Open Access
ABSTRACT
FLOW CONTROL RESEARCH AT NASA GLENN FOR GAS TURBINE ENGINES
NASA Glenn Research Center, Cleveland, OH
The International Conference on Computational & Experimental Engineering and Sciences 2011, 18(4), 107-112. https://doi.org/10.3970/icces.2011.018.107
Abstract
Flow control is used on aerodynamic surfaces to improve flow quality by reducing or eliminating undesirable flow features such as thick boundary layers and possible flow separation that lead to large energy losses resulting in negative impact on performance of the flow device. As the demand for more efficient gas turbine engines increases in the future, flow control technology in various components of the engine will be critical in enabling the future designs to meet the necessary performance requirements.Technology advancement in gas turbine engines used for aerospace propulsion has been focused on achieving significant improvement in thrust-to-weight ratio as well as component and system efficiencies with the overall goals of reducing engine weight, fuel burn, emissions, and noise. Infuture, to meet ever-increasing stringent noise, emission, and fuel burn reduction goals, different airframe and engine architectures compared to the conventional tube and wing configurations need to be considered. One such advanced configuration is the hybrid wing-body (or blended wing body) airframe with embedded distributed propulsion system. In addition to the benefits of large bypass ratio of distributed propulsion and additional benefit of higher propulsion efficiency due to boundary layer ingestion, a number of technical challenges such as the effect of flow field distortion due to the embedded nature of the engine inlets and boundary layer ingestion on engine performance and strategies to mitigate the detrimental impact on performance and life need to be addressed as part of the technology advancement. In addition, to realize higher thermal efficiency, high pressure core engine technology and the complexities of technical challenges such as small blade heights and tight clearance requirements in the aft stages of compressors as well as NOx challenge due to high temperatures in combustion chambers are some of the advanced technology candidates considered for active research.
At a component level, these goals translate to aggressive designs of all the engine components well beyond the state of the art. Compressors and turbines would need highly loaded turbomachinery blades resulting in dramatic increase of work absorption/output of compressor/turbine without unduly increasing rotational speed and maintaining high efficiencies as well as adequate stable operability margins. Inlets and nozzles should be able to diffuse and expand the flow in much smaller regions maintaining minimum total pressure losses and satisfying operability, cost, weight, signature, life, and acoustic requirements at the same time. Combustor designs need to deliver targeted emission reductions through efficient combustion at lower peak temperatures in order to eliminate or significantly reduce NOx, CO2, and unburnt hydrocarbons. All these advancements invariably need some type of flow control technology in each of the components mentioned above. Objective of this paper is to present an overview of the flow control research currently underway at NASA Glenn Research Center. Some representative results of application of the flow control technologyfor variousengine components such ascompressors, combustors, turbines, inlets, and nozzles are presented in the following paragraphs.
Cite This Article
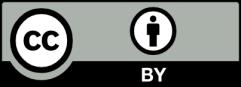
This work is licensed under a Creative Commons Attribution 4.0 International License , which permits unrestricted use, distribution, and reproduction in any medium, provided the original work is properly cited.