatigue life will be discussed through the uncertainty propagation analysis using the developed numerical framework.Cite This Article
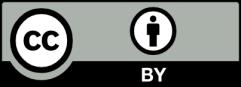
This work is licensed under a Creative Commons Attribution 4.0 International License , which permits unrestricted use, distribution, and reproduction in any medium, provided the original work is properly cited.