Open Access
ABSTRACT
TRANSPORT COMPOSITE WING BOX TRADE STUDY USING FE TECHNOLOGIES
The International Conference on Computational & Experimental Engineering and Sciences 2011, 19(2), 37-38. https://doi.org/10.3970/icces.2011.019.037
Abstract
Recently composite materials are widely used in the building of transport airplanes. The first significant application of composite materials in commercial transports was an all composite rudder for A300/310 by Airbus in 1983. In 1985, Airbus introduced a composite vertical tail fin in the same airplanes. With the success of A300/310, Airbus introduced a full composite tail structure for A320. The composite weight of A320 is totaled to 15% of structure weight. In the late of 1970, NASA and major airframe companies such as Boeing, Lockheed, MD started the ACEE program. The main goal of this program was to reduce airframe structure weight by using composite materials. With the ACEE program, the empennage of B737 was replaced by composite materials, MD developed a full composite wing for commercial transport, and Lockheed designed new composite vertical tail and aileron for L1011. In the US, the most significant use of composites in commercial transports has been on the B777. Composite structures make up 10 percent of the structure weight of the B777. The empennage, floor beams, flaps and outboard aileron of B777 were developed by composite materials. Composite materials are used for fuselage and wing structures for recently developed commercial transports by Airbus and Boeing. The composite weight percentage of A350 and B787 will be more than 50%. Both airplanes adopted composite materials for wing box and fuselage structures.In the early stage of airplane development, trade studies on many possible structure concepts are main job for structure engineers. Structure engineer team studies the possibility of adapting the state of art technologies for their new aircraft. New concepts are introduced to the conventional airframe constructions. In the trade study, weight and cost between conventional concept and new technologies are main items. In this point of view, composite wingbox concepts are estimated for the 90 seats turboprop transport airplane in this work. The wing of 90 seats turboprop transport is designed as an upper wing type. The wing consists of a center wing box, two outer wingbox at the right and left sides, leading edge and trailing edge, inboard and outboard flaps, and ailerons. The wingbox consists of front and rear spars, upper and lower cover panels and ribs. For the first work of this development, 3D digital model of the wing airframe was constructed using CATIA. Then, aerodynamic, inertia and control loads were calculated for the initial sizing using 2D panel methods and point mass models of 3D CATIA model. Based on this 3D CAD data, FE analysis model was constructed. Almost all structures including skin panels, ribs, spars, leading edge, trailing edge and control surfaces were modeled in 2D shell elements by MSC/PATRAN while some skin stringers were modeled in 1D element. Although the material properties are not different along spanwise direction in this FE model, elements were divided to some groups to be used in the HyperSizer program.
The internal loads which were calculated by the FE analysis were used for the detail sizing for each structure components. For this purpose, HyperSizer program was used for structure sizing and concept proofs. This commercial program provides structurally optimized results for the panel and beam components based on the initial FE model. Various concepts were considered and validated for the wing box. For the skin panel and stringer structure, several different stringer concepts for the skin panel were considered such as T-shaped, C-shaped and blade type stringers. The optimal stringer spacing was another design variable to be optimized by the HyperSizer program. For the rib structure, full composite and metal were constructed and compared in the cost and weight. In addition, two different composite spars were considered; one is the one piece spar with cocured/cobonded stiffeners and the other is the three pieces spar with mechanically fastened stiffeners. Through this work, the overall weight and manufacturing cost were estimated for each concepts and the optimal structure concept was suggested for the overall wing airframe construction.
Cite This Article
APA Style
I.S.Hwang, , W.Kang, (2011). TRANSPORT COMPOSITE WING BOX TRADE STUDY USING FE TECHNOLOGIES. The International Conference on Computational & Experimental Engineering and Sciences, 19(2), 37–38. https://doi.org/10.3970/icces.2011.019.037
Vancouver Style
I.S.Hwang , W.Kang . TRANSPORT COMPOSITE WING BOX TRADE STUDY USING FE TECHNOLOGIES. Int Conf Comput Exp Eng Sciences. 2011;19(2):37–38. https://doi.org/10.3970/icces.2011.019.037
IEEE Style
I.S.Hwang and W.Kang, “TRANSPORT COMPOSITE WING BOX TRADE STUDY USING FE TECHNOLOGIES,” Int. Conf. Comput. Exp. Eng. Sciences, vol. 19, no. 2, pp. 37–38, 2011. https://doi.org/10.3970/icces.2011.019.037
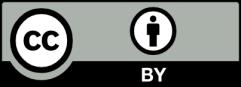
This work is licensed under a Creative Commons Attribution 4.0 International License , which permits unrestricted use, distribution, and reproduction in any medium, provided the original work is properly cited.