Open Access
ABSTRACT
A Failure-Predicting Intelligent PYTHON (IP) Code for Monitoring A Crack of Irregular Shape in A Pipe#
The International Conference on Computational & Experimental Engineering and Sciences 2019, 21(2), 45-45. https://doi.org/10.32604/icces.2019.05432
Abstract
When a small crack is detected in a pressure vessel or piping, we can estimate the fatigue life of the vessel or piping by applying the classical law of fracture mechanics for crack growth if we are certain that the crack growth exponent is correct and the crack geometry is a simple plane. Unfortunately, for an ageing vessel or piping, the degradation will change the crack growth exponent, and the crack will advance not in a simple planar fashion. To validate the crack growth exponent for an ageing vessel or piping with a crack of an irregular shape, we design an intelligent PYTHON (IP) code to do three tasks: (1) the code will re-mesh the region in the neighborhood of the advancing crack such that the irregular shape will be preserved, (2) the code will not only use the crack length and orientation measurements in a parametric formulation of a new mesh, but also embed a matching algorithm to compare the crack tip stress of the predicted (old model + new crack geometry) vs. a re-meshed (iterated new model + new crack geometry) FEM stress analysis result in order to find a new and possibly more correct crack growth exponent of the fatigue life model (super-parametric), and (3) the matching algorithm is expected to continue as more crack geometry information comes in such that the crack growth exponent is expected to converge to a stable value. The IP-assisted continuous monitoring program, using PYTHON as the management tool, TRUEGRID as the topological crack meshing tool, and two finite-element analysis codes for verifiable stress analysis, is capable of predicting more accurately the fatigue life of a cracked vessel or piping because the material model has a field-validated and, therefore, a pipe-or-vessel-specific crack growth exponent. Significance and limitations of this IP-assisted approach are presented and discussed.Cite This Article
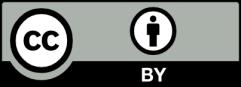
This work is licensed under a Creative Commons Attribution 4.0 International License , which permits unrestricted use, distribution, and reproduction in any medium, provided the original work is properly cited.