Open Access
ABSTRACT
Ultrasonic Fatigue Properties of Age-hardened Al Alloy in High Humidity
The International Conference on Computational & Experimental Engineering and Sciences 2011, 16(1), 3-4. https://doi.org/10.3970/icces.2011.016.003
Abstract
Abstract Al alloys have been widely used as engineering materials in many machines and structures because of their excellent properties such as high specific strength, high resistance to corrosion and easy to recycle. Especially, high strength Al alloys are effective to reduce environment load through achieving low fuel consumption in automobile engines. On the other hand, high strength Al alloys have no definite fatigue limit and their fatigue strengths are very low in comparison with their high static strengths. It is important to know the fatigue strength of high strength Al alloys in the long life region beyond 107 cycles to ensure strength integrity for long-term service. However, fatigue test over 107 cycles is a time consuming task that will take days and months. Ultrasonic fatigue test, therefore, is one of attractive methods in terms of time saving, though many problems such as the effects of loading frequency and environmental conditions need to be clarified. In the present study, in order to investigate the availability of ultrasonic fatigue technology for the evaluation of fatigue properties of Al alloys under conventional loading frequency, fatigue tests under both ultrasonic frequency (20kHz) and rotating bending (50Hz) were carried out for an age-hardened Al alloy 7075-T6 in seven kinds of humidity controlled environments, i.e. 25, 50, 70 and 85% humidity, distilled water, oxygen gas and nitrogen gas, respectively. Although fatigue strength decreased slightly at humidity below 60-70%, significant degradations occurred above that level of humidity, irrespective of the fatigue frequency. However, the degradation mechanisms involved in the rotating bending fatigue and the ultrasonic fatigue are different. In the rotating bending fatigue, the acceleration of crack growth due to brittle fracture was the main reason for the decrease in fatigue strength. In the ultrasonic fatigue, however, the transition from tensile mode to shear mode cracking accompanied with glide plane decohesion and voids formation was responsible. The change in crack growth mode was obvious from the dominated fracture morphologies corresponding to each crack growth.Keywords
Cite This Article
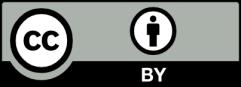
This work is licensed under a Creative Commons Attribution 4.0 International License , which permits unrestricted use, distribution, and reproduction in any medium, provided the original work is properly cited.