Open Access
ABSTRACT
Cohesive Elements Compatible with Large Shell Elements for Efficient Composite Delamination Analyses
The International Conference on Computational & Experimental Engineering and Sciences 2011, 20(2), 37-38. https://doi.org/10.3970/icces.2011.020.037
Abstract
Predicting arbitrary delamination in laminar composites remains a significant numerical challenge in composite engineering [1,2]. Currently the major technical difficulty is to predict accurately when (at what load level) and where (in which interface) should delamination occur within a pristine composite laminates upon loading. Linear-elastic-fracture-mechanics (LEFM) based methods have limits because 1) requirement of known or assumed initial flaws of finite size, and 2) unknown crack-tip singularity functions for interfaces that bond non-orthogonal plies. Numerical tools based on LEFM such as virtual crack closure technique (VCCT) suffer from serious numerical problems including numerical instability and robustness.Cohesive-zone-models (CZM) based simulation technique can effectively circumvent such difficulties and it has been used for a wide variety of nonlinear fracture problems in many engineering materials [1-3]. However, an inconvenient truth of this method for composite delamination analysis is that, the traction-separation laws that governs the damaging process requires very refined mesh at crack tip region: a mesh resolution < 1/3
{}{} 1/5 of the cohesive zone size is needed to achieve reasonable numerical accuracy and stability. Thus for an evolving delamination crack, virtually the entire composite laminate has to be discretized with a fine mesh. This is prohibitively expensive given that the cohesive zone size of a typical PMC is on the order a 1 mm.
On the other hand, for composite laminates structural plate/shell elements are preferred whenever possible because they offer the advantage of using large elements while maintaining adequate numerical accuracy. It is therefore highly desirable to combine plte/shell elements and CZ elements for delamination analyses. Unfortunately, the strict mesh restriction in using cohesive elements greatly negates the benefits of large aspect ratio shell elements.
This study explores effective numerical means that enable the use of cohesive elements together with large plate/shell elements for effective composite delamination analysis. We shall start with investigating the effectiveness of various cohesive integration method, including the commonly used Newton-Cotes method (NCI), Gaussian integration method (GI), and the recently developed mixed Gaussian and Sub-domain integration method (mixed GI & SDI). The root cause of numerical inaccuracy when such methods are used with large plate/shell elements will be identified and possible numerical remedies discussed. A novel integration method that can dramatically improve the numerical accuracy will be proposed and discussed. The improved numerical accuracy and robustness will be demonstrated through several examples of interest to composite engineering. Finally, we shall show that the new method enables the use of much relaxed plate/shell element meshes up to 2 times the cohesive zone size - an order of magnitude increase compared to traditional CZ elements.
Cite This Article
APA Style
Hua, Q., Chen, W., Yang, Q. (2011). Cohesive elements compatible with large shell elements for efficient composite delamination analyses. The International Conference on Computational & Experimental Engineering and Sciences, 20(2), 37–38. https://doi.org/10.3970/icces.2011.020.037
Vancouver Style
Hua Q, Chen W, Yang Q. Cohesive elements compatible with large shell elements for efficient composite delamination analyses. Int Conf Comput Exp Eng Sciences. 2011;20(2):37–38. https://doi.org/10.3970/icces.2011.020.037
IEEE Style
Q. Hua, W. Chen, and Q. Yang, “Cohesive Elements Compatible with Large Shell Elements for Efficient Composite Delamination Analyses,” Int. Conf. Comput. Exp. Eng. Sciences, vol. 20, no. 2, pp. 37–38, 2011. https://doi.org/10.3970/icces.2011.020.037
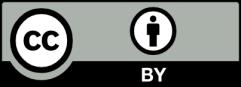
This work is licensed under a Creative Commons Attribution 4.0 International License , which permits unrestricted use, distribution, and reproduction in any medium, provided the original work is properly cited.