Open Access
ABSTRACT
Analysis Tools for Robust and Cost Efficient Design of Composite Structures
The International Conference on Computational & Experimental Engineering and Sciences 2011, 16(3), 69-70. https://doi.org/10.3970/icces.2011.016.069
Abstract
Recent work carried out at the Institute of Structural Analysis of the Leibniz University Hannover in the field of composite materials and composite structures is presented. Analysis tools for composite materials and structures are under development, which enable a robust and cost efficient design. Three key areas for design and analysis of composite structures will be covered in the presentation, namely strength, stability, and fatigue analysis.Predicting the material properties of imperfect composite structures with manufacturing defects such as waviness defects or porosities is still an open challenge. Several analytical approaches exist to determine the reduction of elastic properties due to porosity. However, these analytical methods do not account for the spatial distribution and the geometry of the voids. Size, shape, location and geometric distribution of the voids significantly influence the effect of porosity defects on material properties. A continuum damage mechanics approach is chosen to model porosity defects. Elastic-plastic material models for epoxy resin and fiber bundles have been developed. An invariant based quadratic failure criterion is used to model damage propagation. These material models are applied to study the failure modes induced by porosity defects and to obtain reduced homogenized material parameters for the macro scale. Different failure modes, such as kink-band failure can be observed and give valuable insight on the micromechanical behavior of imperfect structures. It is shown that the fiber misalignment angle has a significant influence on strength reduction.
The load carrying capability of axially compressed composite cylindrical shells is dependent on imperfections like geometric deviations from the perfect shell or loading imperfections. The scattering of imperfections induces that the buckling load is randomly distributed. Knowledge about the distribution of buckling load allows an efficient and save design of cylindrical shells. The stochastic distribution can be predicted with purely numerical methods like Monte Carlo simulation, which require a multitude of buckling load calculations. A fast semi-analytic procedure is presented, that predicts the distribution of buckling load with the same accuracy as a Monte Carlo simulation, but requires much less computational effort.
In order to improve the fatigue analysis of large structures made of fiber-reinforced plastics, a physically motivated fatigue assessment procedure is investigated. In contrast to the analysis procedure usually applied the novel model consists of a layer-wise continuum mechanics approach on the macro scale and considers different failure modes. The approach subdivides into two analysis parts: discontinuous quasi-static degradation and continuous fatigue degradation. The discontinuous approach is based on a well-known failure mode theory. The continuous degradation approach makes use of an energy-based hypothesis, which combines strength and stiffness degradation. With the present approach stress redistributions and sequence effects can be investigated.
Cite This Article
APA Style
Rolfes, R., Czichon, S., Kriegesmann, B., Kruger, H., Vogler, M. et al. (2011). Analysis Tools for Robust and Cost Efficient Design of Composite Structures. The International Conference on Computational & Experimental Engineering and Sciences, 16(3), 69–70. https://doi.org/10.3970/icces.2011.016.069
Vancouver Style
Rolfes R, Czichon S, Kriegesmann B, Kruger H, Vogler M, Jansen E. Analysis Tools for Robust and Cost Efficient Design of Composite Structures. Int Conf Comput Exp Eng Sciences. 2011;16(3):69–70. https://doi.org/10.3970/icces.2011.016.069
IEEE Style
R. Rolfes, S. Czichon, B. Kriegesmann, H. Kruger, M. Vogler, and E. Jansen, “Analysis Tools for Robust and Cost Efficient Design of Composite Structures,” Int. Conf. Comput. Exp. Eng. Sciences, vol. 16, no. 3, pp. 69–70, 2011. https://doi.org/10.3970/icces.2011.016.069
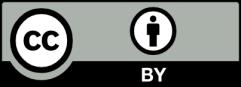
This work is licensed under a Creative Commons Attribution 4.0 International License , which permits unrestricted use, distribution, and reproduction in any medium, provided the original work is properly cited.